-
-
News
News Highlights
- Books
Featured Books
- pcb007 Magazine
Latest Issues
Current IssueSales: From Pitch to PO
From the first cold call to finally receiving that first purchase order, the July PCB007 Magazine breaks down some critical parts of the sales stack. To up your sales game, read on!
The Hole Truth: Via Integrity in an HDI World
From the drilled hole to registration across multiple sequential lamination cycles, to the quality of your copper plating, via reliability in an HDI world is becoming an ever-greater challenge. This month we look at “The Hole Truth,” from creating the “perfect” via to how you can assure via quality and reliability, the first time, every time.
In Pursuit of Perfection: Defect Reduction
For bare PCB board fabrication, defect reduction is a critical aspect of a company's bottom line profitability. In this issue, we examine how imaging, etching, and plating processes can provide information and insight into reducing defects and increasing yields.
- Articles
- Columns
- Links
- Media kit
||| MENU - pcb007 Magazine
Estimated reading time: 3 minutes
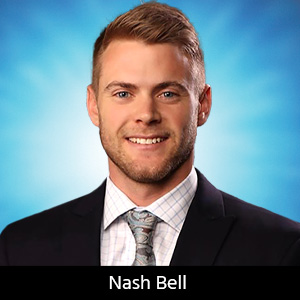
Knocking Down the Bone Pile: Solder Mask Repair Techniques for PCB Repair
One of the most common physical repairs1 (restoring functional capability of a defective PCB while not complying to meet original specifications) on a PCB is the repair of solder mask. Solder mask’s purpose is to prevent solder from flowing from one point to another during the original assembly process. Damage to solder mask (Figure 1) can be aesthetic or functional in nature, such as the case when the mask preventing solder from flowing down the “dog bone” of a BGA causes the BGA ball solder joint to be “starved,” thereby causing a defect.
There are several ways in which solder mask can become damaged. Missing mask can occur due to a breakdown in the mask adhesion to the PCB. Mask can also become damaged when an uncontrolled heat source and solder braid is used to remove solder from a pad location, thereby scratching off the mask. In cases where the mask is exposed to a high number of heat cycles, the mask can become brittle and break down (Figure 2). Poorly adhered solder mask may cause solder shorts, other soldering anomalies, or result in solder mask flowing down the dog bone from a BGA pad.
Solder mask can be repaired using one of several different techniques, each with its own advantages and disadvantages. One method, as outlined in IPC 7721 2.4.1, is via the use of liquid solder mask. This can be spread onto the areas that need repair. This replacement mask is then either heat- or UV-cured. After reading the manufacturer’s directions, UV-cured solder mask is selectively applied and placed underneath the UV lamp of the right wavelength. Based on the output of the UV lamp (which can be measured using a radiometer) a cure time for the given solder mask along with lamp-mask distance, a controlled process can be documented by the repair technician.
Another method (Figure 3) is a simple technique for “spot” solder mask repair by using a repair “pen” (IPC 7721 2.4.1) which is typically cured by air drying or a bakeout cycle. The liquid oozes out of the soft-tipped pen and then can be air- or heat-cured. The pen tips themselves are large with respect to the size of modern BGA pads, making it a challenge to precisely dispense the mask material. Due to the porous nature of the dispensing tip, it tends to pick up debris from the board (including flux residue, remnant mask, and cleaning agents). This soaked-up debris then can re-contaminate other areas of the board. The skill level for someone making solder mask repairs using this technique will need to be at the advanced level and, even so, the repair aesthetics tend to be low compared to the technique outlined in IPC 7721 2.4.1.
In addition to this repair pen method there is another technique which repairs the mask underneath the BGA using a polyimide, adhesive-backed, stay-in-place stencil. This serves as a reliable way to place the BGA while simultaneously repairing the mask. This stencil, while having the benefit of being a simple way to place a BGA, also provides isolation between pads and prevents shorting between the IO. This will fix the standoff height between the base of the BGA and the PCB to control collapse height, while serving as a mask “band-aid.” Once in place, the stencil acts like a solder mask repair stencil. This allows even the beginning repair technicians to repair damaged solder mask underneath the BGA.
Lastly, there is the mask repair stenciling technique (Figure 4). This method saves repair time when a large area requires mask repair. An ultra-thin stencil defines the area where the mask is repaired. Replacement mask material is squeegeed into the stencil apertures and then cured. Post curing, the stencil is peeled away, leaving hardened replacement mask in its path. This method, while time saving for multiple boards requiring the exact same area of repair or for a very complex large area of repair, requires a repair technician with an advanced skill level.
Like all PCB repairs, the customer must need to be informed if mask repair is called for in repairing the PCB. There are many techniques depending on the purpose of the assembly, the cost, and the complexity of the mask repair required.
References
- “Rework, Modification and Repair of Electronic Assemblies,” IPC-7711C/7721C, IPC January 2017.
This column originally appeared in the March 2022 issue of SMT007 Magazine.
More Columns from Knocking Down the Bone Pile
Knocking Down the Bone Pile: Addressing End-of-life Component Solderability Issues, Part 4Knocking Down the Bone Pile: Tin Whisker Mitigation in Aerospace Applications, Part 3
Knocking Down the Bone Pile: Gold Mitigation for Class 2 Electronics
Knocking Down the Bone Pile: Basics of Component Lead Tinning
Knocking Down the Bone Pile: Package on Package Rework—Skill Required
Knocking Down the Bone Pile: 2023’s Top Challenges in BGA Rework
Knocking Down the Bone Pile: Eliminating Solder Balls in Hand Soldering
Knocking Down the Bone Pile: Opening a Trace on the Surface of a PCB