-
- News
- Books
Featured Books
- smt007 Magazine
Latest Issues
Current IssueWhat's Your Sweet Spot?
Are you in a niche that’s growing or shrinking? Is it time to reassess and refocus? We spotlight companies thriving by redefining or reinforcing their niche. What are their insights?
Moving Forward With Confidence
In this issue, we focus on sales and quoting, workforce training, new IPC leadership in the U.S. and Canada, the effects of tariffs, CFX standards, and much more—all designed to provide perspective as you move through the cloud bank of today's shifting economic market.
Intelligent Test and Inspection
Are you ready to explore the cutting-edge advancements shaping the electronics manufacturing industry? The May 2025 issue of SMT007 Magazine is packed with insights, innovations, and expert perspectives that you won’t want to miss.
- Articles
- Columns
- Links
- Media kit
||| MENU - smt007 Magazine
ProMetrics: An Easy, Smart Solution
January 5, 2022 | I-Connect007 Editorial TeamEstimated reading time: 12 minutes
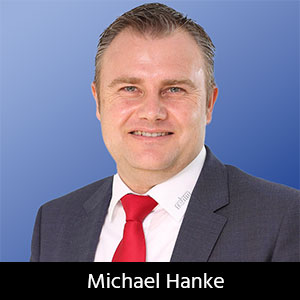
Rehm's Michael Hanke speaks about the product on process and the advantages of live process monitoring with ProMetrics, Rehm’s newest monitoring tool, which is brand new and unique in the market. Users say that it’s easy to use and, more importantly, that it provides the security in a system they are looking for.
Barry Matties: Michael, what do you see as the objective of a production process?
Michael Hanke: I think it’s very important to have a smart product because in our production these days, machines must be much more intelligent. Typically, the operators must be at the machine all the time—something that is very hard to do. For that reason, more systems must be equipped with more intelligent components to guarantee a smart production channel.
Matties: Rehm’s equipment is in the thermal area. Brief us on the type of equipment that your company o?ers and the services you provide.
Hanke: We focus on the production of thermal systems in the field of reflow soldering systems with convection or condensation as well as drying and coating systems and cover a temperature range from -50°C on up to 1,000°C. For our customers we also realize customized applications around soldering, coating, and curing of assemblies. As high temperatures are an important factor in terms of energy consumption, we make a point of ensuring that our systems have the necessary features to produce as energy-efficiently as possible. The new ProMetrics monitoring tool can contribute to this.
ProMetrics is a graphics tool that shows the actual process on each board. Each board is mirrored by the sensors, and you see the results immediately on the screen through a live system. You can see the pro?le and what’s important is you see the borders—like a lane assist in the car. You can see both the upper and bottom side, and you should stay in between with your temperature profile. Being in the middle is the most e?cient way for your production. Unique with our system is that you see not only a ?gure, with ProMetrics a graph is visualized on the system monitor. We can also optimize the system for each company’s needs. So, if you want to reduce the temperature by ?ve or 10 degrees, it’s in your corridor. This is a possibility to save the emissions; one step ahead to a carbon?neutral production. This is the target for an efficient production.
Matties: When you talk about real?time monitoring, is the equipment able to make modi?cations or process parameters adjustments on the ?y, or is that still driven by the operator?
Hanke: It is important that the operator and the process engineer know the limits of the machine. These experts know exactly what limits need to be set for the product. ProMetrics responds with alerts when the actual profile reaches or exceeds the limits, but the machine will not make changes or adjustments on its own. That is not the goal we are pursuing. The process engineers have the knowledge to make the adjustments and the range of the process window is dictated by the part con?guration. This is known to the process engineers when setting the profile parameters.
Matties: How important is it to integrate a profiling supervision tool in every production environment?
Hanke: Today you have a higher product variety, and a profiling monitoring tool provides more safety in your production. At the heart of ProMetrics are sensors that are precisely attached to appropriately defined measuring pucks. These sensors have a high measurement accuracy. ProMetrics is a monitoring tool that provides live data and live information on the screen that you can easily forward to your MES system. The MES system is directly connected to ProMetrics, and easily supports this live data. This overview is unique and ensures that production operations are always in safe mode.
Solder Star is a strong partner that provides the pro?ling. It’s important to note that when you have a new product, you pro?le the system only once, then you just supervise, and no extra work is needed.
Matties: Now, common defects tend to be around the solder joint. How is this helping in the reliability of the ?nished product?
Hanke: When it comes to reliability, it’s important that we have a 100% live test, live monitoring. That process is driven dramatically by having a stable temperature with stable nitrogen gas ?ows. This ?ow is checked by the sensors using ProMetrics. This software is the umbrella over the complete process, which checks from the beginning through to the cooling process.
Matties: And how does this communicate the data?
Hanke: We are very ?exible. This system works with Hermes and with the new interface CFX, so it means horizontal conversation and communication are guaranteed. And the vertical communication to the MES is guaranteed. It is a closed loop. This is a fantastic way to share the data transparently, and the data is always accessible.
Nolan Johnson: When you ’re optimizing, are the process windows getting a more e?cient use of thermal pro?ling, etc.?
Hanke: Yes.
Johnson: Does that help speed up the throughput? Are you getting more pieces per hour through?
Hanke: Good question. The customer needs to have ways to save power consumption on each board; in general, he can optimize the throughput because he sees how the process is going with each board. In he is in this process window, he can speed up the production. Ten to 15% is easily possible. When you optimize it, 20% more throughput is possible. It makes a big di?erence because you don’t need extra insulation or upgrades; you only need the ProMetrics. That’s all; no additional fan speeds, motors, nothing. You optimize your existing system.
Matties: So just to be clear, this is something I can add onto the system that’s already in my factory?
Hanke: Yes.
Matties: What’s that process, and how long would it take to implement?
Hanke: For the implementation, you need only the external sensors, such as for thermocouples and you need the software integration. It can be done within a few hours. That’s all.
Matties: That’s great. And the data storage is all done through the network of the system, or is it to some external system?
Hanke: You don’t need an external system. We use the network as storage. That means if you have a server or it’s cloud?integrated, the data storage can be copied to the cloud.
Matties: Now, ProMetrics is only compatible with your equipment, correct. It’s not compatible with others?
Hanke: Yes. We can do the integration with our ViCON software. This is a smart touch?based Windows software which is developed by Rehm in combination with ProMetrics and no additional interfaces are needed. It provides security in that way. You can use the ProMetrics on the Rehm systems.
Matties: What has the response been to this?
Hanke: It has been great, particularly because of its security. This is the most important question asked by new customers, especially those in the automotive industry that now leads the electronics market. They need things to be secure. They have experts, but they need the highest security on each board. Now they trust the software solution, which is easy to integrate. When I highlighted at the show that the complete traceability function is integrated, the response was, “Wow, this is perfect for me because I can see what’s going on. Not only the numbers, but I really see it.” This is not an Excel ?le; it’s a real graphic overview. And this is fantastic to understand.
Matties: When people come to examine the software, what’s the most typical question you have?
Hanke: The most important question was probably how to look at the process when there’s no camera system in a re?ow. And that’s true; you cannot open the re?ow during the process, so how do you see what’s going on inside? ProMetrics has the solution with smart software to see what’s going on in the process and have the live data. This is important.
Matties: And from the customer, what’s the most important question that they ask you?
Hanke: That would probably be asking if the system is reliable. They want to make sure someone can’t just switch it o?, but if they have con?gured it so it will run all the time, like a virus scan on your Windows PC. They want a perfect system.
Johnson: Michael, do you have customers who are wanting to turn the system o??
Hanke: This question came up, especially in West Coast countries with customers that run a night shift. Some of those guys will switch o? or play with the software, and this is not allowed. At the user level, the operators can start and stop the process, but not start and stop the supervision of the process. This is very important. Like a lane assist or braking system in the car; you cannot switch it o?. Now it’s integrated, and this helps to secure a process in West Coast countries.
Johnson: You’re sharing information to the MEMS. Do you also see the need for this information that you’re gathering to be shared up and down the line with other machines?
Hanke: In general, it is important to have the information from the complete line production in a graphical way because of the way human think and see things. It’s easier to understand instead of thousands of numbers.
I’m personally interested in pictures, and when you see these tables and diagrams rising, it’s easier to understand, especially the process window curve. It’s easier to understand and you see it in a simple way from a cockpit, in a smart overview. For example, something comes up, like a temperature goes closer to the border and you can correct it immediately. This an easy and smart solution.
Matties: It looks like this product came out just this year, right?
Hanke: Yes, it’s brand new.
Matties: How many installations do you currently have?
Hanke: In the past year and a half, we have had about 10 key customers. It’s important to note that the pro?ler is Solar Star, which has been in the market for many years and is a global player. It enables us to combine the pro?ling with the software integration easily. Now, we received hundreds of requests from productronica.
Matties: What sort of feedback have you had from the early adopters, and what sort of changes, modi?cations, or improvements were they looking for?
Hanke: In general, they were looking for improvements, particularly that the machines can be self?optimized with key components or AI components, and augmented intelligence. That’s what we were looking for as the next step; ProMetrics is the base for our future developments.
Matties: Well, that was right in line with my ?rst question of whether this is an automated parameter control system, and it sounds like you’re right. You have the baseline for it. Now you’ll build o? that foundation.
Hanke: This is true. This is the base that we follow. And we see a future where the system self optimizes to the product to be independent.
Matties: Is there a general feeling that you’re getting from the marketplace to reduce labor input on each operation?
Hanke: This is not a reduction of labor but a smarter way to run production, because the problem is that, globally, you don’t have as many educated people as in the past, even though electronics will expand dramatically in new markets. You have to look at how easily, or how user friendly you can o?er the processing channel, not just the machine.
Matties: Well, I think, the end result does reduce labor, though. Generally, when someone is looking for an automated process or they’re looking for better yields and reduced throughput cost.
Hanke: Yes. The main drive nowadays is carbon?neutral production as part of our goal with software, sensors, and hardware. For sure, ProMetrics helps reduce carbon dioxide.
Matties: Now how’s that helping through the better control of the system generally, or are there other features?
Hanke: We have our features, the insulation, that have the best heat transfer. With this software control system and the graphical tool, then you don’t need high temperature, high power which allows you to reduce this emission dramatically, up to 25%. This makes a di?erence when we are producing 34 tons of carbon dioxide per year.
Matties: A 25% reduction in energy is a lot. With energy costs going up, that could add up pretty quickly.
Hanke: Yes. You will see the return on investment quickly on your TCO calculation, especially with the production in West Coast countries or in R&D centers where the highlights are used.
Johnson: Michael, you can retro?t systems with sensors and software. Can you also then retro?t those systems with the insulation as well?
Hanke: It depends a little bit on the age. Think of a car that is 30 or more years older; it makes no sense to optimize the engine because insulation is hard and it’s in the middle of the system. So, compared to the commercial facts, it’s not so e?cient to upgrade it in production. It’s important that we o?ered to retro?t the system if it makes sense in our company while looking for an additional machine. But, yes, in general, our system is prepared to upgrade the hardware components.
Matties: What’s the learning curve for an operator on this new system? Is it straightforward or is there training required?
Hanke: No extra training is required. I think everybody who can use a smartphone can use ProMetrics because it’s a touch?based system. We have common icons like those used for other apps, and you can see immediately the graphical result in a live mode. So why would you need extra training? We o?er training, but it’s not needed.
Matties: Do you have any ?nal thoughts or anything that we haven’t talked about that you feel we should include?
Hanke: I think the most important point is to emphasize how secure the produced boards are. This is unique in the market that every process is safe, every process is mirrored, and shown on MES systems with a graphical boundary, which you can easily identify.
Matties: Well, thank you very much.
Hanke: Thanks a lot, guys.
Suggested Items
Driving Innovation: Direct Imaging vs. Conventional Exposure
07/01/2025 | Simon Khesin -- Column: Driving InnovationMy first camera used Kodak film. I even experimented with developing photos in the bathroom, though I usually dropped the film off at a Kodak center and received the prints two weeks later, only to discover that some images were out of focus or poorly framed. Today, every smartphone contains a high-quality camera capable of producing stunning images instantly.
Hands-On Demos Now Available for Apollo Seiko’s EF and AF Selective Soldering Lines
06/30/2025 | Apollo SeikoApollo Seiko, a leading innovator in soldering technology, is excited to spotlight its expanded lineup of EF and AF Series Selective Soldering Systems, now available for live demonstrations in its newly dedicated demo room.
Indium Corporation Expert to Present on Automotive and Industrial Solder Bonding Solutions at Global Electronics Association Workshop
06/26/2025 | IndiumIndium Corporation Principal Engineer, Advanced Materials, Andy Mackie, Ph.D., MSc, will deliver a technical presentation on innovative solder bonding solutions for automotive and industrial applications at the Global Electronics A
Fresh PCB Concepts: Assembly Challenges with Micro Components and Standard Solder Mask Practices
06/26/2025 | Team NCAB -- Column: Fresh PCB ConceptsMicro components have redefined what is possible in PCB design. With package sizes like 01005 and 0201 becoming more common in high-density layouts, designers are now expected to pack more performance into smaller spaces than ever before. While these advancements support miniaturization and functionality, they introduce new assembly challenges, particularly with traditional solder mask and legend application processes.
Knocking Down the Bone Pile: Tin Whisker Mitigation in Aerospace Applications, Part 3
06/25/2025 | Nash Bell -- Column: Knocking Down the Bone PileTin whiskers are slender, hair-like metallic growths that can develop on the surface of tin-plated electronic components. Typically measuring a few micrometers in diameter and growing several millimeters in length, they form through an electrochemical process influenced by environmental factors such as temperature variations, mechanical or compressive stress, and the aging of solder alloys.