-
- News
- Books
Featured Books
- design007 Magazine
Latest Issues
Current IssueDesigning Through the Noise
Our experts discuss the constantly evolving world of RF design, including the many tradeoffs, material considerations, and design tips and techniques that designers and design engineers need to know to succeed in this high-frequency realm.
Learning to Speak ‘Fab’
Our expert contributors clear up many of the miscommunication problems between PCB designers and their fab and assembly stakeholders. As you will see, a little extra planning early in the design cycle can go a long way toward maintaining open lines of communication with the fab and assembly folks.
Training New Designers
Where will we find the next generation of PCB designers and design engineers? Once we locate them, how will we train and educate them? What will PCB designers of the future need to master to deal with tomorrow’s technology?
- Articles
- Columns
Search Console
- Links
- Media kit
||| MENU - design007 Magazine
Living in a Material World: High-Speed Design Strategies
January 13, 2022 | I-Connect007 Editorial TeamEstimated reading time: 5 minutes
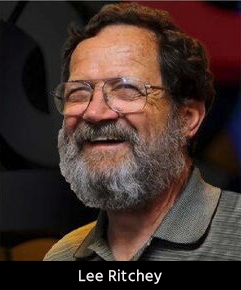
Any discussion about high-speed PCB design techniques would be incomplete without considering the properties and requirements of the materials. Your material selection drives much of your design strategy when you’re operating at 28 gigabits per second or faster.
We recently spoke with high-speed design expert Lee Ritchey of Speeding Edge, and electronic materials veteran Tarun Amla of Avishtech and Thintronics, about the relationship between advanced PCB materials and high-speed design techniques. They discuss the challenges facing designers and engineers working with materials at speeds that were considered unreachable not long ago, and what designers need to know about material selection as board speeds continue rising toward the stratosphere.
Andy Shaughnessy: Would you set the stage by explaining the last few decades of materials that got us to where we are now and how designers are having to learn these EM properties?
Lee Ritchey: I joined 3COM in 1996 where we were doing reasonably well making all the lengths work at 10 megabits per second. And then I got started working on 100 megabits, and that was thought to be pretty fast. At that point, the only thing we were worried about was reflections and crosstalk, which basically meant impedance. In the laminates, we worried about whether we could get repeatability on impedance with a cross-section. And by 1998, I helped a startup build us a product where we had the links leaving the box at a gigabit per second. That was thought to be magical, and of course it was, in that context.
It wasn’t very long before I went to a startup called Procket Networks, where all the internal signals were 3.125 gigabits per second, and that was where we first started to worry about things like loss. Until then we hadn’t worried much about any of those properties. We worried about losses because the transceiver sets were not very good, so they couldn’t tolerate much. For example, a 10 dB loss was a big number, and so that’s when we started driving the laminate manufacturers to reduce loss. At the time, the only material that was considered low-loss was Nelco 4000-13 SI, and they achieved it by using a low-loss glass. That worked just fine until the tsunami happened in Japan, and Nittobo, the one supplier of that glass, was inside the quarantine zone. Within a week none of us could build our products anymore because we were all single-sourced with that glass.
I got involved with Isola to see if we could do something about it. It wasn’t too long before we were doing 10 gigs, and it surprised me that we soon were doing 100 gigs. The current links, the undersea cables all around the world, are 400 gigabits per second, which is pretty astonishing. We are achieving that with eight links of 56 gigabits per second, which pushed every single thing about the laminates. The industry wants us to double that, and to do that we’re using PAM4 (pulse-amplitude modulation), a four-level coating so that the clock is still 28 gigahertz. For us, the loss problem is still the same, but the noise margin, because the levels are smaller, is such that the error rate is not good enough right now. This is where I’m pushing material, now that we know the industry is going to want that.
Between 1996 and 2021, we went from 10 megabits per second to 400 gigabits. That’s a 40,000X increase in bandwidth in 25 years. To do that we have pushed everything about the laminate. Tarun is probably the most renowned at doing that because he’s been the major player driving that whole thing. There are two things that I worry about. One is skew, which is glass weave that causes the two sides of the differential pair to not arrive at the same time, and then the link won’t work. The other is loss. Tarun, you can pick up the ball.
Tarun Amla: I remember around 2002 where people said that five gigabits per second was going to be unattainable in copper. There was a lot of work done around using optical channels which did not get much traction. Around that time, the RoHS lead-free legislation was coming on board, and that just added another layer of complexity, because not only did you want these signals to go through at those high data rates, but you also wanted reliable performance. Boards now had to go through 6X reflow at 260?C for qualifications. In some cases, the qualification standards are about 10X reflow or even higher. Now I’m hearing about 20X reflow, which seems weird. Why would you want to do that to your board?
We are at a crossroads where we have to look at the next generation. Sadly, finding an alternative for copper is going to be difficult with the amount of work involved. A materials—dielectric—solution has to come through, or it will be like what happened with Moore’s Law. We are at an impasse because we have reached the limits, especially with 112 gigabits per second. If you’re trying to do it with PAM4, like Lee said, the margins are lower and you’ve got this inherent skew in that signaling, so that’s where it stands. The whole industry is waiting, and whether it’s 5G or 112 gigabits per second, the stage is set for something new to happen.
Happy Holden: The people I worked with in Taiwan making the flip chip substrates have been doing 8- to 15-micron lines as a basis for almost the last 15 years. Although they use a BT core and BT prepreg, they never got very good yields once they got under 20 microns, until they switched to using the Ajinomoto build-up film. Today, all eight of the Asian manufacturers of high-density packages use the ABF material primarily because it’s a very well-engineered resident system that’s robust, but it goes down extremely flat. That planarity is required for high density of imaging and developing, as well as etching. So, 20 microns is considered about the best you can do if you use laminate and prepreg. Below that and you have to start going to these engineered liquids or films that the Japanese perfected initially, and now other sources are available for them. That’s true for the thin film.
To read this entire conversation, which appeared in the January 2022 issue of Design007 Magazine, click here.
Suggested Items
Elephantech: For a Greener Tomorrow
04/16/2025 | Marcy LaRont, PCB007 MagazineNobuhiko Okamoto is the global sales and marketing manager for Elephantech Inc., a Japanese startup with a vision to make electronics more sustainable. The company is developing a metal inkjet technology that can print directly on the substrate and then give it a copper thickness by plating. In this interview, he discusses this novel technology's environmental advantages, as well as its potential benefits for the PCB manufacturing and semiconductor packaging segments.
Trouble in Your Tank: Organic Addition Agents in Electrolytic Copper Plating
04/15/2025 | Michael Carano -- Column: Trouble in Your TankThere are numerous factors at play in the science of electroplating or, as most often called, electrolytic plating. One critical element is the use of organic addition agents and their role in copper plating. The function and use of these chemical compounds will be explored in more detail.
IDTechEx Highlights Recyclable Materials for PCBs
04/10/2025 | IDTechExConventional printed circuit board (PCB) manufacturing is wasteful, harmful to the environment and energy intensive. This can be mitigated by the implementation of new recyclable materials and technologies, which have the potential to revolutionize electronics manufacturing.
Connect the Dots: Stop Killing Your Yield—The Hidden Cost of Design Oversights
04/03/2025 | Matt Stevenson -- Column: Connect the DotsI’ve been in this industry long enough to recognize red flags in PCB designs. When designers send over PCBs that look great on the computer screen but have hidden flaws, it can lead to manufacturing problems. I have seen this happen too often: manufacturing delays, yield losses, and designers asking, “Why didn’t anyone tell me sooner?” Here’s the thing: Minor design improvements can greatly impact manufacturing yield, and design oversights can lead to expensive bottlenecks. Here’s how to find the hidden flaws in a design and avoid disaster.
Real Time with... IPC APEX EXPO 2025: Tariffs and Supply Chains in U.S. Electronics Manufacturing
04/01/2025 | Real Time with...IPC APEX EXPOChris Mitchell, VP of Global Government Relations for IPC, discusses IPC's concerns about tariffs on copper and their impact on U.S. electronics manufacturing. He emphasizes the complexity of supply chains and the need for policymakers to understand their effects.