-
- News
- Books
Featured Books
- pcb007 Magazine
Latest Issues
Current IssueInventing the Future with SEL
Two years after launching its state-of-the-art PCB facility, SEL shares lessons in vision, execution, and innovation, plus insights from industry icons and technology leaders shaping the future of PCB fabrication.
Sales: From Pitch to PO
From the first cold call to finally receiving that first purchase order, the July PCB007 Magazine breaks down some critical parts of the sales stack. To up your sales game, read on!
The Hole Truth: Via Integrity in an HDI World
From the drilled hole to registration across multiple sequential lamination cycles, to the quality of your copper plating, via reliability in an HDI world is becoming an ever-greater challenge. This month we look at “The Hole Truth,” from creating the “perfect” via to how you can assure via quality and reliability, the first time, every time.
- Articles
- Columns
- Links
- Media kit
||| MENU - pcb007 Magazine
Estimated reading time: 6 minutes
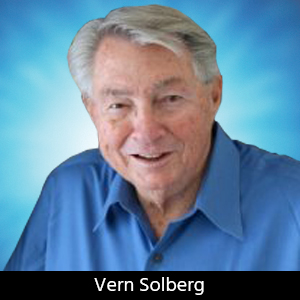
Designer's Notebook: Design for Test, Part 1
Circuit board fabricators remind us that multilayer boards will predictably have more components necessitating greater circuit routing complexities than that experienced on earlier applications. Also, with each generation of semiconductors it seems that the terminal count increases and the spacing between terminals shrinks, requiring designers to employ conductor lines and spaces that are far narrower than previously considered the norm.
Designing the circuit board for testability is a key requirement in meeting the overall design for manufacturability (DFM) criteria. Throughout the circuit board development process, the designer must contemplate the essential features required for electrical test: testing to identify PCB fabrication or assembly defects.
Design for Bare Board Testing
The circuit board is the primary platform for electronic assembly interconnect. While there are several stages within the circuit board’s fabrication process that receive meticulous inspection, the complexity of the circuit structures is increasing. Some may think that they can assess the finished printed circuit board using automated optical inspection (AOI) or magnified visual inspection, but they often find these non-contact methods limited. Except for low-density single- and two-layer circuits, multilayer circuit boards, and especially the high-density variations, will require a more sophisticated end-product verification. Certifying that the finished board is defect-free and will operate as designed, electrical bare board testing is essential.
Bare board testing involves the measurement of both capacitance and resistance of the finished circuit board.
- Capacitance testing involves testing for opens and shorts by applying current then probing each net to measure the induced capacity.
- Resistance testing measures the electrical resistance of the conductor within the net by probing both ends of the net.
The circuit board’s copper conductors will generally deliver a low resistance measurement but the measured resistance will also be impacted by the copper conductor's length and its cross-sectional area. As an example, when measuring two nets of the same material and the same cross-section, and one conductor is twice as long as the other, the longer net will deliver an increased resistance value. On the other hand, if there are two nets of the same material and even though they are the same length, if the copper conductor on one of the nets is twice as thick as the other, the thicker conductor will measure that net at half the resistance of the thinner copper conductor.
Bare Board Test Methodologies
Two methodologies are commonly applied for bare board testing: fixed probe and flying probe. Both fixed probe fixture test and flying probe testing can save the frustration of overlooking circuit board manufacturing defects. So, which test method will be best? It really depends on the volume of units to be tested and the economics of scale. When the circuit board quantity is minimal or the product is subject to further refinement or revision, the flying probe test is a logical choice. The cost of a flying probe test is calculated per unit so the cost of setup and processing will be minimal, but throughput will be slower. When the product has been stabilized, however, and the requirement is for hundreds or thousands of units per week or month, then the setup costs for developing the fixture and programming for fixed probe testing can be justified.
Fixed Probe Testing
For high-volume multilayer PCB applications, a system is commonly employed that is programmed for simultaneously testing all nets on the circuit board. The contacting fixture, referred to as bed-of-nails (Figure 1), is furnished with spring-loaded probe terminals that access every net on the finished circuit board.
In preparation for test, individual boards are placed onto a custom fixture configured with an array of probe contactors aligned to test lands provided on the board surface. For more complex circuit board applications, the board will be placed between opposing probe platforms, pressing the board from the top and bottom with hundreds of spring-loaded contactors.
The actual test cycle is very quick regarding “go and no-go” determination, but the primary benefit is the test system’s capability of identifying the failure type and specific defect location. Although fixed-probe testing is fast and efficient, the development of the dedicated fixture and testing program is costly and, if the board undergoes any changes, the dedicated panels developed to secure the probe terminals in the fixture will likely require modification or replacement.
Flying Probe Testing
Flying probe test systems can measure extremely dense designs without using dedicated fixtures. The cost of the testing is much less than fixed-probe testing but there are detractors. The flying probe test system for bare boards (Figure 2) utilizes four to eight probes and can be configured to test PCB connections from one side or two sides. These flying probes travel across the board’s surface contacting specific end-of-net lands using instructions from a software program that is developed using the board’s initial design data file.
The flying probe method, although furnishing slower cycle times when compared to fixed probe testing, eliminates the cost of fixture development, provides faster setup time, and is easily modified to meet physical change of the circuit board design.
Advantages of Flying Probe Test
- Eliminates fixture preparation costs and time
- Fast test program development; easy integration of design changes
- Process flexibility; circuit access, even in the absence of test points
- Controlled probe contact, programmable for any type of board
- Different test solutions integrated within a single test system
- Intrinsic positioning and measurement precision
Flying probe contactors, however, cannot provide the full parametric test that the fixed-probe fixture testers can provide. This will be an issue when testing hi-rel military, aerospace, and life support medical products. These products typically require simultaneous testing of the PCB for opens and more importantly, shorts. For more complex circuit board designs a dedicated fixture or multiple fixtures will be required.
Data Transfer for Bare Board Test
When preparing the bare board test program and fixturing specified for the product, the testing service will require a sample of the finished circuit board and digital file for the following items:
- Electrical schematic
- Mechanical detail
- Layer cross-section
- Net list
- CAD data (Gerber file)
The following guidelines have been furnished by Aspen Test Engineering, a prominent test fixture development specialist in Colorado:
- Provide test probe accessibility to all nets from the bottom surface of the board. When probe locations are distributed on opposite sides of the board, complexity of the fixture “introduces an entirely new tolerance stack-up and will essentially doubles the cost of fixture development.”
- In regard to test probe land size, a 0.030” (~0.75 mm) diameter land area will ensure reliable probe-to-land interface. When the probe lands must be smaller, the fixture may require “guided probes,” further increasing the test fixture’s complexity.
- Probe lands should be “no closer than 0.050” (~1.3 mm)” however, smaller probes are available, but they are generally more delicate and flexible, resulting in probe-to-land registration issues.
- Test land pattern proximity to components is also a concern. Preferred clearance from the component body to the center of the test land should be no less than 0.060” (~1.5 mm). This will enable access to the same probe locations during assembly test.
- Tooling holes must be proved to enable board to fixture alignment. The requirement is that two 0.125” (~3.2 mm) diameter non-plated tooling holes be provided in opposite corners of the circuit board.
Other tests may be required for checking isolation between conductors—shorts test. A software generated program that checks for nets that are within a tolerance set and impedance testing, measures the frequency of the current passing through conductors.
Part 2 will focus on assembly test methodologies. Low-volume assemblies, for example, may rely only on functional testing while high-volume assembly will most likely adapt some form of automated or semi-automated functional test, functional partitioning, or automated in-circuit testing (ICT).
This column originally appeared in the January 2022 issue of Design007 Magazine.
More Columns from Designer's Notebook
Designers Notebook: Basic PCB Planning Criteria—Establishing Design ConstraintsDesigners Notebook: Layer Stackup Planning for RF Circuit Boards
Designers Notebook: Addressing Future Challenges for Designers
Designers Notebook: Impact of Advanced Semiconductor Packaging on PCB Stackup
Designers Notebook: Implementing HDI and UHDI Circuit Board Technology
Designer's Notebook: Heterogeneous Integration and High-density SiP Technologies
Designers Notebook: PCB Design and IPC-CFX for Assembly Automation
Designer’s Notebook: What Designers Need to Know About Manufacturing, Part 2