-
- News
- Books
Featured Books
- pcb007 Magazine
Latest Issues
Current IssueInventing the Future with SEL
Two years after launching its state-of-the-art PCB facility, SEL shares lessons in vision, execution, and innovation, plus insights from industry icons and technology leaders shaping the future of PCB fabrication.
Sales: From Pitch to PO
From the first cold call to finally receiving that first purchase order, the July PCB007 Magazine breaks down some critical parts of the sales stack. To up your sales game, read on!
The Hole Truth: Via Integrity in an HDI World
From the drilled hole to registration across multiple sequential lamination cycles, to the quality of your copper plating, via reliability in an HDI world is becoming an ever-greater challenge. This month we look at “The Hole Truth,” from creating the “perfect” via to how you can assure via quality and reliability, the first time, every time.
- Articles
- Columns
- Links
- Media kit
||| MENU - pcb007 Magazine
Estimated reading time: 4 minutes
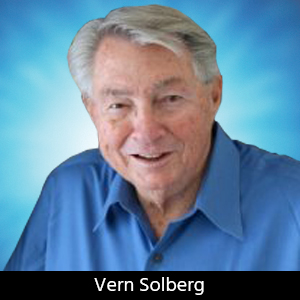
Designers Notebook: A Lesson on Automated Optical Shaping
IPC APEX EXPO show and conference was safely back in full swing after skipping 2021. Because my primary interest is printed circuit board and assembly processing, I ventured onto the show floor to review the evolution of some of the systems on exhibit that may contribute to process efficiency and end-product quality. A key benefit of attending a show like this one is that the board and assembly manufacturers can view and compare similar product offerings in one place.
One topic I was most interested in reviewing was the progress made on automated post-etch inspection of circuit board panels used for multilayer circuit boards. High-volume production environments rely on automated inspection to identify defects in the circuit pattern before the lamination process. Several automated inspection system manufacturers on the show floor demonstrated their products’ attributes and unique features. Automated optical inspection (AOI) systems use data accessed directly from the circuit board’s CAD file and rapidly checked the circuit image on each panel.
The circuit board is the platform that supports and interconnects all component elements that enable the electronic assembly to function. To accommodate the current generations of electronics, the high I/O and very fine-pitch semiconductors simultaneously minimize circuit board size, forcing designers to increase circuit layers and implement finer conductor lines and spaces for interconnect. Fabrication imperfections that occur during imaging and etching stages in the fabrication process, if not identified, may impact the circuit board’s functional integrity.
Companies have found that human inspection of the individual circuit layers consumes a significant amount of time, and even with magnification, may not identify all defects on the panel surfaces. When fabricating complex, multi-layer circuit boards, automating image verification on all circuit layers before lamination has proven indispensable. These AOI systems are programmed to identify circuit path irregularities: opens, shorts, or anomalies within the circuit paths that are outside the user-defined tolerance limits.
I had the pleasure of interviewing Chad Smith, the AOI expert representing Orbotech West. The 35-year-old company is well known for a broad range of products—including automated inspection, direct imaging for defining the PCB circuit pattern, and photoimageable solder mask coatings to precision ink jet printing. The system I found most interesting was identified as an automated optical shaping (AOS) system. This AOS system is unique because it not only locates and identifies the defects in the etched circuit pattern, it has the ability to automatically correct the defects.
As it was explained to me, the key to this process is the company’s image acquisition technology where it captures precise images of the defect area, analyzes and compares the defect shape to CAM data used to initially develop the circuit pattern image, and defines where excess copper requires ablation as well as pinpoint the location of interrupted portions of copper conductors that need to be reformed.
Eliminating excess copper, for example, shorts, protrusions, copper splashes, and excessively-sized features, is accomplished using built-in laser ablation technology. The laser reshaping process eliminates the unwanted excess copper, reforming the circuit features to the original profile defined in the CAM file. An example of a copper bridge defect and the result of laser circuit reshaping is compared in Figure 1.
Regarding copper removal, the laser process can provide reshaping down to 25 µm for both copper conductor features and the spacing separating features. As far as copper ablation speed, the manufacturer estimates that the system can identify and eliminate up to 80 bridge or short defects per hour.
Rebuilding missing conductors is another form of reshaping. This condition would have commonly forced the fabricator to scrap that portion of the multilayer board set. The capability to add copper to the laminate’s surface, however, rescues the panel layer from elimination. To prepare for the additive 3D shaping process the surface area where metallization is to be added is textured. Following preparation, a narrow pattern of molten copper is deposited onto the surface, physically bridging the gap between features, as shown in Figure 2.
The AOS system is designed to accommodate a panel size as large as 24” x 30” (610 mm x 762 mm) and the company states that a single operator can control up to four AOS systems simultaneously, correcting defects, and managing the reshaping process without manual intervention. Additionally, remote image verification capability is offered that will enable the operator to monitor all copper defects and confirm the shaping process completion from a remote computer.
In addition to correcting opens in the circuit path, defect repair may include filling nicks and pinholes in the conductor path and rebuilding shapes impacted by localized over-etching. While conductor width and spacing can be as narrow as 30 µm, large pattern deposition of half-ounce copper is also possible, although limited to an area of 550 µm square. The process time required to restore copper conductors or correct other defects on the FR-4 laminate material’s surface is in the range of 30 locations per hour, depending on the conductor’s length, width, and specified copper thickness (half- or one-ounce).
Orbotech states that “this system is the world’s first one-stop solution that both removes excess copper and precisely restores patterns where copper is missing.” The process is said to enable top quality repair of the most advanced PCB designs, including any-layer HDI and complex multilayer circuits. A key objective of the manufacturer in developing this capability was to furnish the circuit board supplier the tools to ensure uncompromised end product quality and minimize delays in fabrication while virtually eliminating waste.
This column originally appeared in the February 2022 issue of PCB007 Magazine.
More Columns from Designer's Notebook
Designers Notebook: Basic PCB Planning Criteria—Establishing Design ConstraintsDesigners Notebook: Layer Stackup Planning for RF Circuit Boards
Designers Notebook: Addressing Future Challenges for Designers
Designers Notebook: Impact of Advanced Semiconductor Packaging on PCB Stackup
Designers Notebook: Implementing HDI and UHDI Circuit Board Technology
Designer's Notebook: Heterogeneous Integration and High-density SiP Technologies
Designers Notebook: PCB Design and IPC-CFX for Assembly Automation
Designer’s Notebook: What Designers Need to Know About Manufacturing, Part 2