-
- News
- Books
Featured Books
- design007 Magazine
Latest Issues
Current IssueProper Floor Planning
Floor planning decisions can make or break performance, manufacturability, and timelines. This month’s contributors weigh in with their best practices for proper floor planning and specific strategies to get it right.
Showing Some Constraint
A strong design constraint strategy carefully balances a wide range of electrical and manufacturing trade-offs. This month, we explore the key requirements, common challenges, and best practices behind building an effective constraint strategy.
All About That Route
Most designers favor manual routing, but today's interactive autorouters may be changing designers' minds by allowing users more direct control. In this issue, our expert contributors discuss a variety of manual and autorouting strategies.
- Articles
- Columns
- Links
- Media kit
||| MENU - design007 Magazine
Estimated reading time: 4 minutes
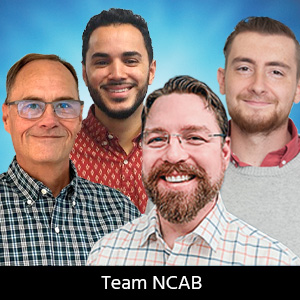
Fresh PCB Concepts: The Right Board for the Flex Job
We like to say we like the board that is best fit for the job, but what does the right board for your job specifically look like? In this column, I will review the benefits and design types of flexible PCBs.
What is a flex PCB? A flex board is defined as a bendable board with one or more conductive layers. There are different types of flex boards to fit any situation you may have. IPC defines them in five types, all are different constructions. To put it shortly these constructions are as follows: one layer of flex, double sided, multilayer flex, multilayer rigid-flex, and double or multilayer flex without electrically connected layers. Flex isn’t too old of a concept considering the history of PCBs. When first introduced these were pretty rare, however, recently the need for them has increased significantly due to the necessity to fit everything into a small package. These types of PCBs bring a number of benefits where rigid PCBs just won’t cut it.
With the right design a flex can offer cost savings on your assemblies, save space, and also cut the weight of your design. Flex are very lightweight PCBs and often very thin as well. Along with specialized FCCL material, this will allow a bend in our circuit. This bend allows us to build and assemble in an extra dimension. These are just some of the benefits that can be reaped from introducing a flex into your system. Flex also allows for a more cost-effective, robust, and reliable connector instead of using wires and cables, which can lead to less failures during and after assembly.
Recently a customer reached out for some help on a wearable sensor product. This design was originally done with a rigid board, however they were looking to move to a flex circuit. With the flex as opposed to the rigid board in this situation, they could inevitably increase the form fit and function. Since this was a wearable device; weight and fit make a world of difference. Lowering the weight and increasing the number of axis’, we can build in yields a better, lighter-weight and overall more natural fit than any rigid assembly could provide.
We have flex boards with stiffeners and rigid-flex boards, but ultimately how can we tell the difference between a one- or two-layer flex and a rigid-flex? There are a couple of key differences between a simple flex design and a rigid flex board. To begin, flex boards typically have a large flex area with certain areas stiffened. However rigid-flex designs contain circuitry and pads in the rigid areas and the rigid areas aren’t just used as stiffeners.
While we do see a lot of flex designs, rigid-flex is also a big contender and can also provide a number of benefits from both the flex and the rigid designs.
You might be thinking, “Why go for flex when rigid-flex provides advantages from both flex and rigid boards?” The reason is that rigid-flex not only provides benefits from both, but they also have their downfalls and using both rigid and flex can also produce some new challenges. Rigid-flex boards tend to be the thickness of a rigid board in the thickest areas so this doesn’t necessarily save on space. However, you do get the benefit of the flex region which allows you to have a dynamic flex wherever you need in the board. Rigid-flex also requires a bit more handling and care during the manufacturing process to make sure it comes out the way it was designed. While having a rigid-flex for the right situation can provide significant cost savings, one produced for the wrong system can just cause more headaches.
Here is a flex type that we don’t hear about too often: semi-flex. This is a type of flex that, for the most part, is not used often in the U.S.
A semi-flex PCB is a “rigid” board with a section routed out for flex-to-install applications. Typically a specialized FR-4 material is used and the factory will route down to the signal layers needed. This type of flex is very useful when it comes to static flex applications with only one or two layers in the flex area. While flex is in the name, these are not good for any situation where you’re going to bend these boards more than a couple times. However, semi-flex boards can be a cost-effective alternative to a fully flexible board.
Flex is a beneficial concept that has changed the circuit board industry and our world as we know it today. While not necessary for some projects or designs, other designs can flourish in our ever-growing, or ever-shrinking, world of technology. If you have questions on whether a flex board is an option for a specific project, I always recommend reaching out to you PCB supplier.
Nicholas Marks is a quote engineer for NCAB Group.
More Columns from Fresh PCB Concepts
Fresh PCB Concepts: Designing for Success at the Rigid-flex Transition AreaFresh PCB Concepts: More Than Compliance—A Human-centered Sustainability Approach
Fresh PCB Concepts: Assembly Challenges with Micro Components and Standard Solder Mask Practices
Fresh PCB Concepts: The Power of a Lunch & Learn for PCB Professionals
Fresh PCB Concepts: Key Considerations for Reliability, Performance, and Compliance in PCBs
Fresh PCB Concepts: Traceability in PCB Design
Fresh PCB Concepts: Tariffs and the Importance of a Diverse Supply Chain
Fresh PCB Concepts: PCB Stackup Strategies—Minimizing Crosstalk and EMI for Signal Integrity