Estimated reading time: 7 minutes
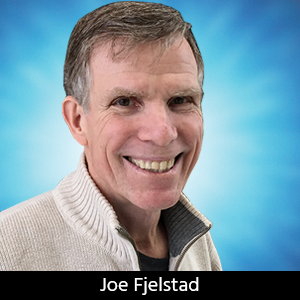
Flexible Thinking: The Fascinating History of Wearable Electronics
Wearable electronics have been capturing much attention in the press, both technical and business, over the past few years. Articles for consumption by the public, as well as technical research papers on the topic, have been increasing steadily in recent times. However, wearable electronics are far from new. Moreover, the term “wearable” is quite fungible and encompasses a broad spectrum of prospective embodiments. The convenience and utility of wearable electronics was, based on evidence, first conceived and conceptually reduced to practice over a century ago. Early in the history of electronics, the invention of the bi-telephone in-ear headphones were patented in 1891 by French electrical engineer Ernest Mercadier (Figure 1). Designed to be used by telephone operators, they even boasted perforated nipples to block out external sounds and support the apparatus.1 Figure 2 depicts what appear to be modern-day wireless earbuds conceived in the 1920's!
A quick search online for photos of 18-year-old H. Day from the UK will show his 1922 invention of a top hat radio which appears to be the first invention of its kind. It was followed up 27 years later by inventor and gadgeteer Victor Hoeflich’s introduction of the "Man from Mars, Radio Hat." The June 1949 issue of Radio-Electronics magazine had a two-page article describing the circuitry and construction of the radio.2 The circuit was built on a flexible liner (Figure 3) that fit inside the hat which was covered by a chassis shield and a perfectly smooth interior liner. Hoeflich hoped his innovative packaging of a radio in a pith helmet would be a runaway success but just five years later, the pocket transistor radio was introduced, and the rest is history.
From those humble and practical beginnings, the spectrum of wearable electronic products has expanded immeasurably with improvements in materials, manufacturing, and processing technologies in concert with engineering and scientific creativity. Enabling most of the advances has been flexible circuit technology with integrated electronic devices of every imaginable type, including everything from simple LEDs to sensors of every stripe, processors, and even flexible batteries.
What has also proven highly enabling to flexible electronic assemblies has been advances in silicon wafer thinning which makes normally brittle silicon integrated circuits truly flexible and bendable (Figure 4).
While thinning was developed for die stacking, it has proven an important benefit for making thin flexible electronic assemblies and thus opening doors to new applications. A collaboration between the Air Force Research Laboratory and American Semiconductor in 2017 produced a flexible silicon-on-polymer chip with more than 7,000 times the memory capability of any current flexible integrated circuit on the market at the time. The manufacturing took advantage of flexible hybrid electronics, integrating traditional manufacturing techniques with 3D electronic printing to create thin, flexible semiconductors that can augment efforts in wearable technology, asset monitoring, logistics and more.3
In recent years, some of the original terminology used exclusively for flexible has been altered and recast by technology marketers. What was once referred to as polymer thick film flexible circuit technology is being rebranded as “flex hybrid electronics” (FHE) and, with the newly introduced term fueled by significant funding from the U.S. government (especially the military) and in-kind contributions from players in industry, FHE is making new electronic design industry inroads and bringing new-found attention to time-honored flexible circuit technology, with wearable electronics often serving as a marquee application under the newly applied terms.
For decades, flexible circuits/printed electronics have been employed to solve many challenges and create new solutions to problems; of high interest has been areas related to health, especially remote monitoring of individual health. Flexible circuits have long been used in medical products such as for the interconnection of piezo ceramic transducer heads for ultrasonic imaging systems, but they have also been successfully used in catheter diagnostics, such as for electrophysiology studies to pinpoint and correct heart nerve pathways to mitigate or eliminate life threatening heart arrhythmias. The recent boost in awareness of flexible circuit technology, brought on by the strong marketing of FHE, is causing a rising tide in interest, which is “lifting all boats” as increasing numbers of product designers turn to flexible circuit technology to solve old problems and address new ones, especially in the field of wearable electronics.
Today, physical fitness buffs are routinely employing flexible circuit-enabled products that help them monitor their vital signs “on the run” and transmit results wirelessly to smart devices in real time on their wrists or in smart phones. Such thin flexible electronic devices are also used to help diabetics monitor their blood sugar in real time without having to stop and prick their fingers to measure glucose levels.
Flexible substrates are not the only kid on the block anymore. In the last decade, significant and growing attention has been given to stretchable circuits and stretchable electronics. Stretchable materials allow for circuit resilience not only in X and Y but also in the Z-axis allowing for a new dimension of design flexibility.
UC San Diego engineers have developed a wearable patch that could provide personalized cooling and heating at home, work, or on the go. The soft, stretchy patch cools or warms a user’s skin to a comfortable temperature and keeps it there as the ambient temperature changes. It is powered by a flexible, stretchable battery pack and can be embedded in clothing. Researchers say wearing it could help save energy on air conditioning and heating (Figure 5). Sheng Xu, UC San Diego professor of nanoengineering, developed the stretchable electronics for the system.4
“Woven” electronics are also now on the technological menu as e-textiles begin to capture interest for the manufacture of electronics-enabled clothing. While much of the early effort was for novel items of fashion, including programable LED lighting in apparel items (Figure 6), it was quickly recognized that the technology could be applied to the integration of electronic circuits for data processing in wearable applications. Again, interest has been shown in remote health monitoring for those who are in ill health and less mobile.
Standards for Circuits: A Necessary Glue
Over the years I have often been heard to refer to standards as a sort of “industrial strength glue” in that, collectively, industrial standards serve to help glue industries together and make them stronger. The IPC, through the dedication of its industry volunteer members, has been nurturing, producing, and publishing industry standards for electronic interconnection technologies for seven decades. The standards include materials and end-product requirements as well as guidelines for design and testing of printed circuits, both rigid and flexible, for decades. As evidence of their ongoing dedication to the industry and to keep pace with both ongoing and recent developments such as those described here, the IPC has taken point in the development of standards for the nascent arena of e-textiles just described. In October 2019, the IPC’s E-Textiles subcommittee completed its work on IPC-8921, “Requirements for Woven and Knitted Electronic Textiles (E-Textiles) Integrated with Conductive Fibers, Conductive Yarns and/or Wires.” It is the IPC’s first international standard for e-textiles, setting the groundwork for other e-textiles standards activities in progress.
Summary
This brief overview of wearable electronics has hopefully provided an appreciation of this branch of electronics technology that we might all agree is both very old and very new. The work of the IPC, as well as NextFlex and its partners and members—founded to promote flex hybrid electronics through its demonstration projects, facilities, and awareness programs—has done much to inspire new and current generations of designers to appreciate the immeasurable past and future benefits of flexible circuit technology. The future has just begun.
Note: I would like to express my gratitude to Shelly Stein for her invaluable assistance in researching, vetting and editing the content and images of this month’s column.
References
- patents.google.com/patent/US454138
- “Radio hat,” Wikipedia entry, wikipedia.org/wiki/Radio_hat
- (2017) AFRL, American Semiconductor create flexible system-on-chip for ‘internet-of-things,’ by M. Alia-Novobilski, Wright-Patterson Air Force Base, Ohio, USA, Air Force Research Laboratory.
- “Wearable Cooling and Heating Patch Could Serve as Personal Thermostat and Save Energy,” May 2019 press release, UC San Diego Jacobs School of Engineering.
- “An investigation of integrated woven electronic textiles (e-textiles) via design led processes” Vega, Prita (2015). This thesis was submitted for the award of Doctor of Philosophy and was awarded by Brunel
- University London, Brunel University Research Archive, College of Engineering, Design and Physical Sciences.
This column originally appeared in the April 2022 issue of Design007 Magazine.
Joe Fjelstad is founder and CEO of Verdant Electronics and an international authority and innovator in the field of electronic interconnection and packaging technologies with more than 185 patents issued or pending. Download your copy of Fjelstad’s book Flexible Circuit Technology, 4th Edition, and watch his in-depth workshop series, “Flexible Circuit Technology.”
More Columns from Flexible Thinking
Flexible Thinking: The Key to a Successful Flex Circuit Design TransferFlexible Thinking: Flexible Circuit Technology—Looking Back and Forward
Flexible Thinking: Mind-tapping into January
Flexible Thinking: Another PCB Design Paradigm Shift in the Works
Flexible Thinking: Rules of Thumb—A Word to the Wise
Flexible Thinking: Musings on High Density Interconnections
Flexible Thinking: Integrated Passive Devices—Design Solutions With Many Benefits
Flexible Thinking: Mechatronics in a Flex World