-
-
News
News Highlights
- Books
Featured Books
- pcb007 Magazine
Latest Issues
Current IssueThe Hole Truth: Via Integrity in an HDI World
From the drilled hole to registration across multiple sequential lamination cycles, to the quality of your copper plating, via reliability in an HDI world is becoming an ever-greater challenge. This month we look at “The Hole Truth,” from creating the “perfect” via to how you can assure via quality and reliability, the first time, every time.
In Pursuit of Perfection: Defect Reduction
For bare PCB board fabrication, defect reduction is a critical aspect of a company's bottom line profitability. In this issue, we examine how imaging, etching, and plating processes can provide information and insight into reducing defects and increasing yields.
Voices of the Industry
We take the pulse of the PCB industry by sharing insights from leading fabricators and suppliers in this month's issue. We've gathered their thoughts on the new U.S. administration, spending, the war in Ukraine, and their most pressing needs. It’s an eye-opening and enlightening look behind the curtain.
- Articles
- Columns
- Links
- Media kit
||| MENU - pcb007 Magazine
The Carbon Footprint of HDI: Direct Metallization vs. Electroless Copper
April 14, 2022 | Jordan Kologe and Leslie Kim, MacDermid Alpha Electronics SolutionsEstimated reading time: 2 minutes
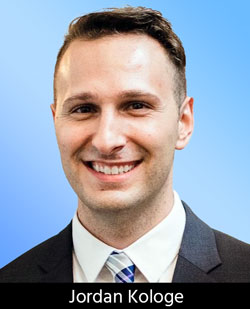
Introduction
As the electronics supply chain contends with the struggles of moving out of the pandemic and into a new normal, it is increasingly obvious that a new normal will be one with sustainability and resource conservation as the top priority. Over the past year, we have seen printed circuit board manufacturers encounter challenges associated with environmental regulations, water and power outages, and pressures from the supply chain to reduce environmental footprints.
From the perspective of a board fabricator, especially one that specializes in HDI, a highly resource-intensive step in the process of making a printed circuit board is the primary metallization step. All circuit boards that have multiple layers go through such a primary metallization, which is either electroless copper or direct metallization (DM). The main difference between a direct metallization process and the more traditional electroless copper plating process is that the former deposits a paint-like conductive coating through absorption onto the surface, while the latter deposits a copper coating from solution through chemical reduction. The DM coatings are most typically a carbon or graphite, and this kind of board manufacturing has been done reliably for nearly four decades.
Electroless copper processes have a larger carbon footprint than direct metallization for several reasons. Compared to direct metallization, electroless copper is more water and energy intensive, has a higher variety and amount of chemical ingredients, and has higher process variation. When looking at the comparison from the perspective of HDI, the impact of all of this becomes even more critical.
HDI—Why Direct Metallization?
In conventional PCB multilayer, the primary metallization step is utilized once all innerlayers of the board have been laminated and drilled and the board is nearing completion. The microvia structure is the central feature of HDI that allows for the manufacture of high-density circuit boards today. The microvia essentially replaces the singular through-hole that connects multiple layers and allows individual layers to be routed to their neighbors directly and separately from other layers. To achieve this feat of engineering, however, every single build-up operation that the board goes through requires an additional run through a primary metallization step.
It is for this reason that the electroless copper and direct metallization are under constant scrutiny from a reliability perspective. Yet, as we will discuss shortly, the sustainability question has not been widely examined. This is important since the volume of boards in the industry that use microvia designs is as high as it has ever been and will continue to grow to meet the needs of any electronic design that can economically benefit from increased circuit density.
Can we create an ever-increasing amount of printed circuit boards with HDI technologies such as mSAP while also meeting increasingly strict targets for carbon mitigation, while also meeting profitability expectations?
To read this entire article, which appeared in the February 2022 issue of PCB007 Magazine, click here.
Suggested Items
The Evolution of Picosecond Laser Drilling
06/19/2025 | Marcy LaRont, PCB007 MagazineIs it hard to imagine a single laser pulse reduced not only from nanoseconds to picoseconds in its pulse duration, but even to femtoseconds? Well, buckle up because it seems we are there. In this interview, Dr. Stefan Rung, technical director of laser machines at Schmoll Maschinen GmbH, traces the technology trajectory of the laser drill from the CO2 laser to cutting-edge picosecond and hybrid laser drilling systems, highlighting the benefits and limitations of each method, and demonstrating how laser innovations are shaping the future of PCB fabrication.
Day 2: More Cutting-edge Insights at the EIPC Summer Conference
06/18/2025 | Pete Starkey, I-Connect007The European Institute for the PCB Community (EIPC) summer conference took place this year in Edinburgh, Scotland, June 3-4. This is the third of three articles on the conference. The other two cover Day 1’s sessions and the opening keynote speech. Below is a recap of the second day’s sessions.
Day 1: Cutting Edge Insights at the EIPC Summer Conference
06/17/2025 | Pete Starkey, I-Connect007The European Institute for the PCB Community (EIPC) Summer Conference took place this year in Edinburgh, Scotland, June 3-4. This is the second of three articles on the conference. The other two cover the keynote speeches and Day 2 of the technical conference. Below is a recap of the first day’s sessions.
Preventing Surface Prep Defects and Ensuring Reliability
06/10/2025 | Marcy LaRont, PCB007 MagazineIn printed circuit board (PCB) fabrication, surface preparation is a critical process that ensures strong adhesion, reliable plating, and long-term product performance. Without proper surface treatment, manufacturers may encounter defects such as delamination, poor solder mask adhesion, and plating failures. This article examines key surface preparation techniques, common defects resulting from improper processes, and real-world case studies that illustrate best practices.
RF PCB Design Tips and Tricks
05/08/2025 | Cherie Litson, EPTAC MIT CID/CID+There are many great books, videos, and information online about designing PCBs for RF circuits. A few of my favorite RF sources are Hans Rosenberg, Stephen Chavez, and Rick Hartley, but there are many more. These PCB design engineers have a very good perspective on what it takes to take an RF design from schematic concept to PCB layout.