-
- News
- Books
Featured Books
- smt007 Magazine
Latest Issues
Current IssueSupply Chain Strategies
A successful brand is built on strong customer relationships—anchored by a well-orchestrated supply chain at its core. This month, we look at how managing your supply chain directly influences customer perception.
What's Your Sweet Spot?
Are you in a niche that’s growing or shrinking? Is it time to reassess and refocus? We spotlight companies thriving by redefining or reinforcing their niche. What are their insights?
Moving Forward With Confidence
In this issue, we focus on sales and quoting, workforce training, new IPC leadership in the U.S. and Canada, the effects of tariffs, CFX standards, and much more—all designed to provide perspective as you move through the cloud bank of today's shifting economic market.
- Articles
- Columns
- Links
- Media kit
||| MENU - smt007 Magazine
Estimated reading time: 4 minutes
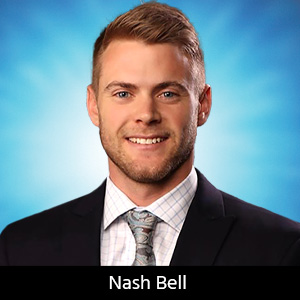
Knocking Down the Bone Pile: Reworking of SMT Connectors with Center Ground Connection
Connectors such as those pictured in Figure 1 are challenging to rework as they generally have a high density, and tight spacing of connector pins as well as a ground connection running through the center of the body of the part. The generic term for these types of connectors is “surface mount center ground connector.” These surface mount connectors are designed for parallel board-to-board, flex-to-board, and cable-to-board configurations, and are generally compatible with both infrared and forced air convection rework heating methods. Specifically, a popular type of this connector configuration is a mezzanine connector which connects two parallel printed circuit boards in a stacking configuration.
The rework of a component such as this requires that the assembly be handled by keeping in mind ESD 2020 guidelines for static control, including but not limited to operator grounding, proper packaging, and proper keep-out zones with respect to insulators that can generate and/or hold an electrostatic charge.
When components such as this (Figure 2) are connected to a ground plane, it is imperative that the right amount of heat be imparted to the component during the removal process, especially when connected to a large ground plane. After properly supporting the assembly in the rework system, apply paste flux with your preferred chemistry to the component leads. The next step is making sure that the neighboring components are shielded to make sure all the components which need to be are thermally shielded. Components to be particularly watchful of include (but are not limited to) plastic-bodied connectors, ceramic capacitors, LEDs, glass bodied fuses, and others which are near the rework area. Make sure to examine the side opposite of the component to protect neighboring components from thermal damage prior to using heat to remove the component.
Prior to removing the component, it is always good practice to develop a profile board. In a profile board, thermocouples are embedded in key locations at and around the component location (on a process development board) to measure board and soldering temperatures at various locations. Typical locations to place these thermocouples are at the ground plane pad and at least two locations opposite one another on the connector. More thermocouples may be added at locations near heat-sensitive devices.
The rework removal profile can be more aggressive than typical reflow norms since in most cases, the component will be scrapped. Make sure the bottom side of the board is between125–150°C through heating of a bottom heater. Both IR and hot air sources can be used as a rework heat source. When profiling, make sure that the solder has turned into the liquidus phase by carefully observing the component either on the video feed provided by the rework station or by carefully peering at the solder/board interface using a flashlight. Once you can observe that the solder has obtained the liquidus state, activate the removal cycle and pick up the connector.
As in other area array or more complex component rework processes, after the assembly comes down to room temperature it is time to prep the site by wicking solder from the pads and cleaning the location. Finally, the pads should be inspected for damage.
For these component body styles it is best to use a miniature stencil or a programmable solder paste dispenser to affix the replacement connector to the PCB. The adhesive-backed stencil method is the least time-consuming method for selectively re-applying solder paste to the pads. The center ground pattern may need to be “window paned” to prevent too much solder from “lifting up” the connector leads. After peeling off the release liner from the stencil, align the stencil apertures, starting at one of the corners. Make the final fine alignment adjustments taking advantage of the repositionable adhesive which will keep also serve to affix the stencil into place once aligned. Using a small squeegee, roll solder paste through the apertures and then slowly peel up the stencil making sure it is perpendicular to the board surface. Examine the solder “bricks” formed on the PCB to make sure the solder paste has been applied to all locations consistently.
Another approach for stenciling is to use a “mini” stainless stencil that mimics the original stencil design at the rework location. This technique takes a great deal more skill to get right and not “smear” the solder paste. A programmable dispenser, while taking some time to set up and program, will also provide for a consistent solder paste volume at each of the pads. After the solder paste is deposited, place the PCB onto the rework station making sure the PCB is properly supported. Recall the proper reflow profile in the rework station and begin the reflow cycle.
After reflow, a few more steps need to be taken to compete the rework process. After the board has cooled and the assembly has been removed from the rework machine, the rework area needs to be cleaned and then visually inspected per the IPC-A-610 standards. Since the ground connection is a non-inspectable area of the connector, this rework needs to be placed into an X-ray machine in order to confirm the solder connection of the component to the PCB. Final inspection also includes the “fit up” with a header that will plug into the receptable on the board to make sure that the connector will function properly and has not been damaged in the rework process.
While the rework of high density SMT connectors with ground planes is challenging, the right process with the right controls in place and completed with properly trained personal will provide for a high yield.
This column originally appeared in the May 2022 issue of SMT007 Magazine.
More Columns from Knocking Down the Bone Pile
Knocking Down the Bone Pile: Addressing End-of-life Component Solderability Issues, Part 4Knocking Down the Bone Pile: Tin Whisker Mitigation in Aerospace Applications, Part 3
Knocking Down the Bone Pile: Gold Mitigation for Class 2 Electronics
Knocking Down the Bone Pile: Basics of Component Lead Tinning
Knocking Down the Bone Pile: Package on Package Rework—Skill Required
Knocking Down the Bone Pile: 2023’s Top Challenges in BGA Rework
Knocking Down the Bone Pile: Eliminating Solder Balls in Hand Soldering
Knocking Down the Bone Pile: Opening a Trace on the Surface of a PCB