-
- News
- Books
Featured Books
- pcb007 Magazine
Latest Issues
Current IssueSales: From Pitch to PO
From the first cold call to finally receiving that first purchase order, the July PCB007 Magazine breaks down some critical parts of the sales stack. To up your sales game, read on!
The Hole Truth: Via Integrity in an HDI World
From the drilled hole to registration across multiple sequential lamination cycles, to the quality of your copper plating, via reliability in an HDI world is becoming an ever-greater challenge. This month we look at “The Hole Truth,” from creating the “perfect” via to how you can assure via quality and reliability, the first time, every time.
In Pursuit of Perfection: Defect Reduction
For bare PCB board fabrication, defect reduction is a critical aspect of a company's bottom line profitability. In this issue, we examine how imaging, etching, and plating processes can provide information and insight into reducing defects and increasing yields.
- Articles
- Columns
- Links
- Media kit
||| MENU - pcb007 Magazine
Estimated reading time: 4 minutes
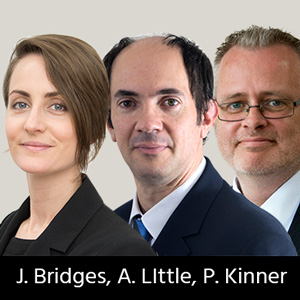
Sensible Design: Why Some Conformal Coatings Fail in Service
In this month’s column, I will examine why coatings sometimes fail in service and the steps you can take to avoid failure in the first place. At Electrolube, we take great care in our research, product formulation, and developing the appropriate processing and application techniques for our products because we know that, on occasion, conformal coatings can fail and it is our business to understand why.
Our investigations are thorough, and to list our findings here in any detail is somewhat beyond the scope of this column. However, some of the more common root causes of failure pop up frequently, and I’d like to run through these issues, offer some tips, and bust the odd myth. As in our previous columns, they will be presented in a question-and-answer format.
Are some PCBs impossible to coat due to their design?
Nothing is impossible if you have enough time and money, but design is important in determining suitable application methodology and, therefore, the cycle times and the costs involved. Some simple things, like trying to keep connectors or other no-coat areas on the same edge of the assembly, can make a huge difference to the ease of coating an assembly, the cost of coating that assembly and, of course, the overall reliability of that assembly.
What are the main reasons for coating failure?
Coating failure can happen for any number of reasons, some common and some not so common. Here are five fundamental reasons which are generally the result of poor product selection and/or application, or some underlying problem arising from insufficient surface preparation or some chemical activity going on beneath the coating that is entirely unrelated to the coating chemistry:
- The formulation of the coating is insufficient for the job. Choosing an appropriate material selection at the outset can help avoid problems such as condensation occurring, and the coating fails to maintain an adequate level of insulation when the PCB is subjected to a condensing environment. There are some coatings that are much more resistant to these sorts of conditions; failure could have been prevented.
- Application is crucial to coating success. If the conformal coating has not cured properly, it will not have a chance to develop its protective properties to the full. By getting the application right, you can resolve many issues in one hit.
- Inadequate coverage or insufficient thickness. Sharp edge coverage can be difficult to achieve with many coatings and it can be hard to ensure sufficient thickness in these areas to maintain protection. A combination of material selection and application technique/workmanship will remedy these sorts of issues.
- Unexpected interaction with other process materials used to prepare/build the PCB, such as flux residues, are particularly illustrative of this type of problem. In a “no-clean” process, for example, these can inhibit the cure of some types of coating or lead to a loss of insulation of the system, greater than either material in isolation.
- Something else is going on that isn’t directly related to the coating. Unless there has been meticulous attention to preparation or pre-coat cleaning regimes, potentially corrosive residues bridging the PCB’s conducting tracks can, over time, cause failures. While the coating may delay failure for many years, at some point failure will inevitably happen.
Is the application method important to the reliability of coatings?
Application method is probably the number one determinant of success. Often a poor material, well applied, can be just as good (or sometimes better) than a material with great properties that is applied badly. Coating is about getting sufficient coverage of the sharp edges and metal surfaces without applying the material too thickly elsewhere. Some materials “apply better” than others and make this process more straightforward, but in the end, the performance of liquid applied coatings will always be determined by how well they were applied.
Would a thicker coating be less likely to fail?
To be honest, it depends on the coating chemistry. Thicker can be better up to a point but at some stage the coating material will be too thick and will either crack itself, or even cause cracking of the coated components themselves, for example, during thermal shock or thermal cycling. And depending on the type of coating material used, solvent entrapment (i.e., the solvent not having enough time to evaporate from the coating film before it hardens) can become an issue.
On top of this, by adding unnecessary amounts of coating material you are in effect wasting it, adding to costs and, importantly for some applications, adding weight. Compromised thermal management issues can also arise as it may prove difficult to dissipate heat away from thickly coated components.
It is good to remember that above a certain thickness, which does vary according to the material being applied, any increase is likely to deliver diminishing returns. Get the advice of a reputable supplier; they have laboured hard to establish optimum coating thicknesses for their products in all kinds of operating environments. There’s a lot to consider for a successful conformal coating process. Getting it wrong could compromise the reliability of an electronic assembly, shorten its life expectancy, or even prove critical. First and foremost, seek some expert advice as there are new coating materials, such as our new bio-based UVCLX coating with 75% bio-organic content from renewable sources, which might solve your requirements more sufficiently. I hope my column has been useful and of course, we are always happy to help and advise.
This column originally appeared in the May 2022 issue of Design007 Magazine.
Download your copy of?Electrolube's?book,?The Printed Circuit Assembler's Guide to… Conformal Coatings for Harsh Environments,?and watch the micro webinar series “Coatings Uncoated!”?
More Columns from Sensible Design
Sensible Design: Automotive Conformal Coating ApplicationsSensible Design: Green Coats Are In
Sensible Design: Encapsulation Resins—PU vs. Epoxy
Sensible Design: Avoiding Conformal Coating Pitfalls
Sensible Design: Comparing Traditional and Bio-based Resins
Sensible Design: All Resins Are Not Created Equal
Sensible Design: Can Solvent-free UV-cure Coatings Increase Stability and Throughput?
Sensible Design: Optimize Your Thermal Management