-
- News
- Books
Featured Books
- pcb007 Magazine
Latest Issues
Current IssueSales: From Pitch to PO
From the first cold call to finally receiving that first purchase order, the July PCB007 Magazine breaks down some critical parts of the sales stack. To up your sales game, read on!
The Hole Truth: Via Integrity in an HDI World
From the drilled hole to registration across multiple sequential lamination cycles, to the quality of your copper plating, via reliability in an HDI world is becoming an ever-greater challenge. This month we look at “The Hole Truth,” from creating the “perfect” via to how you can assure via quality and reliability, the first time, every time.
In Pursuit of Perfection: Defect Reduction
For bare PCB board fabrication, defect reduction is a critical aspect of a company's bottom line profitability. In this issue, we examine how imaging, etching, and plating processes can provide information and insight into reducing defects and increasing yields.
- Articles
- Columns
- Links
- Media kit
||| MENU - pcb007 Magazine
Estimated reading time: 5 minutes
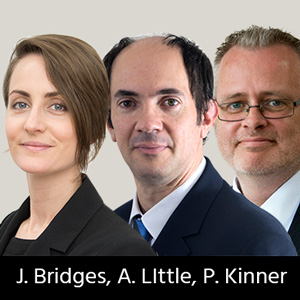
Sensible Design: Green Coats Are In
It goes without saying that bio-based coatings have significantly less impact on the environment and are better able to address the ethical and sustainability requirements of manufacturers and end users than conventional solvent-based coatings. However, the most surprising benefits observed during the development of many new bio-based conformal coatings have been the significant improvements to performance and reliability.
The bio-based material we’ve developed, for example, has shown improved condensation resistance, thermal stability, flexibility, and adhesion compared to many petrochemical-derived materials. This bio-coating has distinguished itself as a top performer with the environmental credentials to match, making it a win-win solution. Making the switch to bio-coatings can also help manufacturers “future proof” their processes. For example, with all the new climate-change targets currently being suggested, including some environmentally conscious measures requiring manufacturers to make drastic changes in just a couple years, those who have already transitioned to bio-based proportional alternatives will have a significant leg up on the competition.
Let’s examine why these conformal coatings, based on organic, renewable ingredients, can help manufacturers stay one step ahead without having to compromise performance. Here are two questions and answers to consider.
Do you see the future of coatings as “greener,” or will there always be a demand for the more traditional solvent-based coatings?
Solvent-based conformal coatings are the most used conformal coatings in the electronics market, and there are many reasons why: They are easy to use, cost-effective, and there is a wide selection available. Whilst solvent-based conformal coatings are incredibly popular and will surely stay with us for quite some time, we are currently seeing a shift to a more careful attitude regarding our finite resources and a desire for more environmentally friendly and sustainable conformal coating products.
Specifically with younger generations on the electronics consumer side, but also in the workplace with product designers, electronic design engineers, chemical engineers, marketers, and others, there is a growing interest in sustainability and environmentally friendly solutions, as well as a willingness to create products that really make a difference. This attitude shift has been filtering through the supply chain, creating pressure to meet this demand for a greener approach to manufacturing and, ultimately, a greener future overall.
Alongside this environmentally conscious perspective, a demand for protective materials that will allow electronics to withstand harsher environments has also materialized in the industry. Such requirements are becoming more stringent every day, and the pressure is on manufacturers to meet this evolving need. As it turns out, our research has shown that natural materials—including materials from food waste, for instance—can provide similar or better properties and protection than conventional options. With such promising characteristics, it seems only logical to dig into these renewables for coating product development. Nature is providing us with better solutions that are as sustainable as they are efficient, so there appears to be a definite future for “greener” conformal coatings.
What is the benefit of a secondary chemical cure in UV curing conformal coatings?
When we look at the traditional UV-cure conformal coatings, we find materials that have a UV primary cure and a secondary moisture cure. This means that wherever the correct UV light wavelength reaches the coating, it will cure the material within a matter of seconds. However, the issues lie within the areas that are not reached by the UV light. Between high components or under component parts, we still want the conformal coating to cure to ensure even protection. For those areas, we will need the secondary cure.
Many common UV-cure coatings use atmospheric moisture for their secondary cure, which can release by-products that produce a strong odor. In applications where the PCB is placed in an airtight enclosure, the available moisture can be limited, potentially resulting in an insufficient cure and limited protection of the electronics. Therefore, it is important to leave the coated PCB until the secondary cure has fully taken place. Depending on the UV coating, the secondary cure can take days, weeks, and, in some cases, even months.
However, with a chemical cure as the secondary cure, the chemical cure will happen with the conformal coating. This is because, rather than relying on a single component material, this process uses a material that consists of two parts, part “A” and part “B,” that will react when mixed to complete the cure. So, after the UV primary cure has taken place, the material will go into the secondary cure phase without the need for any environmental input.
The secondary cure will also happen much faster, depending on the type of coating, the coating thickness, and the temperature; normally, a secondary cure can be completed in 16 to 24 hours. The coated PCB can be handled and, in most cases, even assembled into an enclosure straight away. As there is no need for moisture, the enclosure can be closed without the worry that some areas have failed to cure.
This is a huge advantage for customers, as it reduces or even diminishes the need for excessive buffer storage between production and assembly. This, together with a faster production process, means huge cost savings in production. With general manufacturing costs going through the roof, saving costs wherever possible has become a priority for many.
Regardless of the cost-saving benefits, real progress means looking at how we can ensure that our products are environmentally friendly; the degree of performance improvement achieved with these innovative new coatings is only a small part of what makes them so exciting. Whilst the development focus for such materials has been very much geared toward meeting the demanding requirements of automotive and aerospace applications, the high-performance levels of these materials make them a great choice for any application. These products really come into their own whenever thermal shock cycling and condensation resistance are at play, though these are by no means the only failure mechanisms.
As we all continue thinking about how we can revolutionize our processes to reach that “greener” future, consider how bio-coatings might benefit both your business and the environment—these materials may just be the solution you’ve been looking for.
Download your free copy of Electrolube's book, The Printed Circuit Assembler's Guide to… Conformal Coatings for Harsh Environments, and watch the micro webinar series “Coatings Uncoated!”
This column originally appeared in the December 2022 issue of Design007 Magazine.
More Columns from Sensible Design
Sensible Design: Automotive Conformal Coating ApplicationsSensible Design: Encapsulation Resins—PU vs. Epoxy
Sensible Design: Avoiding Conformal Coating Pitfalls
Sensible Design: Comparing Traditional and Bio-based Resins
Sensible Design: All Resins Are Not Created Equal
Sensible Design: Can Solvent-free UV-cure Coatings Increase Stability and Throughput?
Sensible Design: Optimize Your Thermal Management
Sensible Design: Why Some Conformal Coatings Fail in Service