-
- News
- Books
Featured Books
- pcb007 Magazine
Latest Issues
Current IssueSales: From Pitch to PO
From the first cold call to finally receiving that first purchase order, the July PCB007 Magazine breaks down some critical parts of the sales stack. To up your sales game, read on!
The Hole Truth: Via Integrity in an HDI World
From the drilled hole to registration across multiple sequential lamination cycles, to the quality of your copper plating, via reliability in an HDI world is becoming an ever-greater challenge. This month we look at “The Hole Truth,” from creating the “perfect” via to how you can assure via quality and reliability, the first time, every time.
In Pursuit of Perfection: Defect Reduction
For bare PCB board fabrication, defect reduction is a critical aspect of a company's bottom line profitability. In this issue, we examine how imaging, etching, and plating processes can provide information and insight into reducing defects and increasing yields.
- Articles
- Columns
- Links
- Media kit
||| MENU - pcb007 Magazine
Estimated reading time: 5 minutes
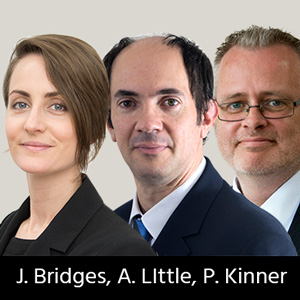
Sensible Design: Avoiding Conformal Coating Pitfalls
Electronic circuits are abundant in modern life and will continue to surge in growth as former manual processes increasingly become automated. The rapid advances we see in technology are driving electronic circuitry to perform faster in harsher environments, in the smallest form, and with the lightest weight. Circuitry failure is not only inconvenient and expensive but as electronic infrastructures become more interconnected, individual failures will put an entire system at risk, which could ultimately put lives in danger for critical applications. It is so important to factor in careful consideration for conformal coatings. In this month’s column, I will cover some important areas to help you steer clear of coating disasters.
Get It Right at the Design Stage
The earlier the coating is factored into the design process, the more likely there will be a successful coating outcome. It saves time and expense in rectifying any problems that may occur later. Important considerations include specifying:
- “Must-coat” areas of the PCB
- “Must-not-coat” areas
- Transition areas, sometimes referred to as “can-coat” or “don’t care” areas
Check how close together the components are and whether there is a sufficient gap between the components. If the gap is insufficient, it can lead to the coating bridging the gap rather than correctly conforming to the board, which can also cause the coating to become too thick and crack or it can leave pockets under the coating where solvent can gather and cause corrosion. Tall components can bring their own challenges by creating shadowed or hard to reach areas. It is therefore sensible to avoid placing tall components in direct proximity to “must-not-coat” areas of the PCB. Larger spacing between such areas can help to achieve a cleaner coating picture. If a larger gap is not maintained, coating may splatter onto “must-not-coat” areas.
Preparation the Key to Success
To truly minimize the risk of defects and failure, cleaning prior to coating needs to be a top priority, otherwise potential residues on the substrate will have a critical impact on coating performance. Without cleaning, residues may interfere with curing, leading to poor adhesion of the coating to the substrate and trapping conductive/ionic materials under the coating. Without a pre-coat cleaning regimen, corrosive residues bridging the PCB’s conducting tracks can cause failures over time. It is of key importance that the PCB is fully dry following the cleaning process to ensure that any residual solvents and moisture are removed prior to the coating and curing procedures. Humidity below the coating can lead to corrosion. Residual solvent on the board can cause bubbles or cracking during the curing process.
Apply the Coating Well
Applying a coating correctly is probably the biggest factor for coating success. You may have purchased the best coating known to the industry, but if it isn’t applied well, it simply will not deliver sufficient protection. Attainment of the “right” coating application is just as important as selecting the right material.
Top Tips
- Check the coating thickness that’s required. Do not apply the coating in a thicker layer than is recommended. If the coating is applied too thickly, solvent entrapment can occur, causing a weakness for external influences to attack the board.
- Check the level of coverage. Gaps in the coating coverage can leave areas of components exposed to humidity or corrosive gasses, providing an entry point to metal surfaces of components.
- Consider the adhesion of the coating to the board and its components. Contamination or processing residues on the board can lead to an insufficient wetting of the coating. Even where the coating is showing a good level of adhesion, the contaminant may not show the same good adhesion to the substrate, potentially leading to delamination.
Remember: The typically successful application method would ensure that each board receives a suitable coating coverage on all required metal surfaces, at a sufficient thickness to provide protection against the environment. These requirements will change with different board designs and environments and will need to be tested and verified ahead of production.
Coating Selection
There are many coating options to choose from, such as an acrylic, a polyurethane, a silicone, a UV cure, or a two-part system. The design of the board may or may not affect the choice of coating material, but it will definitely influence the methods that are suitable for application of the coating. Certain materials, such as moisture-curing or UV-curable materials, are difficult to use in a dip process due to the material curing prematurely, so it could be said that the choice of coating is indirectly related to the board design. Factors such as operating temperature range, temperature excursions (such as thermal shock and thermal cycling), corrosion, condensation, and resistance to chemicals, solvents, and water are all key in determining the successful outcome for a coating. Working with an experienced provider can help you navigate which coating is best for your application and advice on methods.
Consider the Two Primary Failure Mechanisms
Aside from insufficient planning at the design stage, a poorly applied coating, or ignoring pre-coat cleaning, two of the most common reasons for coating failure include corrosion and loss of insulation, which leads to short circuits. Corrosion is a complex process that takes place on an exposed metal surface, usually in the presence of water and ionic contaminants. Cleaning prior to conformal coating will go a long way toward removing these two pre-requisite conditions for corrosion as coatings help prevent the formation of electrolytic solutions by acting as moisture barriers. However, small voids in the coating that expose a PCB’s metal surfaces can accelerate corrosion under the right environment. The challenge for a conformal coating is to achieve good coverage and adhesion to the complex, three-dimensional topography of a PCB. Poorly performing coatings also risk loss of insulation at the PCB surfaces when water condenses in combination with ionic impurities to form conductive pathways between PCB tracks. Without doubt, condensation can severely test the insulation resistance of a coating.
Avoiding coating pitfalls is a fine balance of material selection, understanding the engineering requirements for coverage, and thickness, as well as choosing a suitable application method. Understanding the intricacies of conformal coatings will pay off in determining a successful coating outcome. There’s a great deal more to discuss and over the following months I hope to provide more useful tips and advice that will help you accomplish reliable circuit protection.
This column originally appeared in the October 2022 issue of Design007 Magazine.
Download your free copy of Electrolube's book, The Printed Circuit Assembler's Guide to… Conformal Coatings for Harsh Environments, and watch the micro webinar series “Coatings Uncoated!”
More Columns from Sensible Design
Sensible Design: Automotive Conformal Coating ApplicationsSensible Design: Green Coats Are In
Sensible Design: Encapsulation Resins—PU vs. Epoxy
Sensible Design: Comparing Traditional and Bio-based Resins
Sensible Design: All Resins Are Not Created Equal
Sensible Design: Can Solvent-free UV-cure Coatings Increase Stability and Throughput?
Sensible Design: Optimize Your Thermal Management
Sensible Design: Why Some Conformal Coatings Fail in Service