-
- News
- Books
Featured Books
- pcb007 Magazine
Latest Issues
Current IssueSales: From Pitch to PO
From the first cold call to finally receiving that first purchase order, the July PCB007 Magazine breaks down some critical parts of the sales stack. To up your sales game, read on!
The Hole Truth: Via Integrity in an HDI World
From the drilled hole to registration across multiple sequential lamination cycles, to the quality of your copper plating, via reliability in an HDI world is becoming an ever-greater challenge. This month we look at “The Hole Truth,” from creating the “perfect” via to how you can assure via quality and reliability, the first time, every time.
In Pursuit of Perfection: Defect Reduction
For bare PCB board fabrication, defect reduction is a critical aspect of a company's bottom line profitability. In this issue, we examine how imaging, etching, and plating processes can provide information and insight into reducing defects and increasing yields.
- Articles
- Columns
- Links
- Media kit
||| MENU - pcb007 Magazine
Estimated reading time: 6 minutes
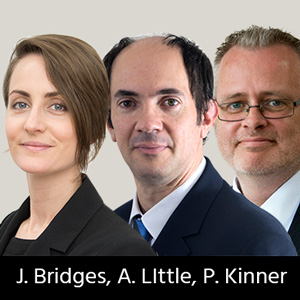
Sensible Design: Optimize Your Thermal Management
In this column, I’ll be looking at how to help you improve reliability through thermal management. Poor reliability arising from thermally induced circuit failures might prove detrimental to brand reputation, but if the application served a critical role, the outcome would be unthinkable. Such applications might include:
- A safety-critical device upon which the safety of personnel working in a hazardous environment might depend
- One that simply would not function without proper thermal management procedures in place
- A device that has a defined working temperature range when in use, or a piece of equipment designed to work in harsh or extreme conditions, which must work reliably, regardless of those conditions
There are a variety of thermal management materials to choose from, and they serve different purposes depending upon the physical constraints of the application, component layout and assembly geometry, the environment in which the assembly will be placed, the severity of duty, and so on. Then there are more specific questions to ask, such as what’s essential for efficient heat transfer, or should I use a bonding or non-bonding material? So without further ado, lets address this in our five-point format.
1. What key issues must be considered when trying to achieve efficient heat transfer?
Again, think variability of environmental conditions. Just because the heat transfer is efficient under standard ambient conditions, doesn’t mean that it will remain stable over the lifetime of the product. Accelerated testing might be able to reveal related design issues; however, in-application testing is more likely to provide definitive information about the long term performance of heat transfer materials.
The application method and applied thickness of heat transfer compounds will depend on the type of interface or gap filling material used and both are crucial to achieving efficient heat transfer. These compounds provide a medium for improving the conditions under which heat transfer takes place and thereby maximise efficiency. Compounds should not be applied in excess amounts in the belief that they will achieve the thermal conductivity of a solid metal heat sink, and remember, high thermal conductivity doesn’t necessarily mean high heat transfer. Measuring thermal resistance at the interface is the most effective way to ensure the thermal compound is improving the efficiency of heat transfer and these results can differ depending on the thickness and quality of application.
Throughout our discussions, you will see both points come up time and again. They are crucial to ensuring effective and efficient heat transfer with reliable performance from each device as well as over the lifetime of the product.
2. Bonding or non-bonding?
There are many different types of thermally conductive materials, and choosing between them will be dictated by production requirements and application design, as well as critical performance factors that must be achieved. Due to the variety of products available, this question is often one of the first to arise and can sometimes be answered very simply. For example, choosing between a bonding or non-bonding material may depend on whether the heat sink needs to be held in place by the interface material, in which case a bonding compound is the better choice. There are also many other factors that can affect this choice and it is often better to review the requirements as a whole first. This allows a holistic view of the requirements from application through to performance in use. Usually by taking this approach, the decision of bonding or non-bonding often becomes clear.
3. Increasing efficiency across a wide temperature range
Thermal changes are common within heat dissipation applications because most devices are switched on and off, or have varying power requirements in use. In addition, environmental temperature changes can lead to extremes within the device. Automotive applications are a good example, as these must also operate after being powered down in conditions well above and below what we would consider a standard ambient temperature.
It is therefore critical that the chosen thermal dissipation media operates within the temperature limits defined for the device, while maintaining performance during changeable conditions. A typical problem is “pump-out” whereby the stresses exerted by the minute changes in dimensions of the interface substrates can cause a non-curing interface material to move over time. The ability of a thermal interface material (TIM) to resist these stresses will improve the performance of the device over its lifetime and will be dependent upon the interfacial spacing, as well as the type and amount of TIM applied.
4. Know your dimensions
Understanding the dimensions of your application is critical to the selection of appropriate thermal management materials. A thermal interface is the space between a component and its heat sink, and the thermally conductive media used in this space are referred to as thermal interface materials. This space is usually very small, i.e., on the micron scale. A gap filling application, on the other hand, is more to do with the distance between a component and the metal housing that encloses an electronics assembly and is usually measured in millimetres. For example, a thermally conductive material is placed to help minimise the chances of hot spots within the unit itself while the casing is used as the heat sink.
The difference between a few microns and a few millimetres could be critical to the performance of the thermal medium chosen. For example, if you place a TIM in a gap filling application, it is likely to be unstable in a thicker layer; with vibration or following a period of temperature cycling, it could easily be displaced. And if a gap filling material is used in a thermal interface application, it will be very difficult to achieve a thin, even film, creating a higher thermal resistance at the interface and consequently reduced heat transfer efficiency.
5. Tips for material selection
As discussed, for an interface material, the bond line thickness needs to be as thin as possible to minimise thermal resistance. For a gap filling material, the dimensions of the gap need to be considered and environmental factors evaluated to decide whether a curing or non-curing product would be best in terms of the stability of the material under the application conditions as well as considering the possible effect on physical stresses within the unit.
In all cases, the operating temperature range and environmental conditions of the application need to be reviewed. If very high temperatures are expected, a silicone may be required, and if the assembly is subject to rework, then a non-bonding, non-curing product should be used. If thermal protection is localised to one component, a curing product is the better choice as it will avoid migration of the material to neighbouring components. However, if that component or area is sensitive to changes in coefficient of expansion, it must be ensured that the cured product used does not cause any negative impact over the application temperature range. With consideration of the application requirements in unison, the optimum thermal management product can be defined, achieving increased performance and reliability of the design.
There’s a lot to consider for successful thermal management. Getting it wrong could compromise the reliability of an electronic assembly and shorten its life expectancy or even prove critical. It’s strongly advised to do your calculations; consider the application requirements as well as operational and environmental conditions, and test, test, test. Experimenting with the product in the actual design is the only way to truly understand the performance that can be achieved and conclude with the correct selection of thermal management products. First and foremost, seek some expert advice, discuss your application, and identify the most suitable products for review.
This column originally appeared in the June 2022 issue of Design007 Magazine.
Download your free copy of Electrolube's book, The Printed Circuit Assembler's Guide to… Conformal Coatings for Harsh Environments, and watch the micro webinar series “Coatings Uncoated!”
More Columns from Sensible Design
Sensible Design: Automotive Conformal Coating ApplicationsSensible Design: Green Coats Are In
Sensible Design: Encapsulation Resins—PU vs. Epoxy
Sensible Design: Avoiding Conformal Coating Pitfalls
Sensible Design: Comparing Traditional and Bio-based Resins
Sensible Design: All Resins Are Not Created Equal
Sensible Design: Can Solvent-free UV-cure Coatings Increase Stability and Throughput?
Sensible Design: Why Some Conformal Coatings Fail in Service