-
-
News
News Highlights
- Books
Featured Books
- pcb007 Magazine
Latest Issues
Current IssueThe Hole Truth: Via Integrity in an HDI World
From the drilled hole to registration across multiple sequential lamination cycles, to the quality of your copper plating, via reliability in an HDI world is becoming an ever-greater challenge. This month we look at “The Hole Truth,” from creating the “perfect” via to how you can assure via quality and reliability, the first time, every time.
In Pursuit of Perfection: Defect Reduction
For bare PCB board fabrication, defect reduction is a critical aspect of a company's bottom line profitability. In this issue, we examine how imaging, etching, and plating processes can provide information and insight into reducing defects and increasing yields.
Voices of the Industry
We take the pulse of the PCB industry by sharing insights from leading fabricators and suppliers in this month's issue. We've gathered their thoughts on the new U.S. administration, spending, the war in Ukraine, and their most pressing needs. It’s an eye-opening and enlightening look behind the curtain.
- Articles
- Columns
- Links
- Media kit
||| MENU - pcb007 Magazine
Technica Heats Up ROI Discussion
May 17, 2022 | I-Connect007 Editorial TeamEstimated reading time: 3 minutes
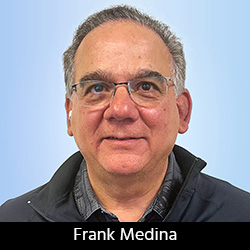
The I-Connect007 Editorial Team speaks with Technica’s Frank Medina, Ed Carrigan, and Jason Perry about trending hotspots that provide the PCB fabricator a high return on investment (ROI). A theme that carries throughout the conversation is that traditional methods for calculating ROI are being replaced by models that include more qualitative factors.
Nolan Johnson: Frank and Jason, where do you see the ROI hotspots in manufacturing right now?
Frank Medina: One is solder mask equipment; another area is automation and material handling.
Jason Perry: I think there are several more areas. A lot of effort has been put into the inner layer and outer layer departments. People are moving toward upgrading the back end of the process. We’re seeing more demand for solder mask improvement and technology, direct write type of technology, and inkjet applications.
Reducing process steps, improving throughput, and improving time to market—getting product through the shop faster always equals higher dollars and lower costs. There’s a drive toward that on the back end, including automation to reduce labor costs as those costs continue to increase. We’re seeing demand to automate repetitive tasks the operators would normally be doing. The goal is to repurpose operators to more important areas, instead of just feeding lines or moving product, and let automation fill the void.
Inkjet Solder Mask
Johnson: It looks like the technology on inkjet solder mask is emerging into its own. Would you detail the steps that get removed from the process when you move to inkjet solder mask?
Perry: You willstill do a direct write like you would with a direct imaging machine. The advantage now is you have no coating process.
The first step that’s removed is the coating of the solder mask application: any equipment or manual operation that is used to screen print, flood coat panels, or even spray coat panels. That process is quite inefficient because there’s a lot of process steps involved and wasted solder mask. With inkjet applications, we’re printing everything that we’re using, so there’s little to no waste. You can print the mask where you want, and not have to flood coat an entire panel.
That would be the first advantage. Another is reduction of VOCs because you have a lot of them in the conventional solder mask process, during the coating application; with inkjet, we’re eliminating that element of the process. It’s a big advantage as the industry moves toward being as green as possible, in specified regions.
Direct Imaging
Barry Matties: Direct imaging is one technology that always seemed to offer a great ROI, but with a heavy investment. Is that a good ROI? What are the trends? Are more people looking for it, or is the market where it needs to be?
Perry: There’s been a definite industry shift toward direct imaging. Most of the shops now have some form of direct imaging machinery and there are more players in the market. There are still a small handful of shops who don’t have it, though.
The drive for direct imaging (DI) has now shifted into the solder mask area for improved throughput and quality. The initial effort was for fabricators to use DI in the inner layer area because that is where they could realize the most cost savings impact, and then the technology was adopted in the outer layer imaging area. Now with the introduction of high-powered LEDs to image the solder mask, the new DI machines are delivering improved throughput, along with high resolution. Eventually, I think the move to inkjet solder mask will be a market shift in the near future as the equipment matures.
Medina: The DI primary imaging equipment being purchased today isn’t as much about ROI as it is about the capability of the equipment to image finer and finer lines. The mSAP and other semi-additive processes are driving this need. We’re seeing more customers trying to image 0.001" and less.
But in regard to the evolution of this technology, as customers with DI start to upgrade to the new technology, the older models will become available and that will allow the smaller shops to get into DI at a much lower price through the used equipment market.
There is no doubt the market continues to grow the use of DI equipment, but the next step is where inkjet comes in. As that technology evolves, it creates other opportunities for that type of technology to direct write, basically putting the resist just where you want it—rather than coat an entire panel and then remove what we don’t want. That’s a huge cost savings.
To read this entire conversation, which appeared in the May 2022 issue of PCB007 Magazine, click here.
Suggested Items
Driving Innovation: Direct Imaging vs. Conventional Exposure
07/01/2025 | Simon Khesin -- Column: Driving InnovationMy first camera used Kodak film. I even experimented with developing photos in the bathroom, though I usually dropped the film off at a Kodak center and received the prints two weeks later, only to discover that some images were out of focus or poorly framed. Today, every smartphone contains a high-quality camera capable of producing stunning images instantly.
Hands-On Demos Now Available for Apollo Seiko’s EF and AF Selective Soldering Lines
06/30/2025 | Apollo SeikoApollo Seiko, a leading innovator in soldering technology, is excited to spotlight its expanded lineup of EF and AF Series Selective Soldering Systems, now available for live demonstrations in its newly dedicated demo room.
Indium Corporation Expert to Present on Automotive and Industrial Solder Bonding Solutions at Global Electronics Association Workshop
06/26/2025 | IndiumIndium Corporation Principal Engineer, Advanced Materials, Andy Mackie, Ph.D., MSc, will deliver a technical presentation on innovative solder bonding solutions for automotive and industrial applications at the Global Electronics A
Fresh PCB Concepts: Assembly Challenges with Micro Components and Standard Solder Mask Practices
06/26/2025 | Team NCAB -- Column: Fresh PCB ConceptsMicro components have redefined what is possible in PCB design. With package sizes like 01005 and 0201 becoming more common in high-density layouts, designers are now expected to pack more performance into smaller spaces than ever before. While these advancements support miniaturization and functionality, they introduce new assembly challenges, particularly with traditional solder mask and legend application processes.
Knocking Down the Bone Pile: Tin Whisker Mitigation in Aerospace Applications, Part 3
06/25/2025 | Nash Bell -- Column: Knocking Down the Bone PileTin whiskers are slender, hair-like metallic growths that can develop on the surface of tin-plated electronic components. Typically measuring a few micrometers in diameter and growing several millimeters in length, they form through an electrochemical process influenced by environmental factors such as temperature variations, mechanical or compressive stress, and the aging of solder alloys.