Estimated reading time: 6 minutes
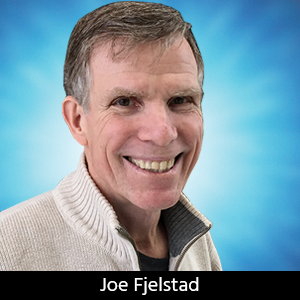
Flexible Thinking: The Many Benefits of Eliminating (Most) Solder
“It is vanity to do with more that which can be done with less.” —William of Occam, 14th century monk, logician, and philosopher
Many scientists are familiar with the concept of Occam’s Razor (also sometimes called the Law of Parsimony). The basic idea postulates that when attempting to explain any given observed phenomena, the simplest explanation is preferable to those which are more complex. The reasoning behind the concept is that simple theories are easier to examine and verify, and not coincidently, are more often found to be true. Simplicity is a theme that has been recommended by some of the greatest minds in history. “Simplify, simplify,” urged Thoreau. Einstein advised, “Everything should be made as simple as possible, but not simpler.” These great teachers are both instructional and inspirational; while echoed throughout history, their words are not always followed because it is, ironically and unfortunately, easier to make things more complex. Yet these touchstone words have held sway over me for most of my life.
With that in mind, I will postulate that some long-time readers of my musings may be familiar with the Occam Process, which I first proposed in 2007 on the heels of the EU ban of lead in electronics solder. The Occam Process proposed to eliminate concerns about lead in solder by eliminating solder (and the root cause of perhaps as much as 70% of failures, according to a relatively recent scholarly paper1) from most (if not all) electronics manufacturing.
Having been influenced by the industry’s roots in 100-mil-center designs predicated on the lead pitch of a ubiquitous dual-in-line package (DIP), the idea of a standard grid was something that just made sense to me. Thus, the idea of solderless assembly was tied together and accompanied by a notion that all SMT IC packaging industry (which had allowed lead pitches and formats to explode in the conversion to SMT) in the future could/should minimize the number of lead pitches, preferably to a single, standard base grid pitch akin to the beauty and simplicity of the earlier 100 mil pitch. From a single base, the package developer could depopulate to meet the majority of IC package needs. The suggestion was 0.5 mm and that all package designs have terminations on that grid—making design layout much simpler. Further, it was suggested that all terminations be simply copper (i.e., no solderable finishes such as solder, nickel-gold, or the like). Because no solder would be used in assembly (all connections would be made by copper plating), the devices would not be subjected to high temperature processes associated with first attaching solder balls at high temperature, then mounting them to a PCB with one or more additional thermal cycles, which cumulatively reduce device and substrate reliability.
Several years ago, I wrote a short, simple book on the Occam Process titled Solderless Assembly for Electronics—the SAFE Approach2. While, it did not make the New York Times best-seller list, it has nevertheless enjoyed decent circulation for a technical book. But it occurred to me that I could simplify my message further and set my sights on creating a one-page comparison of Occam with traditional PCB manufacture and assembly that anyone might be able to understand. I am providing that list (Table 1) along with a picture of a LEGO “module” that Vern Solberg, my long-time friend and colleague, created at my request with the LEGOs and my simple instructions to visually illustrate the idea in a way anyone might understand. The purpose was to help the customers of Tessera, the pioneering chip-scale packaging company where we both worked in the mid-1990s, to visualize and appreciate the huge potential value of using a common pitch for all devices. Darren Smith, the brilliant electronic interconnect designer and colleague, went a step further to demonstrate the potential3 by reducing his original design effort by roughly 70% in size while taking the original layer count down from 12 layers to six without reverting to the use of extreme fine lines.
So, to keep things simple, a list is shown in Table 1 as it stands now. I expect the list will get longer as more distinct benefits of solder-free assembly are recognized.
Conclusion
Soldering is a complex process where many things can and do routinely go wrong. It is far from perfect in both yield and reliability; however, I have frequently mentioned in my presentations over the past decade that it will continue to be used for assembly well into the foreseeable future. In all honesty, I can see important places where solder can and will work in the future of electronic manufacturing.
Unfortunately, familiarity with a process does not make it infallible. I am reading with increasing frequency the myriad problems of solder along with the proposals for the next lead-free solder alloy (78 alloys at last count), the next best flux, the best way to characterize the reflow process, the most recent problem identified, and the best piece of equipment to identify that problem and tool to fix it. I graphically characterized the soldering industry in my SAFE book as a modern-day Sisyphus; instead of a boulder, it’s characterized as pushing a solder ball up a hill only to have it roll down again for another push to the top the next day. Job security, for sure, but at what cost to the soul?
There are better ways to execute most routine activities, but they typically require an appetite for change, and though inevitable, can be frightening. The Wright brothers did not make their first flight off a cliff; they did it on a sandy beach. They were not fools, but they did understand the potential benefits of flight and so met their fear head on. Today, it is safer to be at 40,000 feet than it is to be on the ground and air travel is the safest possible way to get around. I believe that future designers will eventually see the benefit of designing products using the principles which Occam gifted the world eight centuries ago. Again, to make things simple.
This inspirational quote on the topic of design simplicity is from esteemed French writer Antoine de Saint-Exupéry in his autobiography, Wind, Sand and Stars, “A (good) designer knows that he has achieved perfection in design not when there is nothing left to add but when there is nothing left to take away.”
Personal note: It is with great sadness that I share here news that my colleague Darren Smith died by his own hand in April after decades of physical and mental suffering. We spoke of his suffering on numerous occasions but unfortunately his depression won out. Darren’s great enthusiasm for the Occam idea (which included his getting a personalized OCCAM license plate for his car) was immense but insufficient to keep him in life. If the reader is having such problems, please seek professional help through a suicide prevention service. The industry needs you to stick around.
This column originally appeared in the June 2022 issue of Design007 Magazine.
Joe Fjelstad is founder and CEO of Verdant Electronics and an international authority and innovator in the field of electronic interconnection and packaging technologies with more than 185 patents issued or pending. Download your copy of Fjelstad’s book Flexible Circuit Technology, 4th Edition, and watch his in-depth workshop series, “Flexible Circuit Technology.”
More Columns from Flexible Thinking
Flexible Thinking: The Key to a Successful Flex Circuit Design TransferFlexible Thinking: Flexible Circuit Technology—Looking Back and Forward
Flexible Thinking: Mind-tapping into January
Flexible Thinking: Another PCB Design Paradigm Shift in the Works
Flexible Thinking: Rules of Thumb—A Word to the Wise
Flexible Thinking: Musings on High Density Interconnections
Flexible Thinking: Integrated Passive Devices—Design Solutions With Many Benefits
Flexible Thinking: Mechatronics in a Flex World