-
- News
- Books
Featured Books
- design007 Magazine
Latest Issues
Current IssueProper Floor Planning
Floor planning decisions can make or break performance, manufacturability, and timelines. This month’s contributors weigh in with their best practices for proper floor planning and specific strategies to get it right.
Showing Some Constraint
A strong design constraint strategy carefully balances a wide range of electrical and manufacturing trade-offs. This month, we explore the key requirements, common challenges, and best practices behind building an effective constraint strategy.
All About That Route
Most designers favor manual routing, but today's interactive autorouters may be changing designers' minds by allowing users more direct control. In this issue, our expert contributors discuss a variety of manual and autorouting strategies.
- Articles
- Columns
- Links
- Media kit
||| MENU - design007 Magazine
Estimated reading time: 7 minutes
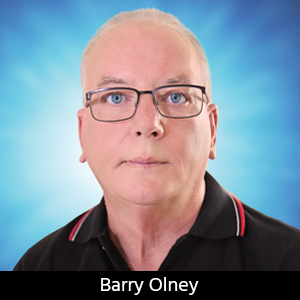
Beyond Design: 2D Field Solver–An Essential Tool for High-speed PCB Design
A field solver is the engine behind signal and power integrity analysis. You never see it, but it performs all the magic of simulation. In its elementary form, the field solver can employ Maxwell’s equations to calculate the parasitic elements of a solution space. This method is referred to as 2D extraction and is used to analyze and synthesize a stackup to achieve a target single-ended or differential impedance. The velocity of propagation can also be extracted to perform signal integrity analysis. A field solver can be used as a stand-alone tool or as part of a simulation environment. In this month’s column, I will look at 2D field solvers.
An electromagnetic (EM) field is produced when a logic driver delivers a high-speed, fast rise-time pulse into a transmission line. The EM wave propagates along the length of the trace radiating into the surrounding dielectric material and coupling energy to nearby trace segments. These EM fields are not restricted to the multilayer substrate and if proper care is not taken may emit radiation causing electromagnetic interference. If the impedance of the driver and load do not match the transmission line, then reflections occur, and radiation is created. Hence, the need for impedance control.
Figure 1: A 2D boundary element method field solver. (Source iCD Stackup Planner)
In a uniform cross-section transmission line, a propagating signal sees the same instantaneous impedance all the way down the line. There is one value of the instantaneous impedance (characteristic impedance) that distinguishes the transmission line. It depends only on the cross-section of the transmission line and the surrounding material properties. 3D field solvers are not more accurate than 2D field solvers in stackup design. When interconnects are uniform transmission lines, a 2D field solver can be more accurate, faster, and much easier to use.
Electromagnetic behavior is governed by Maxwell's equations, and all parasitic extraction requires solving some form of these equations. There are numerous types of field solvers but for 2D field solvers, the appropriate form of Maxwell's equations is typically solved by one of two classes of methods.
The first uses a differential form of the governing equations and requires the meshing of the entire domain in which the electromagnetic fields reside. Two of the most common approaches in this first class are the finite difference (FD) and finite element (FEM) methods. The resultant linear matrix that must be solved is large but sparse.
The second class of methods is integral equation methods which instead require an evaluation of only the sources of the electromagnetic field. Those sources can be physical quantities, such as the surface charge density or mathematical abstractions resulting from the application of Green's theorem. When the sources exist only on two dimensional surfaces for three dimensional problems, the method is often called method of moments (MoM), or boundary element method (BEM), as illustrated in Figure 1. For open boundary conditions, the sources of the field exist in a much smaller domain than the fields themselves, and thus the size of the matrix generated by the integral equations methods is much smaller than FEM. Since the BEM results in a smaller solution space, it is considered faster than other 2D solvers.
The most effective planning tool for optimizing the stackup of a PCB is a 2D field solver. This tool can be used to predict the characteristic impedance and differential impedance for all topologies, including microstrip, stripline, and dual stripline. The other advantage of a 2D field solver is its ability to include second-order effects such as trace thickness, the influence of solder mask, and mixed prepreg dielectrics. These solvers are limited to the numerical accuracy of solving Maxwell’s equations, which generally are accurate to better than 1%. Therefore, a 2D field solver should be used as your design tool of choice.
Accuracy is important because of yield. Any inaccuracy in the predicted impedance will shift the center position of the distribution of the PCB fabricators' target impedance. Customers usually request ±10% tolerance so, with an accuracy of 1%, the field solver is the least of the fabricators' worries. The absolute accuracy of the manufactured product can be evaluated by comparison to measurements on well-characterized test vehicles as well as on production boards. There are many steps to get the fabrication process right, and the field solver is one of the most reliable links in the chain. For instance, typical results of better than 3% tolerance (including fabrication variables) are achieved by iCD customers (Figure 2).
The field solver is very accurate but if one incorrectly models the structures or incorrectly enters the dielectric constant or other properties, then the field solver is hardly to blame when you get erroneous results. Using the exact materials that are stocked by your preferred fabricator can increase accuracy by up to 5%. That is why the availability of a comprehensive dielectric materials library and dielectric material selection is so important.
Years ago, when clock frequencies were low and signal rise times were slow, selecting a dielectric material for your PCB was not difficult—we all just used FR-4. We didn’t really care about the properties of the materials. However, with today’s multi-gigabit designs, with extremely fast rise times and tight margins, precise material selection is crucial to the performance of the product. Materials used for the fabrication of the multilayer PCB absorb high frequencies and reduce edge rates. That loss in the transmission lines is a major cause of signal integrity issues. But we are not all designing cutting-edge boards and sometimes we tend to over-specify requirements that can lead to inflated production costs.
Over the years, a huge range of materials has been developed for multilayer PCB fabrication. In fact, to give you an idea, iCD now has a choice of over 700 series of dielectric materials from over 60 different manufacturers, in its dielectric materials library. When each material is used for the right target application, the resultant PCB will have the lowest possible cost while still satisfying the design and performance goals of the project. Selecting the best material for an application is often a daunting task. One needs to quickly sort through the vast array of choices to make an informed decision.
Figure 3 plots the loss properties of dielectric materials from a fabricator. One can easily see which materials are best for high-speed applications and can choose a few materials from this that are in stock. Cost-to-performance evaluations must still be done to ensure the lowest cost material that will do the job is selected. Keep in mind that material costs vary with quantity.
Matching material performance numbers of the dielectric constant (Dk) is also important. A small difference in this value between materials can impact impedance, line widths/clearances, and thus losses significantly. Also, the dielectric constant of a material determines the propagation speed of the signal in the medium. So, if Dk values vary on different layers of the substrate, then bus timing may also be an issue. One should consider construction options that allow a drop-in material that matches the impedance for each mirrored layer of the stackup.
As signal speeds get up into the gigahertz range, the 2D field solver is an essential tool that every PCB designer must employ to maintain design integrity and performance. Impedance is the foundation of the system performance and reliability, so using a 2D field solver to get it right is not an option.
Key Points
- Field solvers employ Maxwell’s equations to calculate the parasitic elements of a solution space.
- EM fields are not restricted to the multilayer substrate and if proper care is not taken may emit radiation causing electromagnetic interference.
- In a uniform cross-section transmission line, a propagating signal sees the same instantaneous impedance all the way down the line.
- Since the 2D BEM solver results in a smaller solution space it is considered faster than other 2D solvers.
- Filed solvers are limited to the numerical accuracy of solving Maxwell’s equations, which generally are accurate to better than 1%.
- There are many steps to get the fabrication process right, and the field solver is one of the most reliable links in the chain.
- Using the exact materials that are stocked by your preferred fabricator can increase accuracy by up to 5%.
- Materials, used for the fabrication of the multilayer PCB, absorb high frequencies, and reduce edge rates; that loss in the transmission lines is a major cause of signal integrity issues.
- When each material is used for the right target application, the resultant PCB will have the lowest possible cost while still satisfying the design and performance goals of the project.
- If dielectric constant values vary on different layers of the substrate then bus timing may also be an issue.
References
Beyond Design: “Predicting and Measuring Impedance,” “It’s a Material World,” “Stackup Planning Parts 1-6”
“Signal and Power Integrity—Simplified,” by Eric Bogatin
Wikipedia: Electromagnetic field solvers.
This column originally appeared in the July 2022 issue of Design007 Magazine.
More Columns from Beyond Design
Beyond Design: Effective Floor Planning StrategiesBeyond Design: Refining Design Constraints
Beyond Design: The Metamorphosis of the PCB Router
Beyond Design: Radiation and Interference Coupling
Beyond Design: Key SI Considerations for High-speed PCB Design
Beyond Design: Electro-optical Circuit Boards
Beyond Design: AI-driven Inverse Stackup Optimization
Beyond Design: High-speed Rules of Thumb