-
- News
- Books
Featured Books
- pcb007 Magazine
Latest Issues
Current IssueSales: From Pitch to PO
From the first cold call to finally receiving that first purchase order, the July PCB007 Magazine breaks down some critical parts of the sales stack. To up your sales game, read on!
The Hole Truth: Via Integrity in an HDI World
From the drilled hole to registration across multiple sequential lamination cycles, to the quality of your copper plating, via reliability in an HDI world is becoming an ever-greater challenge. This month we look at “The Hole Truth,” from creating the “perfect” via to how you can assure via quality and reliability, the first time, every time.
In Pursuit of Perfection: Defect Reduction
For bare PCB board fabrication, defect reduction is a critical aspect of a company's bottom line profitability. In this issue, we examine how imaging, etching, and plating processes can provide information and insight into reducing defects and increasing yields.
- Articles
- Columns
- Links
- Media kit
||| MENU - pcb007 Magazine
Gov. Kemp: Denkai America to Locate New Manufacturing Facility, N.A. Headquarters in Richmond County
July 20, 2022 | Governor Brian P. KempEstimated reading time: 3 minutes
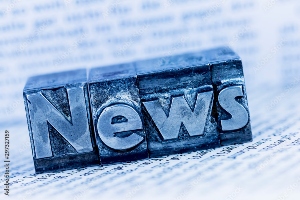
Governor Brian P. Kemp announced that Denkai America, the only North American manufacturer of high-quality electrodeposited (ED) copper foil used in printed electronics, will locate its new manufacturing facility and North American Headquarters in Richmond County. The company’s initial investment will be $150 million to establish an ED copper foil production facility, with a focus on electric vehicle (EV) battery foil, on a 115-acre site, with a goal to invest a total of $430 million and create 250 new jobs over the next five years.
"Georgia is proud to be selected as the home of Denkai America, further strengthening our state's status as a leader in the emerging electric mobility and existing aerospace, defense, and technology industries," said Governor Kemp. "We have been laser focused on bringing quality jobs to highly-trained, hardworking Georgians across the state, and we look forward to seeing one-of-a-kind companies like Denkai thrive in Georgia’s top-ranking pro-business environment."
Denkai America’s materials have traditionally been used in printed circuit board (PCB) applications, primarily for the aerospace and defense industries, but are also now used in the lithium-ion batteries powering electric vehicles. Operating for more than 60 years, Denkai has team members worldwide with operations in Japan and North America.
"This investment highlights our commitment to leading ED battery foil manufacturing in North America for many years to come," said Heday Nakajima, Ph.D., Denkai Group President and CEO. "We are grateful to the teams in Richmond County and the State of Georgia for making this project possible."
“We are thrilled to expand our manufacturing presence into Augusta, which has the skilled and talented work force our company needs for growth,” said Nobu Masuda, Denkai America’s President and CEO.
Construction is expected to begin in September 2022 as the first part of a three-phase investment, and the facility will be fully operational by December 2024. The company will be hiring for skilled industrial technicians, production managers, and engineers. Interested applicants can learn more and apply at Denkai America's website.
"The Development Authority of Augusta, Georgia, is excited to welcome Denkai America and its North American Headquarters to the Augusta Corporate Park. We know they will be a great corporate citizen and bring high-skilled jobs to the growing list of companies that call Augusta and the Augusta Corporate Park home," said Steven Kendrick, Chairman of the Augusta Economic Development Authority. "We look forward to the great jobs and investment that they will bring to Augusta. We also would like to thank the Augusta Commission and the Augusta Utilities Department for their support and hard work to make this happen."
Global Commerce Director of Corporate Solutions and Cyber Security Barton Lowrey represented the Georgia Department of Economic Development (GDEcD) on this competitive project in partnership with the Augusta Economic Development Authority, Georgia Power, and Georgia Quick Start. As the Technical College System of Georgia’s nationally ranked workforce training program, Georgia Quick Start has provided specialized training tailored specifically to business needs for more than 40 years.
"As the adoption of electric mobility becomes widespread, the State of Georgia is committed to harnessing this generational opportunity to ensure that Georgians employed in today’s automotive industry will have access to these jobs of the future here at home. Denkai America plays a vital role in the EV ecosystem, and we are excited to welcome this innovative company to Augusta and Richmond County," said GDEcD Commissioner Pat Wilson. "This investment is also further evidence of how Georgia’s commitment to building lasting international relationships continues to drive economic partnerships across our state, including the recruitment of the wider electric mobility value chain. Congratulations to our partners in this project!"
Georgia’s prime location, extensive infrastructure, skilled workforce, and business-friendly climate has made it an attractive location for a diverse array of rapidly developing industries focused on creating a sustainable future. Georgia is cultivating a vertically integrated supply chain that will help companies increase efficiencies by reducing the reliance on imported materials. EV-related projects have contributed more than $12.6 billion in investments and more than 17,800 new jobs to Georgia since 2020.
Augusta Corporate Park is a Georgia Ready for Accelerated Development (GRAD) Certified park. To earn a GRAD program certification, a property must undergo due diligence and complete specific certification requirements prior to a visit by a prospective business. Completing the GRAD certification program with the Georgia Department of Economic Development is a proactive way both community planners and landowners can help catalyze economic growth and industrial development for the regions they serve.
Suggested Items
I-Connect007 Editor’s Choice: Five Must-Reads for the Week
07/18/2025 | Nolan Johnson, I-Connect007It may be the middle of the summer, but the news doesn’t quit, and there’s plenty to talk about this week, whether you’re talking technical or on a global scale. When I have to choose six items instead of my regular five, you know it’s good. I start by highlighting my interview with Martyn Gaudion on his latest book, share some concerning tariff news, follow that up with some promising (and not-so-promising) investments, and feature a paper from last January’s inaugural Pan-European Design Conference.
Elephantech Launches World’s Smallest-Class Copper Nanofiller
07/17/2025 | ElephantechJapanese deep-tech startup Elephantech has launched its cutting-edge 15 nm class copper nanofiller – the smallest class available globally. This breakthrough makes Elephantech one of the first companies in the world to provide such advanced material for commercial use.
Copper Price Surge Raises Alarms for Electronics
07/15/2025 | Global Electronics Association Advocacy and Government Relations TeamThe copper market is experiencing major turbulence in the wake of U.S. President Donald Trump’s announcement of a 50% tariff on imported copper effective Aug. 1. Recent news reports, including from the New York Times, sent U.S. copper futures soaring to record highs, climbing nearly 13% in a single day as manufacturers braced for supply shocks and surging costs.
I-Connect007 Editor’s Choice: Five Must-Reads for the Week
07/11/2025 | Andy Shaughnessy, Design007 MagazineThis week, we have quite a variety of news items and articles for you. News continues to stream out of Washington, D.C., with tariffs rearing their controversial head again. Because these tariffs are targeted at overseas copper manufacturers, this news has a direct effect on our industry.I-Connect007 Editor’s Choice: Five Must-Reads for the Week
Digital Twin Concept in Copper Electroplating Process Performance
07/11/2025 | Aga Franczak, Robrecht Belis, Elsyca N.V.PCB manufacturing involves transforming a design into a physical board while meeting specific requirements. Understanding these design specifications is crucial, as they directly impact the PCB's fabrication process, performance, and yield rate. One key design specification is copper thieving—the addition of “dummy” pads across the surface that are plated along with the features designed on the outer layers. The purpose of the process is to provide a uniform distribution of copper across the outer layers to make the plating current density and plating in the holes more uniform.