-
- News
- Books
Featured Books
- design007 Magazine
Latest Issues
Current IssueProper Floor Planning
Floor planning decisions can make or break performance, manufacturability, and timelines. This month’s contributors weigh in with their best practices for proper floor planning and specific strategies to get it right.
Showing Some Constraint
A strong design constraint strategy carefully balances a wide range of electrical and manufacturing trade-offs. This month, we explore the key requirements, common challenges, and best practices behind building an effective constraint strategy.
All About That Route
Most designers favor manual routing, but today's interactive autorouters may be changing designers' minds by allowing users more direct control. In this issue, our expert contributors discuss a variety of manual and autorouting strategies.
- Articles
- Columns
- Links
- Media kit
||| MENU - design007 Magazine
Material Conservation Demands Stakeholder Buy-in
August 10, 2022 | I-Connect007 Editorial TeamEstimated reading time: 3 minutes
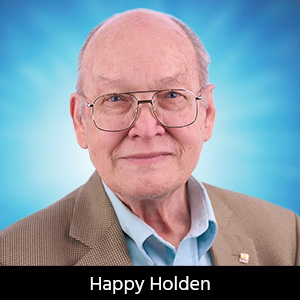
With the supply chain problem showing no signs of letting up, the idea of designing PCBs with fewer materials has begun to take hold. So, as we mapped out this issue on conserving materials, we knew it was important to hear from Happy Holden about this topic. Here’s why:
Happy has been a proponent of cost-aware PCB design for decades. At HP, Happy helped develop the relative cost index (RCI), which allows PCB designers to compare the costs of PCB structures and their alternatives. With this in mind, we spoke with Happy about the potential benefits of designing for material conservation, and why many of the old design concepts may be ripe for updating, such as the 0.062" board.
Barry Matties: Happy, in the past you mentioned that 75% to 80% of the cost of the board is controlled by design and just 20% by the fabricator. To help designers control cost, you developed a relative cost index. Tell us about that.
Happy Holden: We came up with the relative cost index because it was almost impossible to get fabricators to provide cost predictors. First, they didn't want to have people hold their feet to the fire in case you left something out. Second, they were unsure if the information would get out to their competitors. So, we came up with the relative cost index. It allows you to compare architecture design alternatives as a percent savings or percent increase in cost from that fabricator. It doesn't give you the absolute value, although the RCIs are calculated based on the costs of a conventional eight-layer FR-4 through-hole multilayer PCB.
Matties: So, you have a benchmark board, and then you're either adding or subtracting based off that benchmark.
Holden: In terms of percentages, not in terms of dollars. It’s only good for that fabricator because some other fabricator, depending on their eight-layer through-holes and what they charge, will have different RCIs. But at least RCIs give you some help in design when you're comparing alternatives.
Matties: Are the designers driven to reduce cost or conserve material, or are they just driven by schedule?
Holden: They're singularly driven by schedule.
Matties: Now with supply chain issues hitting, though, I would think that they have to now start thinking about reducing the number of materials they use in each PCB.
Holden: Ah, yes, and that's the big bugaboo. This came out of nothing, that now people who can't get to components, you've got to change this component, which changes its footprint, etc. The whole supply chain and virus lockdown has changed many rules, but nothing is available. Nobody was prepared for this. I've had that RCI chart out for 30 years now. Manufacturers actually like how bad designers are because that gives them a much greater profit. If designers were designing optimally, much of their extra profits would go away, so what's their incentive to educate the designer to do it better?
Matties: That's the question that's percolating in my mind. What's the incentive for the designer to conserve material?
Holden: Right now, his biggest incentive is getting his boards out, and figuring out what he’s going to do when fabricators come back with a huge increase in pricing on materials because of the scarcity.
Matties: Inflation is the driver, of course. We have to lower the cost by whatever means we have, because of supply chain issues. So, you have double incentive to create a shift in the paradigm.
Holden: Yes, but nobody teaches this. So, how does a designer learn this?
Dan Feinberg: Happy, I don't think that the design team's management rewards them for this sort of behavior.
Holden: Yes. It certainly will punish them if they don't meet the schedule, but it won’t necessarily reward them. You're right.
Matties: So, you fall back on tried-and-true methods. You just need to make sure that this is functional, rather than spending a lot of time saving the company money when there's little in it for you individually.
Holden: If you sandbag and over-design a board, it still works, and only its cost goes up. But if you're trying to minimize the cost, then you've taken on risk, in terms of meeting the schedule and everything else. You know how much everybody likes to avoid risk. The solution to risk aversion is just to make things more complicated and expensive. At least it won't come back to you.
To read this entire conversation, which appeared in the August issue of Design007 Magazine, click here.
Testimonial
"The I-Connect007 team is outstanding—kind, responsive, and a true marketing partner. Their design team created fresh, eye-catching ads, and their editorial support polished our content to let our brand shine. Thank you all! "
Sweeney Ng - CEE PCBSuggested Items
Global PCB Connections: Understanding the General Fabrication Process—A Designer’s Hidden Advantage
08/14/2025 | Markus Voeltz -- Column: Global PCB ConnectionsDesigners don’t need to become fabricators, but understanding the basics of PCB fabrication can save you time, money, and frustration. The more you understand what’s happening on the shop floor, the better you’ll be able to prevent downstream issues. As you move into more advanced designs like HDI, flex circuits, stacked vias, and embedded components, this foundational knowledge becomes even more critical. Remember: the fabricator is your partner.
The Art and Science of PCB Floor Planning: A Comprehensive Guide
08/14/2025 | Cory Grunwald and Jeff Reinhold, Monsoon SolutionsPCB design is an intricate and crucial part of developing electronic products. One of the foundational stages of PCB design is floor planning, a phase where the placement of components and the flow of signals are meticulously mapped out. A good floor plan ensures that the PCB performs well, is easy to manufacture, and meets all mechanical and electrical requirements. We’ll explore the essential aspects of floor planning, from its objectives and process to the challenges that designers face.
EnSilica Establishes New EU Mixed-Signal Design Centre in Budapest, Hungary
08/12/2025 | EnSilicaThe facility strengthens EnSilica’s presence in the European Union and taps into Budapest’s deep technology ecosystem, which hosts numerous leading automotive and industrial multinationals. This expansion will increase the Group’s global headcount to around 210 employees.
Happy’s Tech Talk #41: Sustainability and Circularity for Electronics Manufacturing
08/13/2025 | Happy Holden -- Column: Happy’s Tech TalkI attended INEMI’s June 12 online seminar, “Sustainable Electronics Tech Topic Series: PCBs and Sustainability.” Dr. Maarten Cauwe of imec spoke on “Life Cycle Inventory (LCI) Models for Assessing and Improving the Environmental Impact of PCB Assemblies,” and Jack Herring of Jiva Materials Ltd. spoke on “Transforming Electronics with Recyclable PCB Technology.” This column will review information and provide analysis from both presentations.
Elementary, Mr. Watson: Why Your PCB Looks Like a Studio Apartment
08/13/2025 | John Watson -- Column: Elementary, Mr. WatsonIn November 2022, I wrote a column called "Is Your Bathroom in the Kitchen?" This piece related a bizarre real estate listing that emerged out of St. Louis that had architects scratching their heads and interior designers cringing. Nestled in the historic Central West End sat a 200-square-foot apartment that completely defied logic. It wasn't the size that raised eyebrows, it was the layout. Here's the kicker: While that's rare in real estate, it's shockingly common in PCB design.