-
- News
- Books
Featured Books
- design007 Magazine
Latest Issues
Current IssueProper Floor Planning
Floor planning decisions can make or break performance, manufacturability, and timelines. This month’s contributors weigh in with their best practices for proper floor planning and specific strategies to get it right.
Showing Some Constraint
A strong design constraint strategy carefully balances a wide range of electrical and manufacturing trade-offs. This month, we explore the key requirements, common challenges, and best practices behind building an effective constraint strategy.
All About That Route
Most designers favor manual routing, but today's interactive autorouters may be changing designers' minds by allowing users more direct control. In this issue, our expert contributors discuss a variety of manual and autorouting strategies.
- Articles
- Columns
- Links
- Media kit
||| MENU - design007 Magazine
Estimated reading time: 6 minutes
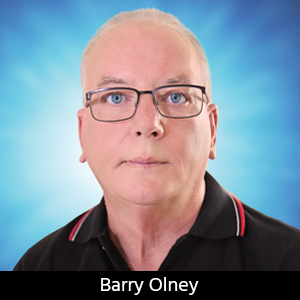
Beyond Design: PCB Design Strategies to Reduce Costs
There are numerous ways to improve the PCB design and production processes and thereby reduce costs, from fundamental improvements involving a standard form factor and reducing the board size and complexity, to technology choices and simulation to reduce iterations. A good starting point would be the IPC standards developed by the electronics industry to enhance manufacturability, testability, and assembly. Anyone new to PCB development should initially begin with these standards and then fine-tune them to capture the essence of their design style.
The adoption of surface mount technology (SMT) and the increased use of high-density interconnects (HDIs) has enabled more functionality per unit area than conventional plated through-hole (PTH) PCBs. The semi-additive process (SAP) takes this one step further by reducing the size of wearable devices. These technologies are also ideal for high-speed design as they reduce transmission line length, hence, reflections and lower inductance of the power/ground system. With no component leads the assembly can be automated, dramatically reducing production time and cost.
Via technology is another consideration. Plated through-hole vias are the most affordable and should be used whenever possible. Blind and buried vias will increase your costs. They’re only necessary on high-density and high-frequency complex boards, so you should typically not need them. Microvias are relatively costly for simpler designs, but for more sophisticated PCBs and prototypes, they are the prime solution. They also reduce layer count which is a cost-saving. Blind and buried vias are also used to reduce the board aspect ratio. The minimum via hole is determined by drill size as well as the aspect ratio, which is the thickness of the PCB divided by the diameter size of the drilled hole. There is usually an additional manufacturing cost for aspect ratios higher than 8:1 for PTH and 0.8:1 for microvias.
The efficiency and design freedom provided by blind and buried microvias are some of the reasons why PTHs are rapidly becoming a thing of the past for complex designs, especially since most of the components that require PTHs to be mounted on a PCB are bulky and space-consuming, whereas dense BGA designs are more suited to the use of microvias.
Cost is also relative to the trace/clearance requirements of the technology employed. The larger the trace/clearance, the less the cost. Going below 4/4 mil technology will incur a cost premium. The use of mixed signal/power planes can reduce the need for additional plane layers to keep the layer count down. Look for different design options to make sure your board is as simple as possible. Not only do you want to optimize the elements of the board, but you’ll also want it on a small form factor that still provides appropriate clearance for every element.
Material selection is another cost consideration. When each material is used for the right target application, the resultant PCB will have the lowest possible cost while still satisfying the design and performance goals of the project.
In Figure 1, I have selected a 10 GHz Isola TerraGreen material with a Dk of 3.3 and a dissipation factor (Df) of 0.003 for its low loss capabilities. Now, this may be necessary for our high-speed DDR4 signals but is not a good pick for planar capacitance. For fast rise time signals, we need a low dissipation factor with low loss. However, for planar capacitance (between power/ground planes), we need a very thin dielectric with a high dielectric constant. The capacitance (C) of a parallel plate capacitor (plane) is relative to plane area (A), the dielectric thickness (d), and the dielectric constant (Dk).
For a high distributed capacitance, we need a high Dk, so I have chosen a low-cost Kingboard material (highlighted) with a high Dk of 4.6. Not only will this help reduce the cost but will also help reduce the AC impedance of the power distribution network. You do not have to use the same expensive material throughout the stackup; in this case, the low-cost Kingboard material performs better for its application.
Utilizing efficient EDA tools can also streamline the PCB development cycle. Many improvements in EDA software have helped to structure the design flow effectively and have reduced expenses. The availability of an elaborate component library reduces the rebuilding time and effort. Team sharing software can also drive comprehensive design reviews to improve the quality of the product.
Following the best design constraints won’t necessarily produce a premium product. Across multiple sectors, fields, and disciplines, simulation is having a profoundly positive effect. One of the primary advantages of using simulation software is the fact that it enables one to obtain valuable feedback when designing real-world circuits. Furthermore, this feedback does not come with the time or expenditure typically required to procure this much-needed design insight. This, in turn, allows the designer to determine the efficiency and integrity of their designs without the need to build the product first. Lifecycle Insights (September 2018) found that the average number of respins per project was 2.9, and the average cost of a respin was $28,482. That's an incredible $82,598 for each new product.
Simulation also allows the designer to explore the worthiness of alternate designs without ever building the actual product. Moreover, examining the effects of your design decisions during the design phase rather than the construction phase saves iterations, time, and money, as well as increases design quality.
The cost of development is dramatically reduced if simulation is employed early in the design cycle. If changes are made late in the design process, then it takes more time, people, material, and therefore money, to complete the project. The advantage of simulation is that it identifies issues early in the design process and rectifies them before they become a major problem.
Design changes that occur:
- In the conceptual stage it costs nothing
- During the design stage it requires just a little extra time
- During the test stage means that you must regress one stage
- During production, or worse still, in the field, can cost millions to fix and possibly damage the company’s reputation
Having the project completed on time and within budget, means that costs are cut by reducing the design cycle and generating higher profits due to shorter time-to-market and an extended product life cycle. Having validated the design by simulation, you can be assured of reliable performance.
Key Points
- Anyone new to PCB development should initially begin with the IPC standards and then fine-tune them to capture the essence of their design style.
- The adoption of SMT and the increased use of HDIs have enabled more functionality per unit area than conventional PTH PCBs.
- Plated through-hole vias are the most affordable and should be used whenever possible. Blind and buried vias will increase your costs.
- Dense BGA designs are more suited to the use of microvias.
- The larger the trace/clearance, the less the cost. Going below 4/4 mil technology will incur a cost premium.
- When each material is used for the right target application, the resultant PCB will have the lowest possible cost while still satisfying the design and performance goals of the project.
- Utilizing efficient EDA tools can also streamline the PCB development cycle.
- Simulation enables one to obtain valuable feedback when designing real-world circuits.
- The cost of development is dramatically reduced if simulation is employed early in the design cycle.
- The advantage of simulation is that it identifies issues early in the design process and rectifies them before they become a major problem.
References
Beyond Design columns by Barry Olney: The Key to Product Reliability; Designing for the SAP PCB Fabrication Process; Simulation Slashes Iterations; It’s a Material World.
This column originally appeared in the August 2022 issue of Design007 Magazine.
More Columns from Beyond Design
Beyond Design: Effective Floor Planning StrategiesBeyond Design: Refining Design Constraints
Beyond Design: The Metamorphosis of the PCB Router
Beyond Design: Radiation and Interference Coupling
Beyond Design: Key SI Considerations for High-speed PCB Design
Beyond Design: Electro-optical Circuit Boards
Beyond Design: AI-driven Inverse Stackup Optimization
Beyond Design: High-speed Rules of Thumb