-
-
News
News Highlights
- Books
Featured Books
- pcb007 Magazine
Latest Issues
Current IssueThe Hole Truth: Via Integrity in an HDI World
From the drilled hole to registration across multiple sequential lamination cycles, to the quality of your copper plating, via reliability in an HDI world is becoming an ever-greater challenge. This month we look at “The Hole Truth,” from creating the “perfect” via to how you can assure via quality and reliability, the first time, every time.
In Pursuit of Perfection: Defect Reduction
For bare PCB board fabrication, defect reduction is a critical aspect of a company's bottom line profitability. In this issue, we examine how imaging, etching, and plating processes can provide information and insight into reducing defects and increasing yields.
Voices of the Industry
We take the pulse of the PCB industry by sharing insights from leading fabricators and suppliers in this month's issue. We've gathered their thoughts on the new U.S. administration, spending, the war in Ukraine, and their most pressing needs. It’s an eye-opening and enlightening look behind the curtain.
- Articles
- Columns
- Links
- Media kit
||| MENU - pcb007 Magazine
Estimated reading time: 4 minutes
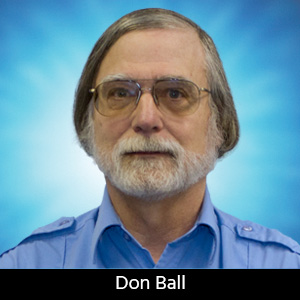
The Chemical Connection: The Etch Factor
One of the biggest obstacles that PCB manufacturers face is etch factor. In the past, I have touched on etch factor in my columns, but to refresh, etch factor is the ratio of downward etch to sideways etch. Etch factor poses challenges to PCB fabricators because it limits PCB design. It can determine how fine a line you can etch, and it can even affect how close together you can have features. For instance, if you wanted to use cupric chloride (etch factor of 3:1) to etch a fine line (3 mils or less), you might not be capable of doing that on panels with thicker copper layers. If you try to do that, you will likely receive inconsistent results throughout your panels. Inconsistencies will arise because there is a point where the sideways etch will affect metal underneath the photoresist and etch it away. This phenomenon, where metal is etched from underneath the photoresist, is known as “undercut” (Figure 1).
In some cases, the undercut for fine lines is so severe that the photoresist will lift off the copper surface, thus exposing the metal to be directly attacked in the etcher and creating the possibility for that feature to be completely etched away.
What Undercut and Etch Factor Have in Common
Throughout the industry, etch factor and undercut are terms typically used interchangeably, despite their differing definitions. This is likely because they are both the result of the one thing that PCB fabricators want to get rid of—sideways etch. Without sideways etch, etch factor and undercut are theoretically nonexistent. If you could remove sideways etching from the etch process, the translation between PCB design and PCB fabrication would have no limitations. You could etch down as far down as you would need without increasing the spaces between features and without decreasing the definition and accuracy of features. Unfortunately, sideways etch is not so easily controlled, and it is often accepted to be a limitation to etching.
How Sideways Etch Has Been Challenged
Although sideways etch has been accepted as a normal obstacle, there have been efforts to combat it. Perhaps the closest copper etching has come to a nearly perfect etch factor was when the PERI-etch process was discovered. The PERI-etch process, also known as powderless etching, was a process that was developed by the Platemakers Educational and Research Institute (PERI) to improve the manufacturing process of copper letterpress printing plates1. This process consisted of an additive to an etching solution that would form a film to protect the sidewalls to prevent them from being etched. Powderless etching gave some promising results of sidewalls from nearly vertical to 30–40 degrees from vertical with no undercutting. Although it gave some promising results for the plate-making industry, some drawbacks limited its wide use in the PCB industry. It was primarily not adopted in PCB production because the additive was meant to work in ferric chloride (FeCl3).
Ferric chloride is an etchant that is sometimes used for PCB fabrication, but it is not often used because the regeneration chemistry is inefficient for large-scale PCB production. Since ferric chloride is based on iron, it is best suited for iron-based metals because it makes regeneration and waste treatment simple and efficient. With copper etching, regeneration of the ferric chloride would not be able to sustain a steady etch rate. As copper content accumulates in the ferric chloride, etch rates decline even with regeneration. Once regeneration becomes ineffective in a large-scale etch process, like PCB fabrication, the profitability of the etch process quickly declines. Since regeneration cannot be performed efficiently, there was never enough reason to justify using powderless etching in large-scale PCB production.
What Could Ideal Etch Factors Mean for SAP?
If somehow you could get both the regeneration of cupric chloride and the vertical sidewalls of powderless ferric chloride etching, I think we would see a dramatic change in the PCB industry. Currently, using the semi-additive process (SAP) is the most practical way to obtain fine features. However, if sideways etch can be efficiently inhibited in the etchants we use today (cupric chloride and alkaline cupric chloride), SAP may not even be necessary in most cases. If you are unfamiliar with SAP, it can be summarized as a process where a copper-plated panel undergoes a selective plating process to form desired features on top of the copper that was already present. Once the features are plated onto the base copper, that panel gets etched to remove the base copper, thus leaving behind only the features that were added. Finding a way around SAP would mean skipping many long and costly steps in the PCB fabrication process. Without requiring SAP to obtain fine features, PCB shops would require less plating equipment and fewer resources to perform plating (i.e., chemicals, trained personnel, time to plate, and operating space).
Conclusion
Although this would be a major game changer in the PCB industry, we seem to be far from obtaining a practical solution with ideal etch factors. The best etch factor with a PCB etchant is the 4:1 ratio you get from maintaining alkaline cupric chloride in its top condition. It begs the question of whether it is possible for copper etching to advance so much that you can get both efficient regeneration capabilities and near perfect etch factors. In the past, we have gotten close to obtaining ideal etch factors, but we did not have the right etchant. Perhaps we could get there with new efforts in chemistry research. If obtaining this quality of etchant is possible, could it ever be enough to replace SAP?
References
- “Member’s Handbook,” Platemakers Educational and Research Institute Inc. (Print)
This column originally appeared in the August 2022 issue of PCB007 Magazine.
More Columns from The Chemical Connection
The Chemical Connection: Through-glass Vias in Glass SubstratesThe Chemical Connection: Reducing Defects in Circuit Board Production
The Chemical Connection: Common Misconceptions in Wet Processing
The Chemical Connection: Surface Finishes for PCBs
The Chemical Connection: Earthquakes, Astronauts, and Aquatics—A Lighter Look at the Past
The Chemical Connection: Better Fabs Attract a Better Workforce
The Chemical Connection: Can Changing Spray Nozzles Improve My Etch Quality?
The Chemical Connection: Getting the Best from Your Cupric Chloride Etchant