-
- News
- Books
Featured Books
- pcb007 Magazine
Latest Issues
Current IssueVoices of the Industry
We take the pulse of the PCB industry by sharing insights from leading fabricators and suppliers in this month's issue. We've gathered their thoughts on the new U.S. administration, spending, the war in Ukraine, and their most pressing needs. It’s an eye-opening and enlightening look behind the curtain.
The Essential Guide to Surface Finishes
We go back to basics this month with a recount of a little history, and look forward to addressing the many challenges that high density, high frequency, adhesion, SI, and corrosion concerns for harsh environments bring to the fore. We compare and contrast surface finishes by type and application, take a hard look at the many iterations of gold plating, and address palladium as a surface finish.
It's Show Time!
In this month’s issue of PCB007 Magazine we reimagine the possibilities featuring stories all about IPC APEX EXPO 2025—covering what to look forward to, and what you don’t want to miss.
- Articles
- Columns
Search Console
- Links
- Media kit
||| MENU - pcb007 Magazine
Pricing Strategies With Michael Carano
September 13, 2022 | I-Connect007 Editorial TeamEstimated reading time: 2 minutes
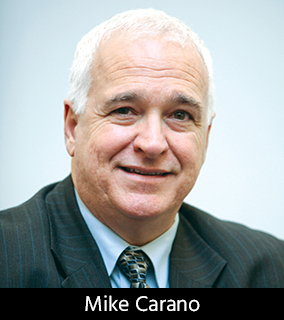
We recently spoke with longtime I-Connect007 columnist Michael Carano, vice president of quality at Averatek, about pricing strategies for PCB fabricators. We’re seeing some movement in this segment as fabricators, already dealing with some of the tightest profit margins around, find themselves having to either raise their prices or trying to massage more revenue out of their already streamlined processes.
We asked Michael for some pricing strategies for fabricators, and he shared a range of options for today’s manufacturers who aren’t afraid to rethink their processes and try new ideas. And, as he says, people will still pay good money for a quality, reliable PCB.
Nolan Johnson: Let’s talk about pricing strategies for fabricators. What are you seeing?
Michael Carano: Let’s step back and think about the price per square inch, or the selling cost. For example, with substrates, people are talking about paying $6 per metal square inch per layer, and that’s pretty darn good money. Now the question is, can you get the yields? If you put these chips up, let’s say 300 on an 18"x24" four-layer, that panel could be an $1,800 to $2,400 panel and be only four layers if you make it in high yields.
Your material cost is about $200 or $300; there’s some labor in that, and you can get pretty good margins on that. Now eventually at higher volumes, if you’re building a hundred million of these a year, obviously it’s going to go down to a dollar per square inch somewhere. But for the mid-range, which could be done here with the DoD, and then some of the high end, you can get $5 or $7 per metal square inch per layer. So, if you have all that in an 18"x24", you just add it up and have $7. It becomes pretty good stuff.
Johnson: Under these current circumstances, for a long time, the fabs have basically had their margins squeezed down to the bare minimum. With this much demand, this much production, everybody this busy, and the supply chain the way it is, is this the time to start to claw back margin?
Carano: Yes, they’re grabbing margin. I think that’s happening because the chemical cost around materials has gone significantly higher in the last year and a half too. That has to translate all the way down to laminate materials, photoresist, and what have you. A lot of times folks want to commoditize a circuit board and they want to get it priced that way, but it is not a commodity. It is a highly functional, critical device and, as I have said, chips don’t float.
Those chips have no circuit board. You can make all the billions of chips you want. They’re not going to go anywhere. Those packages are reliable and when that chip is attached to a BGA substrate that goes on the circuit board, the circuit board has to be reliable, and I think that the message here is we’ve got reliability. We can do higher layer counts, tighter tolerances, and give the OEM more functionality and greater reliability than they’ve ever had before. That has to cost something and you’ve got to pay something for that. It’s time to get those margins back, especially now.
To read this entire conversation, which appeared in the August 2022 issue of PCB007 Magazine, click here.
Suggested Items
Real Time with... IPC APEX EXPO 2025: Benmayor Group—Resistance is Futile: Automation Is the Future
04/11/2025 | Real Time with...IPC APEX EXPOJeff Brandman, president of Aismalibar North America, and Eduardo Benmayor, CEO of Benmayor Group, discuss Benmayor Group's role in electronics and automation, focusing on how automation addresses labor shortages. Jeff, notes that many businesses struggle to find workers for manual tasks, emphasizing the need for various automation solutions to boost productivity. North America lags in automation compared to other regions, which impacts efficiency. Jeff recommends a step-by-step approach to scaling automation, and there's growing acceptance of robots in the workforce, leading to a positive outlook for the future.
Real Time with... IPC APEX EXPO 2025: Exploring Ventec's Innovations
04/09/2025 | Real Time with...IPC APEX EXPOMark Goodwin highlights Ventec's global distribution network and recent expansions in service and equipment offerings. He emphasizes the company's expertise in coating technology for thermal management, specialized materials, and its agility in creating customized solutions for customers.
INEMI Sessions at IPC APEX EXPO Focus is on Board Assembly and PCB & Laminates
03/12/2025 | iNEMIIf you plan to attend the upcoming IPC APEX EXPO in Anaheim, California, be sure to add the INEMI sessions to your calendar. We will have two forward-looking sessions — one on PCB and Laminates and the other on Board Assembly.
Rogers Corporation Launches New Thermoset Laminates for Automotive Radar Sensor Applications
03/03/2025 | Rogers CorporationRogers Corporation (NYSE:ROG) announced its latest innovation in dielectric materials: RO4830™ Plus Circuit Materials, which are well suited for cost-sensitive millimeter wave PCB applications, such as 76-81 GHz automotive corner radar sensors.
Unveiling the Future: Insights on Next-Gen Megtron Materials
02/13/2025 | Marcy LaRont, I-Connect007In this interview from DesignCon, Jim Kenny, OEM business development manager at Panasonic, touches on next-generation Megtron materials and delves into the industry's growing demand for high-speed, low-loss laminate systems, particularly in light of the anticipated 224 gigabits per second technology. With a focus on material development and production timelines, Jim highlights the challenges and opportunities in meeting customer needs while also maintaining quality and supply chain stability. As Panasonic prepares for the evolving landscape, they remain committed to innovating in this competitive market.