-
- News
- Books
Featured Books
- design007 Magazine
Latest Issues
Current IssueProper Floor Planning
Floor planning decisions can make or break performance, manufacturability, and timelines. This month’s contributors weigh in with their best practices for proper floor planning and specific strategies to get it right.
Showing Some Constraint
A strong design constraint strategy carefully balances a wide range of electrical and manufacturing trade-offs. This month, we explore the key requirements, common challenges, and best practices behind building an effective constraint strategy.
All About That Route
Most designers favor manual routing, but today's interactive autorouters may be changing designers' minds by allowing users more direct control. In this issue, our expert contributors discuss a variety of manual and autorouting strategies.
- Articles
- Columns
- Links
- Media kit
||| MENU - design007 Magazine
Estimated reading time: 4 minutes
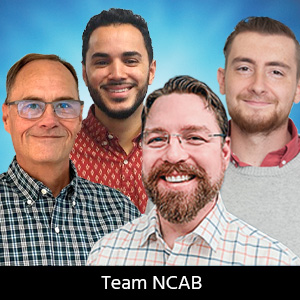
Fresh PCB Concepts: How Large Does That Pad Really Need to Be?
Annular ring is the amount of copper left surrounding the hole after processing. This measurement is taken from the edge of the hole to the edge of the land at the thinnest part. To ensure a robust design, we must design sufficient annular ring for PCB interconnections.
From my field experience, annular ring design is a misunderstood aspect of printed circuit board (PCB) design. Not because it is complex; it is a dry subject with a few moving parts. In the past, I have met many PCB layout engineers who use the following formula to design lands for a given annular ring:
Annular ring = (land size – hole size) / 2
In a perfect world that would be a great way to design PCBs. However, even with modern manufacturing technology and best industry practices, it is not practical. The PCB manufacturing process subjects materials to heat and pressure that cause micro distortions of the materials, and internal layer misalignment. In addition, drill machines are not perfect either. When the drill tool plunges into the pad stack, it will not hit every pad perfectly in the center. This is not only a normal part of the PCB manufacturing process but has been the standard result for many years.
Many PCB specifications require manufacturers to add filleting to pads prior to the manufacturing process. This does not hurt, but just remember, the practice will not ensure the land will finish with a specified annular ring. If the drill bit hits the pad on the opposite side of the fillet, the annular ring may not finish within specification. In other words, filleting will not save a “bad design” every time.
So, how do we design a board with a particular annular ring requirement in mind? The concept is not difficult, but over the years I have met a few PCB designers who were surprised at the result. This is because the calculation shows they need a much larger land size than they planned for in order to get to the annular ring they have been tasked to lay out. Even worse, the Gerber data has already been finalized, but the holes are going to break out beyond the amount the PCB specification allows.
To ensure there is sufficient annular ring surrounding the hole, we must use the information provided in IPC-2221, Section 9.
Here are the rules:
Where:
a = maximum diameter of finished hole
b = minimum annular ring requirement
C = standard fabrication allowance
This formula seems simple enough, but let’s talk about the finer details that escape us when we are designing under pressure. For the external layers, the maximum diameter of the finished hole should include the top end of the finished hole tolerance. In addition, consider the weight of the copper being drilled through, not the finished copper weight. The calculation for the lands on the internal layers should include the diameter of the drill tool, not the hole size. The drill size is typically 0.004" to 0.006" larger than the finished hole size. This is dependent upon the board finish. With an electroless finish like electroless nickel/immersion gold, 0.004" will suffice.
The minimum annular ring requirement is typically specified in procurement documentation.
The fabrication allowance is also given in IPC-2221, Table 9-1. This table lists three fabrication allowances to use, depending on the capabilities of the PCB manufacturer. I urge you to get in contact with your PCB supplier early in the design process in order to determine which allowance the supplier is capable of producing. If you have been in this industry long enough, you know that not all PCB suppliers are created equal.
There are two other rules from IPC-2221 to consider. These rules consider the copper weight and layer count.
For copper weights greater than one ounce, add 0.00197" to the fabrication allowance. That is, 0.00197" per additional ounce used. When the PCB has more than eight layers add another 0.00197", but not an additional 0.00197" per each additional layer.
Now let us walk through an example of a design that must meet the annular ring requirements of IPC-6012, Class 3. The holes for this design will need a 0.002" annular ring on the external layers, and a 0.001" annular ring on the internal layers. Our hypothetical board is a 10-layer PCB with two-ounce finished copper on each layer. Therefore, we will drill through one-ounce foil on the external layers. Let us assume our PCB supplier can produce a Level B manufacturing allowance, so we can substitute 0.00984" in the manufacturing allowance. We must also add 0.00197" to the manufacturing allowance because the board has more than eight layers. Therefore, our manufacturing allowance will be 0.0118".
For a 0.035" component hole our formula will look like this:
Therefore, the 0.035" component hole, with 0.003" added for the top end of the tolerance, will need a 0.054" land diameter on the external layers in order to achieve a 0.002" finished annular ring. This seems like overkill for a 0.002" annular ring, but considering the board specifications, and the capabilities of PCB manufacturing technology we will have to find a way to work this land size into the design, or compromise on the finished annular ring size.
Ryan Miller is a field applications engineer at NCAB Group.
More Columns from Fresh PCB Concepts
Fresh PCB Concepts: Designing for Success at the Rigid-flex Transition AreaFresh PCB Concepts: More Than Compliance—A Human-centered Sustainability Approach
Fresh PCB Concepts: Assembly Challenges with Micro Components and Standard Solder Mask Practices
Fresh PCB Concepts: The Power of a Lunch & Learn for PCB Professionals
Fresh PCB Concepts: Key Considerations for Reliability, Performance, and Compliance in PCBs
Fresh PCB Concepts: Traceability in PCB Design
Fresh PCB Concepts: Tariffs and the Importance of a Diverse Supply Chain
Fresh PCB Concepts: PCB Stackup Strategies—Minimizing Crosstalk and EMI for Signal Integrity