-
- News
- Books
Featured Books
- pcb007 Magazine
Latest Issues
Current IssueThe Hole Truth: Via Integrity in an HDI World
From the drilled hole to registration across multiple sequential lamination cycles, to the quality of your copper plating, via reliability in an HDI world is becoming an ever-greater challenge. This month we look at “The Hole Truth,” from creating the “perfect” via to how you can assure via quality and reliability, the first time, every time.
In Pursuit of Perfection: Defect Reduction
For bare PCB board fabrication, defect reduction is a critical aspect of a company's bottom line profitability. In this issue, we examine how imaging, etching, and plating processes can provide information and insight into reducing defects and increasing yields.
Voices of the Industry
We take the pulse of the PCB industry by sharing insights from leading fabricators and suppliers in this month's issue. We've gathered their thoughts on the new U.S. administration, spending, the war in Ukraine, and their most pressing needs. It’s an eye-opening and enlightening look behind the curtain.
- Articles
- Columns
- Links
- Media kit
||| MENU - pcb007 Magazine
Estimated reading time: 6 minutes
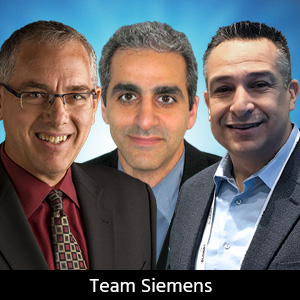
Digital Transformation: Unblocking Innovation With a Component Digital Thread
In our series of digital transformation columns, we’ve hit on several highly relevant topics that electronic systems design companies face today, including a look at supply chain resilience as a challenge and an opportunity and then optimizing multi-domain co-design. This month takes up another important new development: establishing component digital threads. The positive impacts on systems design companies and the electronics ecosystem will be revolutionary.
Note: In this article, “component” and “part” are used interchangeably.
I can remember the days, as a young electrical engineer at a leading mil/aero company, when the source of passive and IC device data for my circuit functional designs was based on the contents of a floor-to-ceiling bookcase filled with data books of production parts from the leading semiconductor suppliers. The vertical search engine of the day was the simple stepstool I used to comfortably read the spines of the data books on the upper shelves. You trusted the data was accurate, especially the DC and AC switching characteristics and physical package specifications.
Still, thankfully, access to electronics part data went digital and has been improving for many years now, so you can go to any number of component distributor or popular industry aggregation websites to accomplish your component research. The represented component supplier data is plentiful, and filtering options make the data easy to search, but given the volume of data, it is too often stale, incomplete, and hard to fully verify. Moreover, when a part is chosen, engineers and teams tasked with product creation must sift through and interpret copious amounts of information presented in static PDF files that differ subtly in format, style, and naming conventions from one supplier to the next. With PDFs in hand and still needing to translate an idea into a product, engineers must expend additional time and effort to create or search-to-acquire all the models (simulation, IBIS, ECAD, mechanical, etc.) needed to get their job done.
I don’t know what all the latest stats say but, honestly, the engineer’s journey is riddled with speed bumps and potholes that lead to wasted, unproductive time. The world may have gone digital with tools for component research, ideation, design, and analysis, and hand-off to manufacturing may have improved greatly, but as Figure 1 depicts, chasms persist in the electronics value chain. Nevertheless, today, somehow, some way, electronics design innovation still happens. Yet there is so much potential to be realized if there was greater digitalization along the systems value chain. The time to achieve that has arrived.
In 2018, JEDEC ratified the JEP30 standard. The website states: “This standard establishes the requirements for exchanging part data between part manufacturers and their customers for electrical and electronic products. This standard applies to all forms of electronic parts.” JEDEC, one of the most widely respected (open) standards bodies for the microelectronics industry, with several hundred member companies (mostly part manufacturers), fired the “shot heard round the world.”1
My intent here is not to do a deep dive into JEDEC2 but it’s important to underscore the milestone that set the stage for the current revolutionary phase of digital transformation within the electronics industry. Why? Because the JEP30 Part Model standard effectively defines the digital twin for an electronic part. That’s a big deal. In short, the part model combines information (related to electrical, physical, thermal, assembly process classification, and more) about a part into an industry-standard-based digital container defined with an XML schema. The part model schema also comprehends standard interfaces and has the flexibility to access specialized models (for example an IBIS model) that can be added to the part model for an applicable device. The standard also extends electrically to support the notion of reference designs associated with the part model of a specific component. So, number one, the JEP30 Part Model is an industry standard, but here’s the game changer: The JEDEC JEP30 Part Model will now be consumable directly by every tool in the product creation lifecycle.
I mentioned the engineer’s journey above and the potholes that lead to wasted time on less productive tasks. These challenges are made even more daunting when overlayed onto the complexity faced by engineers and development organizations given the ever-increasing requirements of each successive generation of electronics product, not to mention the complexity of the underlying components being used. For example, even traditional “analog” components are becoming more “digital”—adding programmability, state machines, and other advanced features that are beyond the capabilities of existing analog design tools. Conquering this complexity quickly is essential to maintain the innovator’s edge. Armed with part model digital twins, innovation is more readily facilitated and extended.
A digital thread is a communications framework that allows a connected data flow and an integrated view of product data throughout its lifecycle—spanning ideation, realization, and utilization. The digital twin is an essential element of the digital thread, connecting the virtual and physical worlds across the value chain of product, production, and performance. As outlined in Figure 2, at every stage of product creation the part model digital twin will deliver derived value directly to the tools used at each step. In action, part models will enable and empower engineers with greater strategic decision capacity at every point in the design process. Their use will streamline the design process by shortening dependencies, because critical information and model content can be derived from the part model. Most importantly, part models powering the design process will improve first-pass success rates because their use will greatly reduce the risks to successful product delivery caused by time delays and human error that accumulate throughout the product creation process. No more searching for model content. No more fixing data integrity errors from a third-party model. No more misinterpreting the numbers in DC and AC switching characteristic tables because it was difficult to decode the naming conventions used by a given component manufacturer.
As the electronics industry continues to embrace the transformation of component data into industry-standard-based digital twins, it will unblock and unleash the innovation process as the connection between OEM and the component ecosystem they rely on goes from handshakes based on PDF files to high-bandwidth, intelligent links composed of digital part model threads.
Component suppliers will play a critical role in this digital transformation because the data sourced in the part model XML files of tomorrow are presently sourced using static PDF files. Many component suppliers are already shifting to part model representations of their parts. Others will follow as more tools are made available to facilitate the transition and validation to the industry standard.
PDFs as a means of exchanging datasheet information aren’t going away, but in the part model era, they will be augmented by datasheets in digital form and interactive application notes that will offer more robust component supplier to end-customer user experiences and connections. As the shift to digital twins of component data accelerates, building in trust is a natural progression. Part models are complete digital representations of parts. You can therefore envision a day when the part model, or different sections of the part model, will assimilate digital signatures to establish the basis for an immutable ledger that will initiate trust throughout the design chain.
The part model era will enable digital transformation that will touch all players in the electronics value chain. This is a big “T” transformation because it will revolutionize the electronics industry; it will accelerate the design process, leading to greater profitability; and it will pave the way for new levels of innovation—so you can unleash the full potential of your engineering team today.
References
- “Concord Hymn,” Ralph Waldo Emerson, 1837.
- Learn more about their work and the JEP30 Part Model standard at jedec.org.
Matthew Walsh is a product marketing manager in the Electronic Board Systems division of Siemens Digital Industries Software.
This column originally appeared in the October 2022 issue of Design007 Magazine.
- Siemens’ 12-part, on-demand webinar series?“Implementing Digital Twin Best Practices?From?Design Through Manufacturing”
- Rountable: RealTime?with...?Siemens and Computrol: Achieving Operational Excellence in Electronics Manufacturing
More Columns from Digital Transformation
Digital Transformation: Leveraging Digital Automation to Accelerate PCB DesignDigital Transformation: Optimizing Co-Design Across Multiple Domains
Digital Transformation: Supply Chain Resilience, Part Two—The Solution
Digital Transformation: Supply Chain Resilience, Part 1—The Supply Chain Problem
Digital Transformation: Enabling a Digital Thread Across IC/Package/PCB Design
Digital Transformation: The Digital Transformation of Advanced Additive Electronics
Digital Transformation: Leveraging Model-Based Engineering to Manage Risk, Part 2
Digital Transformation: Leveraging Model-based Engineering to Manage Risk