-
- News
- Books
Featured Books
- pcb007 Magazine
Latest Issues
Current IssueSales: From Pitch to PO
From the first cold call to finally receiving that first purchase order, the July PCB007 Magazine breaks down some critical parts of the sales stack. To up your sales game, read on!
The Hole Truth: Via Integrity in an HDI World
From the drilled hole to registration across multiple sequential lamination cycles, to the quality of your copper plating, via reliability in an HDI world is becoming an ever-greater challenge. This month we look at “The Hole Truth,” from creating the “perfect” via to how you can assure via quality and reliability, the first time, every time.
In Pursuit of Perfection: Defect Reduction
For bare PCB board fabrication, defect reduction is a critical aspect of a company's bottom line profitability. In this issue, we examine how imaging, etching, and plating processes can provide information and insight into reducing defects and increasing yields.
- Articles
- Columns
- Links
- Media kit
||| MENU - pcb007 Magazine
Estimated reading time: 3 minutes
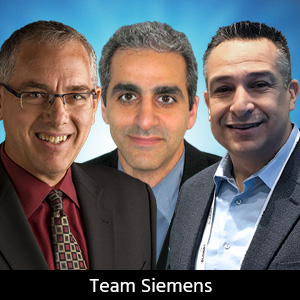
Digital Transformation: Leveraging Model-Based Engineering to Manage Risk, Part 2
In my last column, I highlighted the critical drivers for model-based engineering. I explored the decomposition of system components from the initial requirements (the left side of the V diagram), emphasizing the advantages of maintaining a digital thread during this architectural breakdown across multiple domains. In an earlier column, I addressed the role of the digital prototype in a digital transformation. I’d like to draw those two themes together and talk about the right side of the V (integration and verification).
In traditional flows, system verification is all physical. You test individual units—meaning each PCB by itself, each IC by itself. Once these are verified, you put these components together and move on to subsystem verification to make sure the parts perform correctly with each other. Even at the individual board or IC level, the cost of respins is exorbitant, so waiting until they’re all integrated (including mechanical structures and software) sends the cost and schedule through the roof.
A better approach leverages digital twins to shift verification to earlier in the flow by replacing physical prototypes with digital models. In this process, digital twins, as opposed to physical prototypes, are progressively integrated and verified—from the individual units all the way to the complete system.
Note that there are two ways to leverage digital twins:
- Analysis (often during decomposition and design) to consider trade-offs and optimize a design (ideally automated and leveraging artificial intelligence).
- Verification to ensure compliance against a requirement or derived design rule.
As a design progresses down the left side of the V (from high-level requirements through systems-level architectures to component-level implementations), the digital models increase in fidelity (from very abstract to very realistic). Likewise, as a product progresses from high-level requirements (top left) to system-level validation (top right), the model of the integrated system increases in fidelity.
To ensure errors are found and fixed as soon as possible, verification must be done continuously—from concept to production. The challenge is to leverage the appropriate level of model fidelity at the right time. Just because you have the most accurate model possible doesn’t mean you can do anything with it. For example, simulating every signal on a board is compute-intensive—imagine doing that across a system-of-systems, simultaneously considering multiple disciplines like signal, power, thermal, and structural integrity. While highly abstract models are the only thing that exist in early architecture decomposition, they actually prove more valuable when considering system-level trade-offs across multiple domains at any point in the design process.
Some higher-level requirements can be verified at only the lower levels because they necessitate some white box testing (using detailed models of the inner workings). This makes a bottom-up flow essential, in which you start with the lowest level models and work your way up by merging them together— verify the components, then assemblies, then subsystems, then systems, and even systems-of-systems. The goal is to go up the chain as far as possible.
The power of using digital twins across multiple domains could look like this example. You start with a board-level signal integrity simulation that gives some idea of the EMI radiating from that board. Then you use those results as part of modeling at the subsystem level, where you consider connectors and cablings and such things as the impact of a source harness against a victim harness, or the ability of the enclosure to contain radiation. Then you integrate more elements into that verified subsystem digital model to determine behaviors at the system level, where you’re modeling things like the car, the antenna, and the placement of a motor in order to see how those things might impact 5G communication.
Only by integrating the domains together can we start to address system design challenges. Digital models, from components to systems, are required to connect the domains and enable early design optimization and verification, realizing the dream of a zero-spin design process.
This column originally appeared in the March 2022 issue of Design007 Magazine.
See this additional content from Siemens Digital Industries Software:?
- The Printed Circuit Designer’s Guide to... Stackups: The Design within the Designby Bill Hargin (a free eBook available for download)
- The Printed Circuit Assembler's Guide to ...Smart Data: Using Data to Improve Manufacturing?by Sagi Reuven and Zac Elliott (a free eBook available for download)?
- The Printed Circuit Assembler's Guide to… Advanced Manufacturing in the Digital Age? by Oren Manor (a free eBook available for download)?
- The Printed Circuit Designer’s Guide to… PowerIntegrity by Example by Fadi Deek (a free eBook available for download)
- Siemens’ free, 12-part, on-demand webinar series?“Implementing Digital Twin Best Practices?From?Design Through Manufacturing.”?
- RealTime?With ...?Siemens and Computrol: Achieving Operational Excellence in Electronics Manufacturing?
- You can also view other titles in our full I-007eBook library here
More Columns from Digital Transformation
Digital Transformation: Leveraging Digital Automation to Accelerate PCB DesignDigital Transformation: Unblocking Innovation With a Component Digital Thread
Digital Transformation: Optimizing Co-Design Across Multiple Domains
Digital Transformation: Supply Chain Resilience, Part Two—The Solution
Digital Transformation: Supply Chain Resilience, Part 1—The Supply Chain Problem
Digital Transformation: Enabling a Digital Thread Across IC/Package/PCB Design
Digital Transformation: The Digital Transformation of Advanced Additive Electronics
Digital Transformation: Leveraging Model-based Engineering to Manage Risk