-
- News
- Books
Featured Books
- pcb007 Magazine
Latest Issues
Current IssueThe Hole Truth: Via Integrity in an HDI World
From the drilled hole to registration across multiple sequential lamination cycles, to the quality of your copper plating, via reliability in an HDI world is becoming an ever-greater challenge. This month we look at “The Hole Truth,” from creating the “perfect” via to how you can assure via quality and reliability, the first time, every time.
In Pursuit of Perfection: Defect Reduction
For bare PCB board fabrication, defect reduction is a critical aspect of a company's bottom line profitability. In this issue, we examine how imaging, etching, and plating processes can provide information and insight into reducing defects and increasing yields.
Voices of the Industry
We take the pulse of the PCB industry by sharing insights from leading fabricators and suppliers in this month's issue. We've gathered their thoughts on the new U.S. administration, spending, the war in Ukraine, and their most pressing needs. It’s an eye-opening and enlightening look behind the curtain.
- Articles
- Columns
- Links
- Media kit
||| MENU - pcb007 Magazine
Estimated reading time: 7 minutes
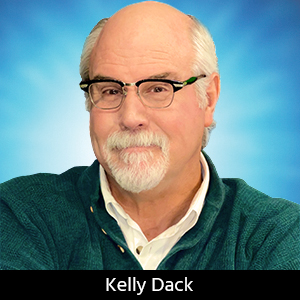
Contact Columnist Form
Target Condition: Scaling PCB Design to the Power of 10
I often reflect on the formative years of my PCB design career when a senior design engineer gave me some sound advice: “Kelly, never design anything that can’t be built.” I think of his words every time I begin laying out a board and while I’m reviewing and performing DFM audits on customer PCB designs which are being transitioned to volume production.
The process of design shapes an idea into a readily producible, physical prototype which can be evaluated for functionality and performance. With regard to “build-ability,” these days, once a prototype materializes, we are challenged differently than when I began designing boards back in the 1980s.
Since then, our manufacturing industry capabilities have scaled seemingly by powers of 10—in macro and micro directions—in their ability to process materials. Capability to process heavy copper onto power circuit substrates in thicknesses greater than 20 ounces is available using advanced print, etch, and electroplating processes. In the micro direction of scale, laser processing has enabled us to shrink many PCB features. Take via processing, for instance. We’ve gone from large, clunky, plated through-holes to elegantly formed HDI (high-density interconnect) microvias. Laser direct imaging (LDI) technology has allowed processing of smaller scale design topology to match the requirements of ever-shrinking electrical parts. More than ever, but not without time and significant investment, PCB manufacturing stakeholders have been able to respond to the requirements put forward by PCB design and engineering stakeholders to shrink process capability if a tangible application and corresponding justification exists.
Telescope Images Got Me Thinking
As many of us gaze upon the images taken recently by the James Webb Space Telescope, there is a great deal of discussion regarding the attributes of scale, definition, and clarity. Some excited scientists point out that these new images let us see much deeper into space than ever before. Other are forming new hypotheses about what the curious images reveal regarding the origins of matter forming each of the galaxies. Most scientists, however, remain apathetic and detached from the images because they don’t reveal much about their areas of subject matter expertise.
To give our readers an idea of the scale these images are missing, I suggest viewing a 1977 short film called “Powers of Ten,”1 produced by Charles and Ray Eames. It does an outstanding job of zooming out, then zooming back into the universe by adding an additional zero to each view, scaling to the power of 10, and helping us to understand the relative size of things. I reference this film often around campfire discussions on metaphysics, the meaning of life, and our place in the universe as PCB designers.
The film starts from an elevation of one meter over a park in Chicago. The first scene depicts a couple enjoying a picnic on a blanket. This view represents the common scale of our “neighborhood” (10 to the 0) at which average folks live and work. In the next scene, we zoom away from the blanket by a power of 10 every 10 seconds. The camera shot begins to zoom out so we can see a 10-meter wide (10 to the 1) square of grass on which the couple’s blanket rests. At 100 meters out (10 to the 2), the couple disappears. The journey continues out to a dark and “lonely scene” at 10 to the 24 meters out—the equivalent span of 100 million light years—until quickly plunging back to the Chicago park to travel in the opposite direction of scale.
As I viewed the images, which were shared in the news and on social media, I must say that I thought they were interesting—to a point. Yes, these images are clearer than those captured years ago by the Hubble Space Telescope (1990), showing light emitted from matter existing millions of light years away. But the image data lacks present, real-time information on the original matter. The data that’s been collected in the images is obsolete by millions of years. I can see how the images are newsworthy and marketable. Publishing the images proving that nebulas and exoplanets existed (past tense) is rocking the scientific world. But for me, new information about distant, million-year-old things are of little value unless I can tangibly understand them and think of a useful application for them. Heck, tiny 01005 chip component packages have been around for only a few short years, and I still have not found a use for them in a PCB design layout due to limited processing capability.
A PCB Concept That Lacks Manufacturing Capability
I know there are PCB designer scientists in the electronics industry working on design standards and ways to present ultra-HDI to our industry stakeholders in a tangible format. I salute them and their efforts to bring these images and potential standards into the view of our PCB design and manufacturing neighborhoods.
But until then, with all the advertising pageantry and displays of low-digit micron trace patterns, I’m afraid some designers will think they can try this out on “normal” design topologies. In fact, I’m currently working on a board in which the designer utilized 15-micron lines to route out of an ultra-fine pitch BGA package. This Hail Mary approach was due to the ongoing effects of our present supply chain crisis. The original design had a much larger processor appropriately matching the PCB topology scale of the layout surroundings. But like a thief in the night, the parts became unavailable and the only procurable parts with similar functionality were packaged within a 143 pin 0.4 mm pitch BGA.
To avoid substantial redesign using conventional HDI via-in-land technology affecting the stackup, the designer chose to route out the inner row connections through the outer row contacts with 15-micron lines. The designer “went all UHDI” without any special processing notes or material specification. Our volume bare board suppliers have “no bid.” I have called three advertised suppliers of “X-SAP” processing, stating that I have money to spend, but I have not received a single call back.
Can UHDI and X-SAP technology help get an EMS stakeholder out of a bind by delivering on this customer design application with delivery requirements of 2,700+ boards per month? Is this layer 1 customer artwork containing 15-micron tracks a viable solution? Can we just add a note which says “Add UHDI processed copper here using supplied artwork?” Should we continue punching down this UHDI path or re-design the entire area of the design to conventional HDI via technology? Which solution will give our customer less sticker shock?
I hope PCB designers will find ways from our contributors to tangibly understand and apply UHDI technology. Will UHDI remain as limited for use as are the tiny 01005 chip packages due to manufacturing capability? Will there be confusion on how to implement UHDI into a PCB which already suffers assembly challenges while processing micro-scaled 0201 chip packages? Designers don’t have to voyage too far into smaller scales of technology before pushing a PCB destined for low-cost, volume production into outer darkness. It is notable that the narrator of “Powers of Ten” makes the point that most of space—galaxies and quarks—are like dust suspended in darkness. (Hey, this sounds like my recent request for an UHDI quote.) The narrator comments, “The richness of our own neighborhood is the exception.”
Is our propensity to focus on the distant macro matter of space or the micro matter of PCBs just a distractive diacatholicon, diverting our attention from the problems and challenges of our present scale? “Our house is on fire,” warn our supply chain managers, quality engineers, and DFM auditors. We’ve got substantial problems to solve within our own neighborhoods in the PCB industry right here on Earth.
I do think the messaging of the “Power of Ten” film somehow transcends into scales of PCB design. We must first and foremost consider the neighborhoods of our PCB industry stakeholders.
As PCB designers creatively zoom out or in, we must avoid venturing into manufacturing darkness. Be thankful for the scientists who go there and bring back applicable data. Let’s help where we can and as project stakeholders, wisely stay in touch, understand, and apply appropriate scales of technology in our industry neighborhoods or we risk losing vision and sense of purpose.
“We are stardust, we are golden, we are billion-year-old carbon, and we’ve got to get ourselves back to the garden.” —Joni Mitchell.
References
- “Powers of Ten,” a 1977 film adapted from Cosmic View, authored by Kees Boeke. The film is available for viewing on YouTube.
This column originally appeared in the October 2022 issue of Design007 Magazine.
More Columns from Target Condition
Target Condition: From Dream House to Drill FilesTarget Condition: Designing vs. Inventing
Target Condition: ‘Boomer to Zoomer: Do You Copy?’
Target Condition: Advanced Packaging Technologies—Look Before You Leap
Target Condition: My Anti-venom to PCB Cost Adders
Target Condition: Taking the Stand at Your Own Design Review
Target Condition: Designing Unconventional Geometries
Target Condition: What the Heck? A PCB Tech Spec Check