-
-
News
News Highlights
- Books
Featured Books
- design007 Magazine
Latest Issues
Current IssueAll About That Route
Most designers favor manual routing, but today's interactive autorouters may be changing designers' minds by allowing users more direct control. In this issue, our expert contributors discuss a variety of manual and autorouting strategies.
Creating the Ideal Data Package
Why is it so difficult to create the ideal data package? Many of these simple errors can be alleviated by paying attention to detail—and knowing what issues to look out for. So, this month, our experts weigh in on the best practices for creating the ideal design data package for your design.
Designing Through the Noise
Our experts discuss the constantly evolving world of RF design, including the many tradeoffs, material considerations, and design tips and techniques that designers and design engineers need to know to succeed in this high-frequency realm.
- Articles
- Columns
- Links
- Media kit
||| MENU - design007 Magazine
Estimated reading time: 9 minutes
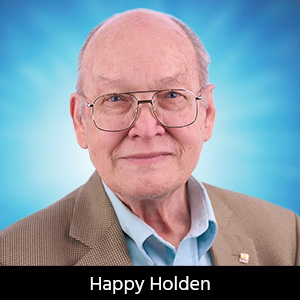
Contact Columnist Form
Happy’s Tech Talk #13: Direct Imaging Revisited
Introduction
It is hard to believe we have had direct imaging for 40 years, starting with Excellon’s introduction of its DIS-2000 argon laser imager. Since then, companies in 11 countries1 have developed various digital direct imagers. Karl Dietz wrote about this technology several times in his columns2, noting early on the skepticism that laser direct imaging would hit a Golden Age. So, where are we now?
Digital Imaging Updates
I-Connect007 has repeatedly reported on and updated digital imaging2. There are several reasons for this extended coverage:
- The technology had a slow, long incubation time that eventually led to accelerated improvement and acceptance for mass production.
- It might also be argued that next to the development of the microvia technologies, digital imaging is probably the most innovative technology to achieve high density interconnects with acceptable yields.
- It is worth mentioning that “direct imaging” is a more appropriate term to refer to this technology than “laser direct imaging” (LDI) because LDI is just one example of digital imaging, albeit its pioneering vision.
The advantages of digital circuitization techniques have been described in detail by suppliers of equipment and photoresist. Since phototool generation and conditioning are omitted, there is the advantage of shorter lead time. Small lots can be customized at no extra cost, as an example, with added date and lot number information. There may be an advantage in fine line imaging of surfaces with poor co-planarity because of the depth of focus of the laser beam. Maybe the biggest advantage is the ability to scale, i.e., to change the dimension of each individual exposure for best fit to reference points on an underlying pattern of a multilayer structure. However, early digital imaging systems had substantial drawbacks, such as Orbotech’s DP100 which used an argon ion laser with limited radiation power, high power usage, and high cooling requirements.
For years, LDI was synonymous with digital imaging. While most early commercially successful digital processes involved the use of lasers, other more recent processes use non-laser light sources such as LEDs (light emitting diodes) that consume less power, last longer, and have a higher light intensity output (Figure 1).
Alternatively, various types of mercury lamps are making use of more than one wavelength. Others use inkjet technology to build image patterns such as legend print, solder mask, or etch resist. They all have in common the building of a pattern, pixel by pixel, and they employ digital “on/off switches” to form the pattern. The switch might be an optical modulator (as in laser direct imaging) or an array of liquid crystal polymer cells (LCPs) that can be rendered translucent or opaque by addressing it with an electrical pulse. The switch might be micro-mirrors on a chip, such as Texas Instruments’ Digital Micromirror Device™ (DMD), whereby tiny mirrors are addressed with an electric pulse so that the mirror is either tilted to direct the light toward the substrate or away from it (Figure 2).
The following is an overview of development and commercial digital imaging systems recently introduced.
Altix-Automata-Tech, the French supplier of imaging systems, first introduced its ADIX-System at productronica 2013. It is based on an advanced high-power LED radiation source (ALDS), a dual multi-wavelength UV-LED, and DMDs. The system is suitable for rigid and flex substrates and has automatic handling options. Earlier systems using DMDs include:
- ORC’s DI-Impact (formerly by Pentax)
- Hitachi’s DE imagers DE-H, DE-S, and DE-F series
- MIVA Technologies GmbH, Germany, Miva 2600X Direct Imager
- Maskless Lithography’s DMD-based system (USA), using a mercury arc light source or LEDs
- Aiscent Technologies (Canada)
The Korean company Ajuhitek, Inc., entered the market with its EP digital imager series using a laser diode radiation source with the wavelength of 405 nm.
To the best of my knowledge, HAN’s Laser Technology Group is the only Chinese supplier of direct imagers.
Japanese direct imager suppliers ADTEC, DNS, ORC, and Via Mechanics continue to introduce improved systems.
The Swiss supplier PrintProcess introduced its Apollon DI-F10 (manual single frontload) and the Apollon-DI-A11 (auto double-side reverse inline). Line width resolution is 30 to 20 microns depending on photoresist type. There are one to seven imaging heads (eight is optional). The light source is UV-LED, with multiple wavelengths in the range of 360 to 420 nm. These units offer automated loading and unloading. It offers automatic image scaling and reliably resolves 1-mil features.
KLEO Halbleitertechnik GmbH, Germany, supplies direct imagers since 2009, with systems in production in Germany and Switzerland. The KLEO-LDI-System CB20HV-Twinstage uses a 405 nm wavelength laser diode. The 405 nm radiation source is dominant in Asia. Photoresists (dry film and liquid) suitable of exposure at 405 nm are available from Hitachi, DuPont, Atotech, Eternal, Kolon, and Elga Europe. KLEO was acquired by Manz in 2015.
The UV-P100 UV-LED direct imager by Limata GmbH (Germany) was developed for prototype and short run production. It can use conventional dry film and solder mask. Light source life exceeds 10,000 hours. Maximum panel size is 650 x 540 mm. Resolution of 50-micron features is obtained. Automated load/unload is available, and side-to-side registration is achieved with cameras and registration target holes.
Orbotech has installed over 1,000 direct imagers. Its Nuvogo DI System is designed for mass production of advanced HDI/flex and rigid flex applications, according to Orbotech. The Nuvogo 800 is compatible with nearly all resist types. Its resolution is capable of 18-micron lines and spaces. Nuvogo makes use of Orbotech’s well established large-scan-optics-technology (LSO). The MultiWave Laser Technology uses a multi-wavelength laser beam of high intensity so that lower cost resist with standard photosensitivity can be used for high throughput (up to 7,000 panels/day/line) with optimal line structure.
Manz, a supplier of wet processing chemistry modules, has diversified into digital imaging with its SpeedLight 2D system. It features a twin stage, allowing imaging of the first panel while a second panel is being registered. The imager consists of 288 laser diode beams that are modulated by nine polygon mirror modules.
Limata GmbH, the German supplier of laser direct imaging systems used in small lot PCB production and photochemical machining, has developed its established UV-P model into the advanced UV-R Series. It can make use of the latest UV diode lasers with multiple wavelengths and a long operating life. Both models are equipped with one to eight laser heads. Resolution down to 25-micron lines and spaces is being achieved. A pre-registration module can address up to 64 registration targets to achieve near perfect registration. Solder mask can be imaged using up to three wavelengths for maximum intensity, to accommodate less sensitive photoresists. A robotic load and unload station can be added for enhanced throughput and optimal interface with other processing equipment.
Canadian supplier Aiscent Technology has done R&D in digital imaging for more than 15 years. Its system uses DMDR-based photolithography and a proprietary high-power laser. Double-sided models currently offered are suitable for production of PCBs, high-resolution photomasks, digital screen imaging, and other customized industrial use.
Schmoll Maschinen, the well-known supplier of mechanical and laser drilling machines, offers a digital direct imaging (DDI) system ideal for prototyping inner layer, outer layer, and solder mask images. It is based on semiconductor laser diodes and large (wide) optics. The imager is equipped with two to eight diode lasers. Schmoll also offers micromirror digital imaging (MDI) systems. The unique “light engine” head is mounted to a granite platform providing a precision positioning system. This new technology transfers UV light images to the circuit board substrate utilizing over 2 million high-resolution micromirror chips. These systems are available as a single-table unit, a tandem table unit, or the XXL model that can handle a maximum single panel size of 1371 x 914 mm. The units use high-power LEDs and DMDR with multiple wavelengths from 365 to 405 nm.
The Swiss company First EIE SA supplies photoplotters, inkjet printers, and direct imagers suitable for quick-turn, small lot size shops. Its direct imager is named EDI500. The light source technology is based on TI’s DMDR devices with advanced UV lens and very high-pressure mercury arc lamps. Panel registration is done with a building CCD camera or by manual pin registration. Maximum panel size is 620 x 690 mm, but the newer EDI700 can handle an even larger panel size.
Visitech is a Norwegian company that supplies optical modules (optical subsystems) for direct imagers. The Luxbeam Rapid System (LRS) is based on TI’s DLPR (micromirrors) and multiwavelength LED light sources, emitting in the range of 350 to 440 nm. Five modules are available with different resolution capabilities: LLS2500 (2.5-micron t/s); LLS04 (4-micron t/s); and LLS06 (6-micron t/s) with two more up to 30-micron t/s. Optical multiplexing allows the units to achieve their very fine resolution.
Front to Back Registration
It is desirable to achieve good front-to-back registration. There are several ways to achieve this, some without the need to drill target holes on the panel before exposure (“hole-less registration”). Figure 3 shows four methods utilizing mechanical and laser drills. The “hole-less registration” is achieved through the “print-out image” characteristic of the photoresist, a color change of the resist during exposure that makes the latent polymerized features visible. For both types of registration, the panel is placed on the machine’s table for topside exposure. As vacuum is applied, the markers placed inside the table start to image the targets or holes on the bottom side of the panel. CCD cameras then align the panel to the table as the panel moves in, and the topside is imaged during the reverse movement. After flipping the panel, CCD cameras locate the target or hole marks on the bottom side; registration and imaging follow.
Another method is shown in Figure 4. First, the recording heads of the DLP Towers are calibrated (step a) and detect any position corrections using the alignment cameras and the registration type (step b), then on fast computers compensation for scaling, rotation, positioning, and enlargement to conduct highly reliable and accurate imaging. Auto-focus follows the board and compensates for warping and board thickness.
Summary
In the application of DI for next generation ultra-HDI, Figure 5 shows the results of the 3 ?m line/space resolution evaluation on larger 510 mm x 515 mm panels. A CCL/ABF substrate with a 10 ?m-thick dry film resist was selected for this demonstration, resulting in lines with just over a 1:3 aspect ratio. Best dose and best focus were determined using a focus exposure matrix (FEM). Best dose was used for the resolution demonstration. The figure indicates that CDs showed less than 10% deviation from -10 ?m to -70 ?m, at a DOF of 60 ?m. The data from the FEM were used to generate a Bossung plot (Figure 5a) in which the X-axis is focus (?m) and the Y-axis is CD (?m). The plot shows the 60 ?m DOF. Figure 5b also includes a lower magnification image of 3 ?m, 3.5 ?m, and 4 ?m isolated and dense line/space arrays. A higher resolution cross-sectional image of 3 ?m lines (Figure 5c) shows dimensions for the middle line: 3.181 ?m line width and 9.873 ?m line height (resist thickness).5
References
- Israel, Germany, Japan, Korea, China, U.S., Switzerland, Canada, Taiwan, UK, and Norway.
- Karl Dietz Tech Talks of November 1997, May 1999, September 1999, August 2002, June 2004, April 2005, April 2007, July 2011, October 2011, November 2012, and November 2015.
- “Laser Technologies for HDI Applications— new structuring and via processing”, D.J. Meier and J. Kickelhain, Proceedings, Electronic Circuits World Convention (9), Oct. 7-9, 2002, Cologne, Germany.
- Karl Dietz, Tech Talk #198, Digital Imaging, Part A, The PCB Magazine, pp. 60–63, October 2012.
- “Fine-resolution lithography enables next-generation panel-level packaging,” by John Large-field Chang, Proceedings of IMAPS Advanced SiP Conference-2022, Hilton Sonoma, California.
Happy Holden has worked in printed circuit technology since 1970 with Hewlett-Packard, NanYa Westwood, Merix, Foxconn, and Gentex. He is currently a contributing technical editor with I-Connect007, and the author of Automation and Advanced Procedures in PCB Fabrication, and 24 Essential Skills for Engineers.
This column originally appeared in the October 2022 issue of PCB007 Magazine.
More Columns from Happy’s Tech Talk
Happy’s Tech Talk #39: PCBs Replace Motor WindingsHappy’s Tech Talk #38: Novel Metallization for UHDI
Happy’s Tech Talk #37: New Ultra HDI Materials
Happy’s Tech Talk #36: The LEGO Principle of Optical Assembly
Happy’s Tech Talk #35: Yields March to Design Rules
Happy’s Tech Talk #34: Producibility and Other Pseudo-metrics
Happy’s Tech Talk #33: Wet Process Management and Control
Happy’s Tech Talk #32: Three Simple Ways to Manage and Control Wet Processes