Custom Made: The Digital Factory Suite
October 31, 2022 | Nolan Johnson, I-Connect007Estimated reading time: 3 minutes
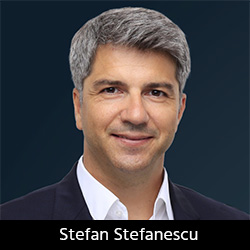
Stefan Stefanescu is head of business development for Atotech’s industrial digital transformation solutions. Here, he discusses how the Digital Factory Suite (DFS) fits into a PCB fabricator’s workflow. The new software connects to the onsite production equipment and continuously collects process and equipment data. But it’s more than that, Stefan says. It’s a way to help customers increase productivity and take steps toward developing a smart factory.
Nolan Johnson: Stefan, would you introduce your role regarding Atotech products?
Stefan Stefanescu: We understand that digitalization plays a key role in the development and evolution of every company. When I was hired in 2019, my initial role was to help identify digitalization opportunities within the company, in both our internal processes and our products. I have focused very intensely on a strategy for industrial digitalization around our equipment, especially printed circuit board manufacturing equipment. Obviously, digitalization is a core enabler, but transformation is not just about a platform or solutions. It’s about processes and people. It’s very complex. Atotech has been responsive and open and that’s why I enjoy working with a company that understands that transformation needs to happen.
Johnson: Atotech, which is now part of MKS, recently announced it is expanding its product offering with a Digital Factory Suite, particularly wet processes. What can you tell me about that?
Stefanescu: For almost 20 years, we have delivered equipment for PCB manufacturing with our control software that allows our customers to operate and run our equipment in production. This enables our customers to run their production as best as possible. Our visualization and control system (VCS) is embedded and delivered when a customer receives our equipment, and the Digital Factory Suite is an add-on, which works with our VCS to bring a suite of values around the equipment.
It helps to see it in steps. I like to start with understanding our motivation, and there are four key areas of focus. First, our products are developed with a customer focus. We see digitalization as a tool to bring this focus to higher levels, reduce friction and response time, and help the customer solve problems faster. Second, we see digitalization and industrial digital solution as a tool to increase productivity and especially help our customers operate their production more smoothly. It also touches on sustainability, an important topic for our customers and the whole ecosystem.
Third, digitalization helps us with our R&D processes to bring products to the market faster. Thus, we have adjusted our procedures and planning. Finally, we look at how our customers are doing production today. Some are already looking at what a smart factory means and how to do it. They have started with basic solutions such as a manufacturing execution system (MES), but much more can be done. We see our solutions as enabling our customers to begin this Smart factory journey. It’s something that needs to be done together with the suppliers of equipment and other solutions and with the customer, because a Smart factory is an ecosystem, not just one system.
Johnson: Stefan, when transition and significant change finally happens in an organization, it’s usually because there was some compelling event. Overall pressures will push you toward change, but finally something seems to force your hand. Is there a theme for what’s triggering PCB fabricators to move to a digital environment?
Stefanescu: Yes, we see that quite a bit. The things that happened due to the pandemic accelerated digitalization. That’s a fact. But to summarize the need for digitalization and the drive from our customer’s side, there are three important factors. First is compliance in the form of traceability and sustainability. There are requirements for reporting, warranties, and having the proper tools to understand how “green” the production is.
To read this entire conversation, which appeared in the October 2022 issue of PCB007 Magazine, click here.
Suggested Items
Siemens, Intel Foundry Advance Collaboration
04/30/2025 | Siemens Digital Industries SoftwareSiemens Digital Industries Software announced that its continued collaboration with Intel Foundry has resulted in multiple product certifications, updated foundry reference flows, and additional technology enablement leveraging the foundry’s leading-edge technologies for next-generation integrated circuits (IC) and advanced packaging.
The Knowledge Base: Unlocking the Invisible—The Critical Role of X-ray Technology
04/29/2025 | Mike Konrad -- Column: The Knowledge BaseFrom detecting voids under BGAs to solder defects in high-reliability applications, X-ray inspection has become an indispensable tool in modern manufacturing. But how is the technology evolving? What challenges do experts face in deploying X-ray inspection effectively and what does the future hold for this critical quality assurance method?
KOKI Expands U.S. Sales Coverage with Multiple New Representatives
04/29/2025 | KOKIKOKI, a global leader in advanced soldering materials and process optimization services, is pleased to announce the expansion of its U.S. sales network with the addition of three new manufacturers’ representative firms: Assembled Product Specialists, Diversitech Reps Inc., and Eagle Electronics.
Machine Vision: MVTec Expands Deep Learning Portfolio with New Versions of its Deep Learning Tool
04/29/2025 | MVTec Software GmbHThe machine vision industry is gaining significant momentum by using deep learning, a subset of artificial intelligence, which allows for the automation of entirely new applications and improved results.
CCL Design, Ynvisible Announce Strategic Partnership to Deliver Scalable Printed Display Solutions
04/28/2025 | CCL DesignCCL Design will integrate Ynvisible's proprietary display technology into its global manufacturing infrastructure and technology portfolio.