-
- News
- Books
Featured Books
- pcb007 Magazine
Latest Issues
Current IssueInventing the Future with SEL
Two years after launching its state-of-the-art PCB facility, SEL shares lessons in vision, execution, and innovation, plus insights from industry icons and technology leaders shaping the future of PCB fabrication.
Sales: From Pitch to PO
From the first cold call to finally receiving that first purchase order, the July PCB007 Magazine breaks down some critical parts of the sales stack. To up your sales game, read on!
The Hole Truth: Via Integrity in an HDI World
From the drilled hole to registration across multiple sequential lamination cycles, to the quality of your copper plating, via reliability in an HDI world is becoming an ever-greater challenge. This month we look at “The Hole Truth,” from creating the “perfect” via to how you can assure via quality and reliability, the first time, every time.
- Articles
- Columns
- Links
- Media kit
||| MENU - pcb007 Magazine
Estimated reading time: 3 minutes
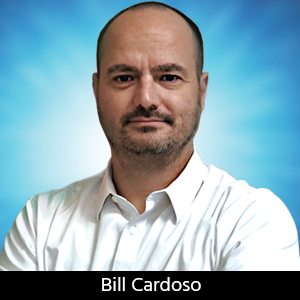
X-Rayted Files: Battery-Powered Advancements Keep on Ticking
Understanding that batteries will power our increasingly electrified future is an important focus for the electronics manufacturing industry. While most manufacturers will simply benefit from an increased demand for additional boards and electronic assemblies, some may choose to migrate into battery production as well. Understanding batteries and how they power so many of the devices we make is crucial to the success of this enterprise.
Of course, the primary driver (get it?) of large-scale battery production, as well as advancements in battery design and chemistry, are automakers, who now produce the largest amount of consumer electronics to date. Tesla took an early lead in battery design before making the jump into manufacturing. In cooperation with Panasonic, Tesla's Gigafactory in Nevada now produces cell-type batteries like the 2170 used in the Tesla Model 3. Ford and GM are also both investing heavily in domestic battery production to develop the pouch-type batteries necessary for their own electric vehicle offerings. Because of some powerful government incentives, much of that battery production for both domestic and foreign automakers is going to happen right here in the United States.
Most of the current battery designs rely on lithium-ion for their basic chemistry. The basics inside a battery assembly include a sheet or sheets of positively charged electrode or anode, and negatively charged electrode or cathode, separated from one another by thin sheets. For cells like the 2170, the sheets are rolled (thus often referred to as “jelly rolls”) and inserted into their metal outer case; electrolyte supports the flow of electrons to the attached terminals. For pouch batteries, the sheets remain flat and are instead inserted into an aluminum-coated plastic pouch. While this process may sound relatively straightforward, there are many challenges to successfully assembling these products.
As a supplier of X-ray inspection equipment, I’m seeing a significant increase in inquiries seeking solutions for quality inspection of batteries, and for good reason. We all remember the dangers associated with battery failures in Samsung phones; such failures would be even more disastrous for significantly larger consumer electronics. As electronics manufacturers, you know that quality and safety standards have always been higher for auto manufacturing than for consumer electronics, and for good reason. That experience uniquely positions the industry to support the manufacture of not only batteries, but all associated electronics.
There’s a wide range of failure modes for lithium-ion batteries. In the early days of Gigafactory, Panasonic was reported to have been scraping as many as half a million defective cells daily to keep pace with demand. Like in board manufacturing, battery production benefits from multiple point inspections during the assembly process. Connectors need to be inspected for weld or solder defects. Both pouches and rolls must validate electrolyte fill levels and absence of dry spots. Rolls need to be evenly wound and free of gaps or delamination. Pouches must be carefully inspected for electrode overhang, especially in corners. Both types must be free of foreign materials and contaminants. Defects that leave the factory can be downright catastrophic, including fires resulting from thermal runaway that can be impossible to extinguish. When done right, though, these and other emerging battery technologies will power an exciting future.
It's not just big players like Tesla, GM, and Ford flexing their muscles in this market; there may be opportunities for smaller EMS providers to make the shift to electric vehicles as well. A cottage industry of sorts is emerging among those converting legacy vehicles to electric, as well as those producing specialty electric vehicles for consumers seeking something different. These low-volume, boutique manufacturers will need the support of nimble and efficient specialty electronics of all types, batteries included.
I’ve been in the electronics industry in one form or another since I was a teen. We’re always on the forefront of technological change—that's what makes this industry both challenging and exciting. If we keep our eyes on the battery technology space, we can appreciate the thrill of yet another new change while also benefiting from the many opportunities it creates.
Dr. Bill Cardoso is CEO of Creative Electron.
More Columns from X-Rayted Files
X-Rayted Files: Best Practices in Buying MachinesX-Rayted Files: ’23 and Me?
X-Rayted Files: What’s Cooler Than X-ray?
X-Rayted Files: My Favorite BGA Assembly Ever, Part 3
X-Rayted Files: My Favorite BGA Assembly Ever, Part 2
X-Rayted Files: My Favorite BGA Assembly Ever
X-Rayted Files: Smart vs. Intelligent SMT Factory
X-Rayted Files: X-ray Everything!