-
- News
- Books
Featured Books
- pcb007 Magazine
Latest Issues
Current IssueInventing the Future with SEL
Two years after launching its state-of-the-art PCB facility, SEL shares lessons in vision, execution, and innovation, plus insights from industry icons and technology leaders shaping the future of PCB fabrication.
Sales: From Pitch to PO
From the first cold call to finally receiving that first purchase order, the July PCB007 Magazine breaks down some critical parts of the sales stack. To up your sales game, read on!
The Hole Truth: Via Integrity in an HDI World
From the drilled hole to registration across multiple sequential lamination cycles, to the quality of your copper plating, via reliability in an HDI world is becoming an ever-greater challenge. This month we look at “The Hole Truth,” from creating the “perfect” via to how you can assure via quality and reliability, the first time, every time.
- Articles
- Columns
- Links
- Media kit
||| MENU - pcb007 Magazine
Estimated reading time: 4 minutes
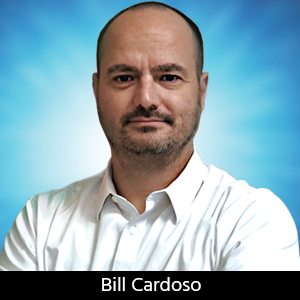
X-Rayted Files: X-ray Everything!
It should be clear by now that my enthusiasm for X-ray knows no bounds. From fighting counterfeits, inventory management, and solder inspection, to quality control for an endless array of manufactured products, the usefulness of X-ray inspection tools is seemingly limitless. So, forgive me for not setting my bias aside, but when it comes to X-ray imaging, you probably fall into one of the following categories:
- You don’t need X-ray and you know it (please, at least read the paragraph that follows)
- You need X-ray but don’t know it
- You have X-ray but are underutilizing it
- You are the rarest of birds who has X-ray but just doesn’t need it
It’s from this admittedly biased vantage point that I have to ask: Why aren’t you X-raying your product?
Some will answer with a definitive “I just don’t need to.”
Of course, it’s true that there are many products for which X-ray inspection can add little value. That said, if you are working on the assumption that your widgets can’t benefit from X-ray validation somewhere in the manufacturing process, I hope that you have reached that conclusion because you have imaged those widgets on a contemporary, high-resolution, real-time imaging system. Quite often, we image samples for a prospective client based on a specific need, and find that there is additional, unanticipated information to be gleaned from getting a peek inside their product. True, you may not need X-ray, but as an imaging enthusiast, I’d encourage you to stay curious. Be open to the possibility that there may, in fact, be something you can learn in the process, and at little or no cost. I can’t think of a single X-ray system manufacturer who doesn’t offer complimentary sample studies.
“Radiation can damage my product.”
There are exceptions, of course, (we wouldn’t want to X-ray photographic film), but for most things, including micro-electronics, there is virtually no way X-ray is going to alter or harm a product during the imaging process. Yes, there are theoretical situations in which X-ray power and exposure time could do potential harm to sensitive materials, but the parameters that could lead to such an outcome are both predictable and easily avoided. Take micro-electronics, for example. All those chips that make our iPhones, pacemakers, laptops, or glucose monitors tick will receive a far greater dose of radiation exposure on a transcontinental airline flight than in a typical industrial inspection system. Keep in mind that most packages are X-rayed by customs and shipping companies at energy levels far superior to the ones inside imaging X-ray systems.
“They are too complicated to use.”
You’re not kidding. Some X-ray inspection equipment is excruciatingly difficult to use, and can require extensive training and dedicated staff to truly utilize. If you’ve had experience on such a system, it could certainly color your view on the usefulness of X-ray equipment, especially in a manufacturing capacity. Fortunately, spurred in part by the move toward Industry 4.0, many X-ray inspection systems are far more user friendly than their predecessors. X-ray machines don’t have to be intimidating, and can be remarkably easy to train on and use. With skilled operators in scarce supply, you may even opt for fully automated systems, operating autonomously with the help of artificial intelligence software. Not only do such tools reduce demands on staff, but they can eliminate human error, and provide instantaneous data about your manufacturing process. Yes, X-ray equipment can be complicated, but it doesn’t have to be.
“X-rays aren’t safe.”
The simple fact is that exposure to high levels of radiation can be dangerous. It is also true that radiation exposure is virtually inescapable, as background radiation from cosmic rays, common building materials, even food, surround us 24/7. Early X-ray system were downright dangerous, especially for their operators, but modern X-ray equipment includes highly effective shielding that prevents radiation from escaping their cabinets. How effective? Quite often, X-ray cabinets will release less radiation than background radiation of the manufacturing environment in which it operates.
“X-ray machines are too big.”
Of course, you’ve seen those X-ray cabinets that are bigger than your entire lab. But just as we no longer have to put up with shoehorning a “brick” of a mobile phone into our jacket pockets, X-ray systems are available in significantly smaller footprints. And like the modern smart phone, their smaller size doesn’t mean downsized capabilities. Even the most space constrained labs can make use of powerful, high-resolution, real-time X-ray inspection tools.
“I can’t afford it.”
Once again, this may be true, but if it’s been a while since you’ve explored X-ray system cost, hold that thought. I’m not going to suggest that X-ray machines have been subject to Moore’s law, but some highly capable systems might surprise you with their relatively short return on investment (ROI). Speaking of ROI, depending on your industry, it may be fair to ask, “Can I afford not to have an X-ray system.” For high-reliability products such as automotive, aerospace, and medical device, letting a single defective part reach consumers can be far more costly than the price of incorporating robust inspection into your manufacturing and quality assurance best practices.
I know, the guy who makes X-ray machines says X-ray everything. But just because it is admittedly self-serving, it doesn’t mean I’m wrong. Stay curious, set aside what you think you know about X-ray machines, and yes, X-ray everything!
Dr. Bill Cardoso is CEO of Creative Electron.
More Columns from X-Rayted Files
X-Rayted Files: Best Practices in Buying MachinesX-Rayted Files: ’23 and Me?
X-Rayted Files: Battery-Powered Advancements Keep on Ticking
X-Rayted Files: What’s Cooler Than X-ray?
X-Rayted Files: My Favorite BGA Assembly Ever, Part 3
X-Rayted Files: My Favorite BGA Assembly Ever, Part 2
X-Rayted Files: My Favorite BGA Assembly Ever
X-Rayted Files: Smart vs. Intelligent SMT Factory