-
- News
- Books
Featured Books
- pcb007 Magazine
Latest Issues
Current IssueInventing the Future with SEL
Two years after launching its state-of-the-art PCB facility, SEL shares lessons in vision, execution, and innovation, plus insights from industry icons and technology leaders shaping the future of PCB fabrication.
Sales: From Pitch to PO
From the first cold call to finally receiving that first purchase order, the July PCB007 Magazine breaks down some critical parts of the sales stack. To up your sales game, read on!
The Hole Truth: Via Integrity in an HDI World
From the drilled hole to registration across multiple sequential lamination cycles, to the quality of your copper plating, via reliability in an HDI world is becoming an ever-greater challenge. This month we look at “The Hole Truth,” from creating the “perfect” via to how you can assure via quality and reliability, the first time, every time.
- Articles
- Columns
- Links
- Media kit
||| MENU - pcb007 Magazine
Estimated reading time: 4 minutes
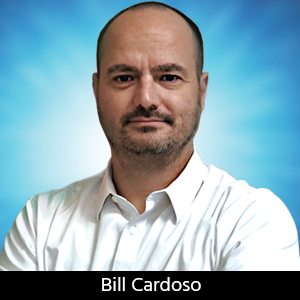
X-Rayted Files: What’s Cooler Than X-ray?
At the most basic level, imaging—whether optical, X-ray, or even computed tomography (CT)—is data collection. Why we gather that data, of course, is to develop useful information about the product we are imaging. When the method of imaging provides the information we need, we have actionable data. When considering whether to employ X-ray imaging vs. CT, there are quite a few considerations, but most important is whether our choice will successfully result in actionable data, providing genuine insight (pun intended) into our product and process.
What’s the Difference?
I’m pretty enthusiastic about “conventional” 2D X-ray. Real-time, high-resolution, digital X-ray can provide an amazing amount of information. Such systems can easily, and nearly instantaneously, generate very detailed images of entire assemblies, or components down to the size of bond wires. But sometimes even the most detailed 2D images can’t tell the whole story. Defects, for example, can sometimes be hidden within multiple layers of dense materials, or even just obscured by objects of similar density. Sometimes this simply can be addressed by inspecting from multiple angles, oblique angle viewing that is often referred to as 2½ D. Because a real-time X-ray system can generate data (images) so rapidly, using fixturing or even a rotation device can suffice to reveal the needed information in relatively short order.
Figure 1: X-ray, optical, and CT of a cast component.
For those of us who embrace all things X-ray, computed tomography is simply next level. CT uses 2D X-ray images, numbering in the hundreds or thousands, produced by rotating the object being imaged (the sample), or the X-ray source and detector, in very small, precise increments. These X-ray images are processed using sophisticated volume-rendering software to produce a 3D representation of the sample being imaged. Because the 3D rendering is produced using X-ray, the rendering includes both external and internal features. Slicing the rendering can reveal internal features, and unlike traditional 2D X-ray images, the features in the region of interest won’t be obscured by other features in the foreground or background. The process takes time (often a lot of time), but the information it yields can be both worth the wait and worth its weight.
When You Need the Data
When to use X-ray vs. CT gets back to the question of data. How much data do we need to provide meaningful, actionable information? CT provides far more raw data than 2D X-ray, and we often see the engineers light up when we share a reconstructed CT image. But I don’t even have to say it for you to know where I’m going; more data isn’t always a good thing. Excess data, that which doesn’t result in actionable insight, is nothing more than noise. But noise is not the only consideration when choosing between these technologies. 2D X-ray inspection systems are relatively inexpensive compared to CT systems. In addition to equipment cost, the time it takes to acquire an image is important in making this call. For high volume inspection, X-ray imaging, even from multiple angles, will likely prove more practical than CT.
Though, for some high-reliability products, CT might be required to ensure the quality desired. If we are, for example, investing in the building and launching of a satellite, the additional investment in implementing CT imaging as part of the quality assurance process likely makes good sense. It would be a shame to get the thing up there only to have it fail because of a poorly attached BGA. Essentially, using CT comes down to weighing cost and possibly inefficiency against the value of the data and information the resulting images provide.
Figure 2: X-Ray image of assembled connector, CT of same connector, and a slice from the CT image.
For Instance
There are a number of important uses of CT, including defect detection, failure analysis, and reverse engineering to name a few, some of which just can’t be accomplished using 2D X-ray analysis. We recently imaged the complex connector in Figure 2. This one is a critical component of an electric vehicle, with dangerous consequence in the case of failure. Electrical connectors can suffer from a number of failure modes including open connections, missed crimps, and improper crimps to name a few. In the 2D image, only a single defect, the open connection, can be clearly identified. With the 3D rendering, all of the defects are revealed including improperly crimped and uncrimped wires. Missing these additional defects could be disastrous if these problems go unaddressed. Our client used CT imaging to test and validate their fabrication process, resulting in consistent and reliable assembly. The CT system remains a valuable tool for failure analysis, product development, and process development.
If X-ray will provide all the data and information you need, then don’t make the mistake of flooding the zone with noise. But if X-ray alone is leaving gaps in your understanding, then the additional detail that computed tomography can provide, may prove invaluable. Again, data is only valuable to the degree that it results in actionable information.
Dr. Bill Cardoso is CEO of Creative Electron.
More Columns from X-Rayted Files
X-Rayted Files: Best Practices in Buying MachinesX-Rayted Files: ’23 and Me?
X-Rayted Files: Battery-Powered Advancements Keep on Ticking
X-Rayted Files: My Favorite BGA Assembly Ever, Part 3
X-Rayted Files: My Favorite BGA Assembly Ever, Part 2
X-Rayted Files: My Favorite BGA Assembly Ever
X-Rayted Files: Smart vs. Intelligent SMT Factory
X-Rayted Files: X-ray Everything!