OE-A at LOPEC – Printed Electronics Up Close
February 7, 2023 | OE-AEstimated reading time: 2 minutes
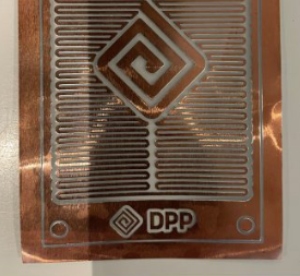
Smart skis that “feel” the vibrations of a downhill run, a flying 3 D printed drone, a sensing glove, a biosensor test kit that helps to avoid virus spreading and some more inspiring ideas play a major role in this year’s “OE-A Competition”. This yearly competition run by the OE-A, part of VDMA, fosters and challenges engineers and designers to present their printed electronics innovations to the world. At LOPEC 2023, the leading international exhibition and conference of printed electronics, from February 28 to March 02 at ICM, Messe München, all projects are showcased at the OE-A booth.
Mega trends Mobility and Smart Living
“For me personally the best thing about the competition is the exciting mix between inspiring, trendsetting ideas and market ready products. This year’s submissions are very much in line with the Focus Topics of LOPEC, we have great projects in the field of mobility and smart living. And we see that sustainability is even in early-stage projects a leading idea.” says Dr. Klaus Hecker, Managing Director of the OE-A, an international working group within VDMA.
This year 16 contributions from international companies, research institutions and universities take part in the “OE-A Competition 2023” to present their new products, prototypes, and concepts. The submitted projects are judged by a jury of representatives from well-known international companies and institutes in three categories: “Prototypes & New Products”; “Freestyle Demonstrator”; and “Publicly Funded Project Demonstrator”.
When Clever meets Smart
“The expert jury will have a hard time rating the 16 contributions and deciding on the winners of the three categories”, predicts Klaus Hecker. Here is a first snapshot of competition contributions which will be shown at the OE-A booth:
Smooth & Sharp from Taiwan submitted a printed NFC biosensor test stripe for disease screening. The test stripe decreases the risk of virus spreading triggered through testing and transportation because it shows the result straight away. The contaminated patch can be removed safely and is easy to dispose.
How to create an eco-friendly, ultra- thin and flexible heating foil based on a copper skin film shows Avery Dennison. This novel technology enables a more sustainable production of heating and sensor foils for the mobility and healthcare sector.
The Smart skis submitted by Joanneum Research and partners sensors vibrations while skiing. The energy autonomous sensor transmits data about the behavior of the ski on different slopes, material stability and the suitability of the ski for the athlete.
Who is going to win?
Not only the jury will decide which project is a winner, – but all visitors are invited to cast their vote for the “Public Choice Award”. Visitors choose from all contributions which demonstrator deserves the “Public Choice Award”. The voting takes place March 01st at the OE-A booth and the winner will be announced on the evening of Wednesday, March 01nd during the LOPEC Get-together & Award Show. Additionally, the winner of all categories will present their demonstrators at a web seminar in April 2023.
New edition of OE-A Roadmap
More than 100 experts have contributed to the new OE-A Roadmap. The OE-A Roadmap offers end-users, developers and funding bodies alike a deep insight into the technology and applications. “Next to the inspiring demos of the competition, a visit at the OE-A booth is also worthwhile to get your copy of the newly published OE-A Roadmap. For our members is this comprehensive guide of printed electronics complimentary. For non-members we offer an executive summary right at the booth. In case you cannot make it to LOPEC, summary and whitepaper will be for download at oe-a.org right after LOPEC” adds Klaus Hecker.
Suggested Items
I-Connect007 Editor’s Choice: Five Must-Reads for the Week
07/18/2025 | Nolan Johnson, I-Connect007It may be the middle of the summer, but the news doesn’t quit, and there’s plenty to talk about this week, whether you’re talking technical or on a global scale. When I have to choose six items instead of my regular five, you know it’s good. I start by highlighting my interview with Martyn Gaudion on his latest book, share some concerning tariff news, follow that up with some promising (and not-so-promising) investments, and feature a paper from last January’s inaugural Pan-European Design Conference.
Elephantech Launches World’s Smallest-Class Copper Nanofiller
07/17/2025 | ElephantechJapanese deep-tech startup Elephantech has launched its cutting-edge 15 nm class copper nanofiller – the smallest class available globally. This breakthrough makes Elephantech one of the first companies in the world to provide such advanced material for commercial use.
Copper Price Surge Raises Alarms for Electronics
07/15/2025 | Global Electronics Association Advocacy and Government Relations TeamThe copper market is experiencing major turbulence in the wake of U.S. President Donald Trump’s announcement of a 50% tariff on imported copper effective Aug. 1. Recent news reports, including from the New York Times, sent U.S. copper futures soaring to record highs, climbing nearly 13% in a single day as manufacturers braced for supply shocks and surging costs.
I-Connect007 Editor’s Choice: Five Must-Reads for the Week
07/11/2025 | Andy Shaughnessy, Design007 MagazineThis week, we have quite a variety of news items and articles for you. News continues to stream out of Washington, D.C., with tariffs rearing their controversial head again. Because these tariffs are targeted at overseas copper manufacturers, this news has a direct effect on our industry.I-Connect007 Editor’s Choice: Five Must-Reads for the Week
Digital Twin Concept in Copper Electroplating Process Performance
07/11/2025 | Aga Franczak, Robrecht Belis, Elsyca N.V.PCB manufacturing involves transforming a design into a physical board while meeting specific requirements. Understanding these design specifications is crucial, as they directly impact the PCB's fabrication process, performance, and yield rate. One key design specification is copper thieving—the addition of “dummy” pads across the surface that are plated along with the features designed on the outer layers. The purpose of the process is to provide a uniform distribution of copper across the outer layers to make the plating current density and plating in the holes more uniform.