-
- News
- Books
Featured Books
- smt007 Magazine
Latest Issues
Current IssueMoving Forward With Confidence
In this issue, we focus on sales and quoting, workforce training, new IPC leadership in the U.S. and Canada, the effects of tariffs, CFX standards, and much more—all designed to provide perspective as you move through the cloud bank of today's shifting economic market.
Intelligent Test and Inspection
Are you ready to explore the cutting-edge advancements shaping the electronics manufacturing industry? The May 2025 issue of SMT007 Magazine is packed with insights, innovations, and expert perspectives that you won’t want to miss.
Do You Have X-ray Vision?
Has X-ray’s time finally come in electronics manufacturing? Join us in this issue of SMT007 Magazine, where we answer this question and others to bring more efficiency to your bottom line.
- Articles
- Columns
- Links
- Media kit
||| MENU - smt007 Magazine
Estimated reading time: 6 minutes
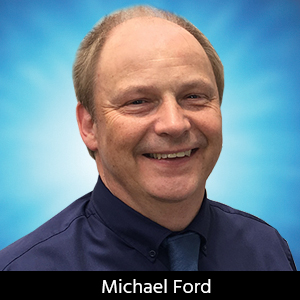
Smart Factory Insights: Manufacturing Meets the Flintstones
As a kid, I loved “The Flintstones” cartoon series. Recently, I watched some of the old shows and as I listened to the dialogue, I saw how our social landscape has changed significantly, except for one character, “Bamm-Bamm Rubble.”
Pounding things with a club, like Bamm-Bamm, appears to be the enduring default approach of our sustainability and recycling industries, yet I believe a business opportunity exists in the form of reverse manufacturing where EMS companies and others can potentially double the scale of their activities and value in an area that appears to be locked into the Stone Age.
A very significant example is the recycling of car batteries from modern electric vehicles. I was amazed to discover that these are currently shredded in the same way we would shred limbs of overgrown trees in our gardens to make sawdust. The whole battery pack is simply put into a massive shredder. When cells are not completely or properly discharged, there are frequent fires and explosions. Following this, only about 30% of the core minerals and materials can be recovered through a series of vibrators and sieves; further recovery is possible from the “black dust” that remains. It requires special processing and is often done overseas.
Personally, and perhaps naively, I thought we had progressed a little bit since “The Flintstones.” For probably one of the most significant new products and technologies of our age, it seems we would have figured out from the start how to make the recycling end of this business sustainable, especially considering the rarity and difficulty to source these materials, as well as the cost and pollution caused by these basic recycling methods. There is then the volume to consider. Right now, such batteries need recycling only in the event of a battery failure or damage to a car in an accident. In perhaps a decade or so, we will be well on the ramp-up curve, as all of today’s electric cars reach their end of life. Other immediate examples of “Flintstones” recycling include the recovery of rare-earth magnets from products such as mechanical hard disks and speakers, where the part of the product containing the magnets is simply cut off—and Bamm-Bamm is called in.
In the case of electronic products, we have started to disassemble the products rather than just crushing them. Governments have created legislation to reduce electronic waste in landfills, such that discrete products made up of sub-assemblies, key components, and hazardous materials can be separated out by reverse assembly, then reused, recovered, or recycled. There are new technologies on the horizon to replace the PCB base FR-4 material, such that when everything has been removed, we are left with something that can actually be recycled.
The “circular economy” is often thought about in terms of the recoverability of materials which can be reused in manufacturing, but this focus is too narrow. Success will remain elusive if we continue with the way things are, as the cost of material recovery is simply not yet a viable business model in most cases. The flaw in the plan is expecting that one day the recycling business model will become realistic if it relies on materials becoming rarer and, hence, more expensive to justify the cost of recycling. By then, as most materials will have been wasted and lost, it will be too late for recycling to scale to the level needed to replace raw material availability. Therefore, the focus needs to be on creating a sustainable recycling business plan now, reducing the cost, and increasing the yield of current recycling strategies.
Car batteries are based on relatively new and evolving technologies. The focus of their design is on operational and cost performance, as well as physical attributes that make up the design of the car itself. Little or no effort appears to be made on design for recycling. One reason is that there are no common guidelines in the design and manufacturing process; everyone is doing it for themselves. There are, however, some very simple things that can be done. Knowing where key bolts are located, using standard symbols or RFID technology, for example, can reduce the manual labor for disassembly significantly, allowing disassembly by robot automation.
Today we are needlessly investing in projects that try to reverse engineer these bolts, using AI-driven vision processing, size, and torque estimations that will never become commercially viable. Instead, we need to take the simple steps to standardize, or at least document, the way things are made and should be disassembled. Another challenge is the glue used to seal the battery cells within the housing. This glue is intentionally extremely difficult to penetrate, but could be replaced with a glue that dissolves, for example, when subjected to a high concentration of hydrogen. These ideas do not limit or compromise functionality or performance, but hugely impact the ability to disassemble and recycle more efficiently. With the right approach, the circular economy is not just about material recovery, but includes the element of design for recycling.
There is, however, a significant and fundamental difference between manufacturing and recycling. Manufacturing is commercially viable due to its scale, even when considering the increasing variability of products and shortened factory-to-customer lead times. There is a full set of documentation based on the CAD design data with which to manufacture products. Manufacturing engineering, featuring the automated creation of product-specific work instructions, as well as program data for automated processes, should now be completely automated for most manufacturing companies. Manufacturing is, therefore, a known, continuous, efficient, and repeated process.
In the recycling industry, by contrast, products become end-of-life randomly. Almost every unit presented for processing is completely different from the one before. There is no provision for access to any of the details of assembly or disassembly methods, or of the material content—including embedded chemicals, and locations of key materials and components—all of which are key elements needed from the design and manufacturing data. As we have seen with the massive increase in software automation for MES in recent years, we are now on the precipice of “RES,” meaning recycling execution, rather than manufacturing. This is simply MES in reverse gear. Examples already exist in the best MES tools available today, which include RMA/MRO processing, where products from the field are repaired, overhauled, upgraded, or remanufactured into other products. While this is currently happening only at the high end of the market, there are lessons to be learned by the industry.
Due to the random nature of recycling, and with the need for product data from many OEMs to be available to recycling companies, there is an element of security and risk of IP leakage. However, hardware and software technologies exist that uniquely identify products, and allow access to only the needed data of their design and manufacturing in a way that does not reveal intellectual property and other private information. These technologies are being utilized and developed for the supply-network applications supporting manufacturing, but really, the greatest need will be in the recycling industry, which should be included in such projects. After all, materials and elements from recycling are then intended to go back into the supply network.
Revolutions in recycling do not happen overnight, but we all need to be headed in the same, logical direction, rather than just hoping that Bamm-Bamm will continue to be the answer. Let’s hope that, instead, MES technology for disassembly will become as important as for manufacturing. It will include automation with Smart hardware and software and create many new high-skill jobs with built-in security and trust, building the future we imagine not only for future generations, but in knowing that we are making the world better. Before it’s too late.
This column originally appeared in the April 2023 issue of SMT007 Magazine.
More Columns from Smart Factory Insights
Smart Factory Insights: Making Rework a Smart Business OpportunitySmart Factory Insights: The Sustainability Gold Rush
Smart Factory Insights: Today’s Manufacturing Jobs Require a New Skill Set
Smart Factory Insights: Compose Yourself, Mr. Ford
Smart Factory Insights: The Smart Business Case for Local PCB Manufacturing
Smart Factory Insights: Manufacturing Digital Twin—Spanners in the Works
Smart Factory Insights: Machines, People, and AI
Smart Factory Insights: Is Sustainability in Manufacturing a Benefit or Burden?