-
- News
- Books
Featured Books
- smt007 Magazine
Latest Issues
Current IssueSpotlight on India
We invite you on a virtual tour of India’s thriving ecosystem, guided by the Global Electronics Association’s India office staff, who share their insights into the region’s growth and opportunities.
Supply Chain Strategies
A successful brand is built on strong customer relationships—anchored by a well-orchestrated supply chain at its core. This month, we look at how managing your supply chain directly influences customer perception.
What's Your Sweet Spot?
Are you in a niche that’s growing or shrinking? Is it time to reassess and refocus? We spotlight companies thriving by redefining or reinforcing their niche. What are their insights?
- Articles
- Columns
- Links
- Media kit
||| MENU - smt007 Magazine
Estimated reading time: 4 minutes
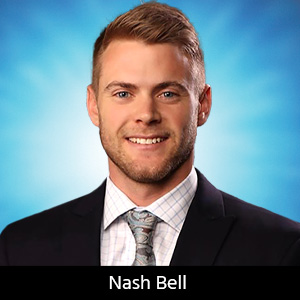
Knocking Down the Bone Pile: Package on Package Rework—Skill Required
Editor’s Note: Though this may be Bob Wettermann’s last installment of Knocking Down the Bone Pile, Bob’s column will carry on under the expert guidance of the subject matter experts at BEST.
Package-on-package (PoP) is an electronic component-stacked package type consisting of vertically stacked ball grid arrays most commonly in a two-high stack. The package closest to the board is the logic/CPU component and is more commonly known as the “bottom” package. The “top” package sits on top of this module and is the memory module. These packages are generally found in consumer electronics (mobile devices) such as smartphones, tablets, and netbooks. These packages tend to be high IO count, fine pitch, very thin packages.
The rework and subsequent inspection of such components requires precise control of temperature as well as skilled repair and rework technicians and a broad understanding of a variety of materials that will be of assistance in reworking PoPs.
There are numerous challenges to reworking these components, including but not limited to the following:
- Due to the thin sizes of the packages (they have to fit into a slender consumer package in most cases), the thermal stresses of the reflow cycle can cause warping of the packages. This can lead to opens and shorts post-rework.
- Many of these consumer devices are underfilled in order to prevent solder joints from cracking, as the handheld devices are prone to the mechanical shock of being dropped. The removal of such packages using a heat source causes the solder to be pushed around, creating soldering anomalies such as shorts.
- Inspecting the multilayer-stacked packages means that more advanced X-ray systems and more experienced operators are required for inspecting the packages post-rework.
- The thin packages mean the packages have high MSL (moisture sensitivity levels), which requires a high degree of care.
- Many of these packages are underneath or near RF shields, which in and of themselves are challenging to remove and replace without damaging underside or neighboring components. Many times the proximity of underfill or components to the shield wall can cause challenges of neighboring components being negatively impacted during the rework process.
The BGA rework equipment needs to be properly adjusted in order to maintain the proper profile when reworking these stacked packages. If the top package to be singled out is to be removed and replaced, then the rework system must have the ability to precisely control the hot air time-temperature profile in order to reduce the possibility of package warpage. These PoP-capable rework systems need to have a zero force or near zero force removal capability in order to not disturb the lower package if the upper package is the one requiring reflow. Since many of these component packages are small, the optical split vision system—along with the BGA placement system—must be able to precisely place the component. In addition, the BGA rework system should be equipped with a non-contact scavenging system for more consistent results in terms of site preparation. In the case of underfilled components, the low or no heat “cold” removal machines—which could be lasers or milling machines—will be key to a successful rework program. Furthermore, the X-ray inspection used to check the rework should have the ability for isometric viewing. This allows the rework technician to inspect the PoP and “see” each of the balls on the individual layers. These are some of the critical rework tools for reworking on PoP packages.
Not only does the equipment need to be capable of reworking stacked packages, but the right experienced engineering and technician support needs to be available. Experience in the nuances of time-temperature profile development, along with the experience of using the right paste fluxes or dipping solder pastes, is part of getting to a robust rework process for the PoPs. The technicians need to be experienced in mitigating the effects of component warpage caused by the heating during placement and removal. Furthermore, the rework process technicians should be very disciplined in properly handling the components given higher than normal MSLs. One of the other decisions that needs to be made in the complete rework process is PoP testing. Experience will help guide the functional testing and whether the PoP should be tested prior to being placed or be tested in-circuit to confirm functionality.
In addition to the right equipment set and the right operator experience, the rework supplier must have a deep understanding of a variety of different materials for PoP rework. In many cases, “dippable” solder paste is used for the individual package rework in order to ensure more consistent solder paste deposit volume, which widens the process window. There are a variety of fluxes which can be used to make sure that longer rework cycles do not cause the activity level of the fluxes to expire. In some cases, specialty chemicals are required for removal of the underfill materials. Experience in their usage and disposal is important. Finally, the right saponifiers for cleaning underneath and in between the various layers is important for removal of the flux residues. In some cases, the bottom component is temporarily glued to the PCB so as to not have the component shift during reflow cycles. This requires experience with different electronic grade glues.
PoP rework requires the right rework experience in terms of process engineering, the right equipment set to develop a repeatable process with the widest possible operating window, and knowledge of a broad set of materials.
Note: This is my last column on PCB rework and repair. I am fortunate to be moving on to Life 3.0—helping others—and no longer be developing PCB rework/repair processes and products or writing about the same. Thank you to all the readers who have been alongside me in this journey.
This column originally appeared in the April 2023 issue of SMT007 Magazine.
More Columns from Knocking Down the Bone Pile
Knocking Down the Bone Pile: Addressing End-of-life Component Solderability Issues, Part 4Knocking Down the Bone Pile: Tin Whisker Mitigation in Aerospace Applications, Part 3
Knocking Down the Bone Pile: Gold Mitigation for Class 2 Electronics
Knocking Down the Bone Pile: Basics of Component Lead Tinning
Knocking Down the Bone Pile: 2023’s Top Challenges in BGA Rework
Knocking Down the Bone Pile: Eliminating Solder Balls in Hand Soldering
Knocking Down the Bone Pile: Opening a Trace on the Surface of a PCB
Knocking Down the Bone Pile: Soldering for QFPs and Other Gull Wing Leaded Parts