-
- News
- Books
Featured Books
- smt007 Magazine
Latest Issues
Current IssueSupply Chain Strategies
A successful brand is built on strong customer relationships—anchored by a well-orchestrated supply chain at its core. This month, we look at how managing your supply chain directly influences customer perception.
What's Your Sweet Spot?
Are you in a niche that’s growing or shrinking? Is it time to reassess and refocus? We spotlight companies thriving by redefining or reinforcing their niche. What are their insights?
Moving Forward With Confidence
In this issue, we focus on sales and quoting, workforce training, new IPC leadership in the U.S. and Canada, the effects of tariffs, CFX standards, and much more—all designed to provide perspective as you move through the cloud bank of today's shifting economic market.
- Articles
- Columns
- Links
- Media kit
||| MENU - smt007 Magazine
Estimated reading time: 7 minutes
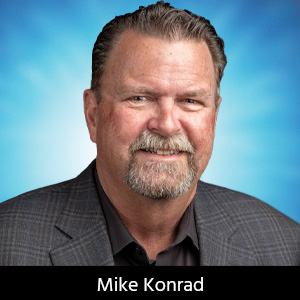
The Knowledge Base: Data Collection and Analysis
This month, I am speaking with Ryan Gamble, CEO and founder of Intraratio, about the collection and analysis of big data. What are the common misconceptions, does artificial intelligence play a role, and what are some of the biggest mistakes for assembly companies when it comes to big data collection?
Historically, the collection of data was associated with a high price due to the cost of early memory chips. Technology has advanced to the point where memory is cheap, and most assembly process equipment can collect data. Now that we can collect large volumes of data (so-called “big data”), how can we make that data useful?
Ryan Gamble: Early in my career I recall analyzing test data in a binary file format called STDF, and wondering why on earth you would painfully use 4 bits to represent a complex test result. Turns out this file format was created back in 1984, and it was a genius way of compressing data because of the high costs of memory at the time.
With data now flowing freely from test and assembly equipment, it’s not unusual to see gigabyte files generated just from a single test operation. The huge challenge now is that this data has no context in terms of correlating to any other equipment in the line, let alone inventory supplier data and other things critical to driving reliability, quality, and cost improvements.
Exacerbating this are machine vendors themselves that are selling data collection and analytics tools that only address their specific operations—disconnected islands of data perpetuating the need for engineers to waste valuable time manually aggregating it into ad hoc spreadsheet tools. At least 80% of engineering time is wasted on manually aggregating and cleaning up data1. Think about what this 80% is costing you in pure dollars, time to market, and more.
The solution is to implement a modern traceability software system that automatically catalogs and contextualizes data from every test and assembly operation across the entire line. Interpreting and storing data from all the different formats and protocols is a complex undertaking, and so best suited for modern software built on web-scale technologies. This breed of software can be configured to be format and protocol agnostic, able to capture all requisite data from all machines, whether it’s file or network HTTP/HTTPS data interchange. It will catalog and contextualize it in real time for immediate data-driven insights.
Don’t get locked into machine vendor specific data collection solutions—they are just another data silo. Above all, avoid legacy solutions providers; they are still sitting atop software written decades ago, based on older approaches to manufacturing that result in costly customizations, technical debt, and the inability to scale without more costly upgrades.
Modern solutions using web scale technologies are the future because they require lower support costs, plug-and-play type data connectivity via APIs (application programming interfaces), and enable enterprises to be nimble and adaptable amidst the growing complexity of today’s supply chain markets.
What are the common misconceptions with data collection and data management?
Gamble: The first misconception is that it’s complicated and costly, therefore only accessible by large corporations who can afford to spend hundreds of thousands of dollars on the endeavor.
Data collection and an effective data management system are a fairly straightforward and cost-effective endeavor to take on. You just need to roll up your sleeves and audit the data collected at every step and every machine in your factory line. Look at where the gaps are against the overall production traceability requirements, so that you have a full picture of the needs. Now you’ll be armed to find the right data collection and traceability software solution.
The second misconception is that you should start small, such as with only one machine cell, and that this will somehow translate and scale to the rest of the factory line.
The biggest (and often the costliest) misconception is thinking your ERP can somehow be made to double as the factory data collection and traceability system. Not even a Netsuite Oracle system out of the box can do serialized traceability, let alone track the 30+ process steps of an SMT production line.
ERP is based on a general ledger architecture, not a factory data collection and management architecture. Bring in a system such as an MES (manufacturing execution system) to provide you with true factory line level visibility and control, with output data reporting that drives better accuracy of your ERP.
With all the buzz surrounding ChatGPT and other online AI-based technologies, how has AI made its way into data analysis and how does that improve the customer experience?
Gamble: Applications such as ChatGPT don’t have direct application to manufacturing. These types of tools are just high-powered chatbots at the end of the day, creating responses to questions based on massive amounts of text content from the web, statistically aggregated to be the most probable response to provide.
Obviously, they will not be able to solve a solder printing process issue or help with that 0.5% yield improvement that is a function of all process settings going back to the semiconductor chips on the PCBA.
However, the underlying technology (a subcategory of AI called machine learning), is a game changer for the electronics industry. Today, anyone with a strong engineering background, coupled with good scripting/programming skills using Python, can implement a machine learning algorithm to hunt for patterns in data. These algorithms can be used for outlier detection, which is incredibly useful for catching quality and process issues in the line, as well as predictive machine maintenance.
Machine learning algorithms can also be leveraged to do virtual product testing based on process data measurements from earlier in the line, thus removing the need to do 100% testing of products going out to customers. The quality, throughput, and overall margin improvements are incredible. But you need well-cataloged contextual data to do this. Otherwise, your engineers will spend most of their time aggregating and cleaning data, and you’ll get nowhere.
Based on your experience, what are the biggest mistakes made when collecting or analyzing data?
Gamble: The biggest mistake I see is not embedding basic traceability attributes in the data at the point it’s generated—for example, part number, test program or machine recipe, lot number or board serial number, and date+time of execution should be there as a minimum.
The idiocy is that many common data standards don’t specify these fields as required. Just look at the SEMI E142 specification, for example. Machine vendors and third-party data software providers are notorious for violating standards because these standards are inherently overly complicated.
Often, engineers try to get around this by embedding information in the file name. But file names get overwritten, and even worse, have you tried to generate analytics by reading in file names?
With today’s access to scripting languages, such as Python, which is open source and free, coupled with simple modern web/network APIs (application programming interfaces) approaches, this information can be injected into the data as it’s being generated. All you need is an API accessible source of routing information, such as an MES, and you’ve got it solved.
Where do you see the future of your industry in general, and data analysis specifically?
Gamble: It’s an exciting time for the electronics manufacturing industry, with engineering becoming more and more data centric. With improving data collection and management, the ability to automate manufacturing lines becomes more attainable, from automated inventory control and dispatching of automated guided vehicles on the factory floor, to advanced outlier detection and improved quality control.
With increased data utilization, there is opportunity for tremendous job growth. I have seen companies grow over four times within the first two years of implementing a modern MES because it frees up engineers to focus on the technical things needed to improve the line, while enabling operators to take on more complex and higher value tasks. All this leads to better product, faster time to market, greater margins, and growth.
Data collection and analytics are key to navigating today’s supply chain challenges and market demands. With the ever-increasing electronics complexity of products manufactured today, it is now a requirement for maintaining a competitive edge.
Today’s engineers are coming out of college with basic programming and data analytics skills. It’s an exciting time with so many new paths to be taken on this technical journey.
Reference
“Cleaning Big Data: Most Time-Consuming, Least Enjoyable Data Science Task, Survey Says,” by Gil Press, Forbes.com, March 23, 2016.
This column originally appeared in the June 2023 issue of SMT007 Magazine.
More Columns from The Knowledge Base
The Knowledge Base: Cultivating Your Brand in the Age of ConnectionThe Knowledge Base: A Conference for Cleaning and Coating of Mission-critical Electronics
The Knowledge Base: Building the Workforce of Tomorrow With EMAC
The Knowledge Base: Beyond the Badge—Why Membership Matters More Than Ever
The Knowledge Base: Unlocking the Invisible—The Critical Role of X-ray Technology
The Knowledge Base: At the Forefront of Electronics Manufacturing
The Knowledge Base: Challenges and Considerations of Harsh Environments
The Knowledge Base: My 2025 Industry Wish List