-
- News
- Books
Featured Books
- pcb007 Magazine
Latest Issues
Current IssueThe Hole Truth: Via Integrity in an HDI World
From the drilled hole to registration across multiple sequential lamination cycles, to the quality of your copper plating, via reliability in an HDI world is becoming an ever-greater challenge. This month we look at “The Hole Truth,” from creating the “perfect” via to how you can assure via quality and reliability, the first time, every time.
In Pursuit of Perfection: Defect Reduction
For bare PCB board fabrication, defect reduction is a critical aspect of a company's bottom line profitability. In this issue, we examine how imaging, etching, and plating processes can provide information and insight into reducing defects and increasing yields.
Voices of the Industry
We take the pulse of the PCB industry by sharing insights from leading fabricators and suppliers in this month's issue. We've gathered their thoughts on the new U.S. administration, spending, the war in Ukraine, and their most pressing needs. It’s an eye-opening and enlightening look behind the curtain.
- Articles
- Columns
- Links
- Media kit
||| MENU - pcb007 Magazine
Estimated reading time: 8 minutes
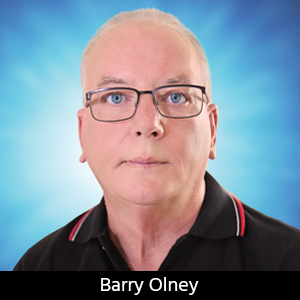
Beyond Design: Balancing Trade-offs for Optimal PCB Design
The field of PCB design is evolving rapidly, which creates both opportunities and demands for new and experienced designers. PCB designers must deal with various issues in finding the right balance between the form factor, functionality, and power requirements of their boards while ensuring that the stackup, placement, and routing are completed to guarantee stringent signal and power quality. Advanced tools and skills are needed to create compact, flexible, high-performance, and low-power PCBs with faster turnaround times. There is also a trend to collaborate with other designers and manufacturers in a team environment through cloud-based platforms to ensure that the designs are reliable and manufacturable.
As multilayer PCBs become more complex, PCB designers face the challenge of cramming more components and connections onto a limited board area without compromising performance or quality. Increasing the number of signal layers can help to accommodate more signal routing and reduce crosstalk, but there are inevitable bottlenecks in the breakout of high pin-count devices. The use of high-density interconnects, blind and buried vias, and via-in-pad techniques also help to alleviate these issues.
Ball grid array (BGA) packages come in a variety of pitches and sizes. As device complexity increases and OEMs continue their drive toward smaller components, ball pitches of 0.5 mm and lower are becoming more popular. Today, there are 0.4-mm pitch BGAs in virtually every smartphone, and 0.3-mm ultra-fine pitch BGAs are the next generation. The next step is to increase functionality within the same package. Early adopters are venturing into the 0.3-mm pitch devices. However, there are currently no formal IPC design guidelines or layout rules specifically tailored to supporting 0.3-mm pitch devices. As a result, many PCB designers largely rely on traditional 0.5-mm pitch design guidelines and layout rules to develop new 0.3-mm pitch device-based designs. For instance, the current design guidelines allow the use of a solder-ball-joint pad with a diameter of 20% less than the diameter of a BGA/CSP solder ball.
Table 1 gives an example of the required feature sizes for BGAs. This enables us to determine the signal layer count required to breakout from fine-pitch BGAs. The minimum number of signal routing layers required to route a particular design can be estimated once the location of the signals on the BGA is known.
- The first two rows/columns will route on one signal layer
- The second two rows/columns will route on a second signal layer
Plus, an additional signal layer is generally required for every row of signal balls past four rows.
This assumes that all balls are routed because their signals are needed for connectivity. But if some balls are no-connects, then those corresponding ball escape lanes are free for other signals. In this regard, fewer layers may suffice if the required signals have enough viable routing lanes. Blind microvias and vias-in-pad are normally required for the breakout of 0.5-mm pitch or less.
Accommodating the high number of individual power supplies to the BGA is also an issue. One can generally place three to four power pours on each power layer depending on the BGA pinout. So, four power layers typically are required for 10 supplies plus ground. This could be reduced if some of the power pours are combined with signals on a mixed layer.
As the data rate increases, the bandwidth required for data transmission also increases, which poses challenges for PCB design such as signal integrity, crosstalk, impedance matching, and electromagnetic interference. The PCB designer must also balance the layer count vs. manufacturing complexity. Signal integrity requirements may also impact this decision if, for instance, parallel trace segments are over 12 mm in length with a 200 ps rise time.
PCB design is a complex and challenging task that requires designers to consider various aspects that influence the performance and quality of the PCB. Among these aspects, signal integrity, power integrity, thermal management, and electromagnetic compatibility are crucial for ensuring the functionality and reliability of the PCB. PCB designers need to acquire more knowledge and skills to analyze and optimize these aspects of PCB design using appropriate principles, methods and tools.
The increased data rates also require more complex modulation schemes for data encoding, such as non-return-to-zero (NRZ) to pulse amplitude modulation 4-level (PAM4) encoding. These schemes use multiple levels or phases of signals to encode more bits per symbol, which increases the spectral efficiency and data rate of the channel. However, these schemes also increase the complexity and sensitivity of the signal processing and recovery circuits, which require careful PCB design to ensure proper signal quality and synchronization. NRZ is a modulation technique that has two voltage levels to represent logic 0 and logic 1. While PAM4 uses four voltage levels to represent four combinations of 2-bit logic: 11, 10, 01, and 00 (Figure 1).
Impedance is the key factor that controls the stability of a design. It is the core issue of the signal integrity methodology. The impedance should be simulated by a field solver to obtain accurate values of impedance for each signal layer of the substrate. The impedance of the trace is extremely important, as any mismatch along the transmission path will result in a reduction in the quality of the signal and possible radiation of noise. For perfect transfer of energy, the impedance at the source must equal the impedance at the load.
However, this is not naturally the case and terminations are generally required at fast edge rates to limit ringing. If this noise is not constrained at the source, then it will be coupled into nearby victim traces (crosstalk) and radiate to create more EMI. Apart from the issues of EMI, signal integrity, and crosstalk, this noise can cause intermittent operation of the product due to timing glitches and interference, dramatically reducing the reliability of the product. Excessive ringing can also lead to power integrity issues.
Flight time delay and skew are the key pillars in high-speed PCB design signal integrity. One of the driving factors for flight time and skew performance is the placement of components. In the classic high-speed design flow, timing specifications simulation results are compared to determine placement and routing constraints. Given a length constraint, a designer can control signal integrity by controlling the PCB trace topology of the various parts of an interface. Included in this topology are any terminations. Figure 2 shows an eye diagram of a signal with jitter and ringing due to poor termination.
The integrity of the PCB stackup and the PDN are the basis for a stable product. Multilayer PCB design is becoming more complex and less forgiving—it’s not just about signal integrity, crosstalk, and EMI. The substrate and the power delivery system are extremely critical and if they should fail then the whole system can go down or, in the worst case, may just work intermittently.
Today’s high-performance processors employ low DC voltages with high transient currents and high clock frequencies to minimize power consumption and hence the amount of heat dissipated. A typical high-speed design contains 10 or more individual power supplies. And unfortunately, the lower core voltages, higher currents, and faster edge rates all impact the power distribution network (PDN) design, as well as signal integrity.
Ideally, the effective impedance of the PDN should be kept below the target impedance up to the maximum required bandwidth. However, if the impedance is too far below the target, then this implies that the PDN has been overdesigned which unnecessarily increases costs with little added benefit. If your company intends to build hundreds of thousands of assemblies, then the potential cost saving can be quite significant. Analyzing the PDN ensures the best performance at the most cost-effective price.
Many competent PCB designers will retire within the next few years leaving a void in the knowledge base. This creates a shortage of skilled and experienced PCB designers, increases the demand for new and young PCB designers, and allows for more opportunities for collaboration and innovation among PCB designers. However, the lack of manufacturing knowledge of the upcoming designers can cause design errors and failures, increase the design time and cost, and reduce the manufacturability and yield of the product.
Experience is the best teacher of all. PCB designers need to have more knowledge and skills to design PCBs that have high signal integrity, power integrity, thermal performance, and electromagnetic compatibility. PCB designers must understand the principles, methods, and tools for analyzing and optimizing all aspects of PCB design.
Key Points
- PCB designers must deal with various issues in finding the right balance between the form factor, functionality, and power requirements of their boards.
- BGA pitches of 0.5 mm and lower are becoming more popular.
- 0.3-mm ultra-fine pitch BGAs and increased functionality within the same package are the next generation.
- Currently there are no formal IPC design guidelines or layout rules specifically tailored to supporting 0.3-mm pitch devices.
- Blind microvias and vias-in-pad are normally required for the breakout of 0.5 mm pitch or less.
- Accommodating the high number of individual power supplies to the BGA is also an issue.
- The increased data rates also require more complex modulation schemes for data encoding, such as non-return-to-zero (NRZ) to pulse amplitude modulation 4-level (PAM4) encoding.
- The impedance should be simulated by a field solver to obtain accurate values of impedance for each signal layer of the substrate.
- Flight time delay and skew are the key pillars in high-speed PCB design signal integrity.
- The integrity of the PCB stackup and the PDN are the basis for a stable product.
- The lower core voltages of today’s processors require higher currents and faster edge rates.
- The effective impedance of the PDN should be kept below the target impedance up to the maximum required bandwidth.
- If the impedance is too far below the target, then this implies that the PDN has been overdesigned which unnecessarily increases costs with little added benefit.
Resources
- Beyond Design by Barry Olney: “Fly-over Technology: When It All Gets Too Fast,” “Signal Integrity (Parts 1 & 3),” “The Target Impedance Approach to PDN Design.”
- AM57xx BGA PCB Design, Texas Instruments.
- “Metric Pitch BGA and Micro BGA Routing Solutions” by Tom Hausherr.
This column originally appeared in the June 2023 issue of Design007 Magazine.
More Columns from Beyond Design
Beyond Design: The Metamorphosis of the PCB RouterBeyond Design: Radiation and Interference Coupling
Beyond Design: Key SI Considerations for High-speed PCB Design
Beyond Design: Electro-optical Circuit Boards
Beyond Design: AI-driven Inverse Stackup Optimization
Beyond Design: High-speed Rules of Thumb
Beyond Design: Integrated Circuit to PCB Integration
Beyond Design: Does Current Deliver the Energy in a Circuit?