-
-
News
News Highlights
- Books
Featured Books
- pcb007 Magazine
Latest Issues
Current IssueThe Hole Truth: Via Integrity in an HDI World
From the drilled hole to registration across multiple sequential lamination cycles, to the quality of your copper plating, via reliability in an HDI world is becoming an ever-greater challenge. This month we look at “The Hole Truth,” from creating the “perfect” via to how you can assure via quality and reliability, the first time, every time.
In Pursuit of Perfection: Defect Reduction
For bare PCB board fabrication, defect reduction is a critical aspect of a company's bottom line profitability. In this issue, we examine how imaging, etching, and plating processes can provide information and insight into reducing defects and increasing yields.
Voices of the Industry
We take the pulse of the PCB industry by sharing insights from leading fabricators and suppliers in this month's issue. We've gathered their thoughts on the new U.S. administration, spending, the war in Ukraine, and their most pressing needs. It’s an eye-opening and enlightening look behind the curtain.
- Articles
- Columns
- Links
- Media kit
||| MENU - pcb007 Magazine
Reduce Board Skyline With Solid Cavity Design
July 20, 2023 | Kris Moyer, IPCEstimated reading time: 2 minutes
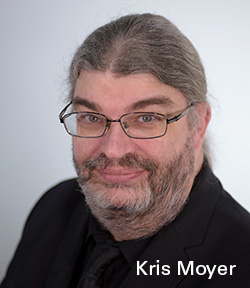
With the increasing shrinkage of modern electronics in both board size and product volume, it’s becoming more difficult to mount components to the PCB surface and still meet volumetric requirements. To avoid chip-on-board (COB) processing, board cavities can help mitigate the Z-axis skyline volumetric issues and allow for components that would otherwise not fit within the skyline to be used.
As the name implies, a cavity is the removal of some of the board material to expose traces and contact pads on inner layers of the PCB. This is done to allow attachment of the component to these exposed pads rather than pads on the surface of the PCB (Figure 1). To form cavities, several special processes need to be considered. Among these are inner layer plating, particularly the effects of plating and surface finish on inner layer impedance for signal integrity; sequential lamination; surface finish on exposed inner layer pads; and the use of controlled depth milling to form the cavity, just to name a few.
Figure 1: A typical cavity as it appears in an ECAD software tool.
One of the first items of concern is the effect of plating and surface finish on impedance of the inner layers. When cavities are formed without sequential lamination, the plating and surface finish needed to support the soldering process will add conductive material thickness to the exposed areas of the inner layer. This in turn will cause an impedance discontinuity due to these different thicknesses of the traces.
Additionally, the removal of the reference planes from one side of the conductor changes the structure of the transmission line from a stripline on inner layer to a microstrip in the cavity. Most ECAD and SI tools do not support different transmission line structures on the same layer of the board. There are some solutions to this conundrum: Rather than relying on the built-in transmission line structures of ECAD tools, the designer can manually calculate the controlled impedance trace widths for the stripline and microstrip sections and then use area constraint rules to define the widths both in the cavity and on the remainder of the layer.
One possible way around this issue is to use sequential lamination to allow plating on the entire layer. But sequential lamination poses its own problems. First, it is a more costly and time-consuming process. Second, it adds fabrication allowances. It may also require the use of blind and/or buried vias to make the connections between layers. The multiple plating cycles needed for sequential lamination can cause other fabrication issues. It is recommended that the fabricator be consulted on any sequential lamination PCB design.
To read this entire article, which appeared in the July 2023 issue of Design007 Magazine, click here.
Suggested Items
Hands-On Demos Now Available for Apollo Seiko’s EF and AF Selective Soldering Lines
06/30/2025 | Apollo SeikoApollo Seiko, a leading innovator in soldering technology, is excited to spotlight its expanded lineup of EF and AF Series Selective Soldering Systems, now available for live demonstrations in its newly dedicated demo room.
SolderKing’s Successful Approach to Modern Soldering Needs
06/18/2025 | Nolan Johnson, I-Connect007Chris Ward, co-founder of the family-owned SolderKing, discusses his company's rapid growth and recent recognition with the King’s Award for Enterprise. Chris shares how SolderKing has achieved these award-winning levels of service in such a short timeframe. Their secret? Being flexible in a changing market, technical prowess, and strong customer support.
E-tronix Announces Upcoming Webinar with ELMOTEC: Optimizing Soldering Quality and Efficiency with Robotic Automation
05/30/2025 | E-tronixE-tronix, a Stromberg Company, is excited to host an informative webinar presented by Raphael Luchs, CEO of ELMOTEC, titled "Optimize Soldering Quality and Efficiency with Robotic Automation," taking place on Wednesday, June 4, 2025 at 12:00 PM CDT.
SMTA Releases Final Batch of Training Resources Donated by Bob Willis
05/29/2025 | SMTAThe Surface Mount Technology Association (SMTA) announces the release of several more webinars, poster sets, and photo libraries to conclude a generous donation from renowned industry expert Bob Willis.
Altus Supports Phoenix Systems in Advancing THT Assembly with Robotic Soldering
05/27/2025 | Altus GroupAltus Group, a leading distributor of capital equipment in the UK and Ireland, has successfully supported Phoenix Systems UK Ltd in its investment in robotic soldering technology to further enhance its through-hole technology (THT) assembly processes.