-
-
News
News Highlights
- Books
Featured Books
- pcb007 Magazine
Latest Issues
Current IssueThe Hole Truth: Via Integrity in an HDI World
From the drilled hole to registration across multiple sequential lamination cycles, to the quality of your copper plating, via reliability in an HDI world is becoming an ever-greater challenge. This month we look at “The Hole Truth,” from creating the “perfect” via to how you can assure via quality and reliability, the first time, every time.
In Pursuit of Perfection: Defect Reduction
For bare PCB board fabrication, defect reduction is a critical aspect of a company's bottom line profitability. In this issue, we examine how imaging, etching, and plating processes can provide information and insight into reducing defects and increasing yields.
Voices of the Industry
We take the pulse of the PCB industry by sharing insights from leading fabricators and suppliers in this month's issue. We've gathered their thoughts on the new U.S. administration, spending, the war in Ukraine, and their most pressing needs. It’s an eye-opening and enlightening look behind the curtain.
- Articles
- Columns
- Links
- Media kit
||| MENU - pcb007 Magazine
A 21st Century Perspective on Data, Analysis, and TQM
August 8, 2023 | Nolan Johnson, I-Connect007Estimated reading time: 2 minutes
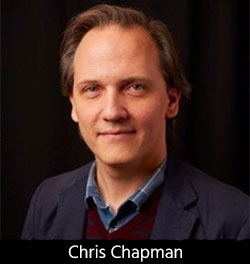
Chris Chapman is a Deming management method practitioner and consultant who publishes “The Digestible Deming” blog on Substack. Chris has been a student of Deming’s agile, Lean, and related methods since 2007. With his software and data background, he brings something of a 21st century perspective to quality. In this conversation, we explore how data and AI might be changing how we approach quality.
Nolan Johnson: Chris, as we talk about TQM, I’d like to ask you to consider the amount of data that we now have available. Our ability to collect data, implement sensors, get real-time data from the manufacturing floor, analyze it, and make it available to upper management has increased. What would be Deming’s perspective on this amount of data? Back in his day, surely, they didn’t have this much data to roll up.
Christopher Chapman: There's a fantastic little quip in Dr. Joyce Orsini’s book, The Essential Deming. Joyce was one of Deming’s PhD students and worked with him right up until the end. In one chapter, he comments on the data that was available to management back then. He says, “Tons of figures, no knowledge.” It was the idea that, even 30 to 40 years ago, you could have voluminous amounts of information that would overwhelm management—never mind what we can get access to today—without any real methodology to interpret what you're actually seeing. , to distinguish signals from noise and gain insights into what the data is telling you about how a system or process is working.
Here's a real-world example from a particular customer of mine in telecom, where they wanted to track the activation of Apple watches as the first versions rolled out. How many people were going onto the network? A senior executive who was very hot to trot on understanding this said, “Gather all the data that tells me the activation and deactivation rates of these watches nationwide.”
It took seven or eight hours a day for people to pull together that data from all the systems and roll it up onto a dashboard as a single number. That number was green when it went up, and red when it went down. You can imagine the attendant behavior which that encouraged.
What I suggested to the managers I was working with was to present the data in context over time on a run chart with process limits, such that the leadership could see a quarter’s worth of activation, perhaps. In that way, you could take some of the temperature, and establish what the estimated three sigma limits are for normal activations. You don't have to explain the math, don't draw them manually; just calculate the limits and report what the picture of normal looks like. We want it to economize our interventions only to when we see very overt signals above or below limits in the activation/deactivation cycle. Only then do we look at the contributory system indications for that.
To read this entire conversation, which appeared in the July 2023 issue of PCB007 Magazine, click here.
Suggested Items
Specially Developed for Laser Plastic Welding from LPKF
06/25/2025 | LPKFLPKF introduces TherMoPro, a thermographic analysis system specifically developed for laser plastic welding that transforms thermal data into concrete actionable insights. Through automated capture, evaluation, and interpretation of surface temperature patterns immediately after welding, the system provides unprecedented process transparency that correlates with product joining quality and long-term product stability.
Smart Automation: The Power of Data Integration in Electronics Manufacturing
06/24/2025 | Josh Casper -- Column: Smart AutomationAs EMS companies adopt automation, machine data collection and integration are among the biggest challenges. It’s now commonplace for equipment to collect and output vast amounts of data, sometimes more than a manufacturer knows what to do with. While many OEM equipment vendors offer full-line solutions, most EMS companies still take a vendor-agnostic approach, selecting the equipment companies that best serve their needs rather than a single-vendor solution.
Keysight, NTT, and NTT Innovative Devices Achieve 280 Gbps World Record Data Rate with Sub-Terahertz for 6G
06/17/2025 | Keysight TechnologiesKeysight Technologies, Inc. in collaboration with NTT Corporation and NTT Innovative Devices Corporation (NTT Innovative Devices), today announced a groundbreaking world record in data rate achieved using sub-THz frequencies.
Priority Software Announces the New, Game-Changing aiERP
06/12/2025 | Priority SoftwarePriority Software Ltd., a leading global provider of ERP and business management software announces its revolutionary aiERP, leveraging the power of AI to transform business operations.
Breaking Silos with Intelligence: Connectivity of Component-level Data Across the SMT Line
06/09/2025 | Dr. Eyal Weiss, CybordAs the complexity and demands of electronics manufacturing continue to rise, the smart factory is no longer a distant vision; it has become a necessity. While machine connectivity and line-level data integration have gained traction in recent years, one of the most overlooked opportunities lies in the component itself. Specifically, in the data captured just milliseconds before a component is placed onto the PCB, which often goes unexamined and is permanently lost once reflow begins.