-
- News
- Books
Featured Books
- smt007 Magazine
Latest Issues
Current IssueSupply Chain Strategies
A successful brand is built on strong customer relationships—anchored by a well-orchestrated supply chain at its core. This month, we look at how managing your supply chain directly influences customer perception.
What's Your Sweet Spot?
Are you in a niche that’s growing or shrinking? Is it time to reassess and refocus? We spotlight companies thriving by redefining or reinforcing their niche. What are their insights?
Moving Forward With Confidence
In this issue, we focus on sales and quoting, workforce training, new IPC leadership in the U.S. and Canada, the effects of tariffs, CFX standards, and much more—all designed to provide perspective as you move through the cloud bank of today's shifting economic market.
- Articles
- Columns
- Links
- Media kit
||| MENU - smt007 Magazine
Estimated reading time: 19 minutes
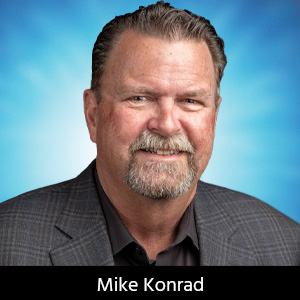
The Knowledge Base: The Role of Automated Inspection Systems
I invited three experts within the AOI space to answer 10 questions: Brian D'Amico, president of MIRTEC USA; Joel Scutchfield, general manager of SMT business operations and director of sales at Koh Young America, Inc.; and Arif Virani, COO of Darwin AI. In this insightful interview, we delve into the pivotal role of automated inspection systems in the electronics assembly industry.
In an era where technology is rapidly advancing, electronic devices have become an integral part of our daily lives, powering everything from smartphones and laptops to medical equipment and automotive systems. With this increased reliance on electronics, ensuring the quality and reliability of electronic assemblies has never been more critical.
Automated inspection systems have emerged as a game-changer in this dynamic landscape, offering a level of precision, speed, and consistency that human inspection alone simply cannot match. These systems employ advanced technologies such as machine vision, artificial intelligence, and robotics to meticulously scrutinize electronic components and assemblies, identifying defects and anomalies with unparalleled accuracy.
We explore the multifaceted significance of automated inspection systems in the electronics assembly industry. We will discuss their pivotal role in maintaining product quality, streamlining production processes, reducing costs, and enhancing overall efficiency. Moreover, our experts share their insights into the latest advancements in automated inspection technology and how these innovations are reshaping the electronic assembly landscape.
What are the primary objectives of implementing automatic inspection systems in electronics manufacturing?
Brian D'Amico: The primary objective of implementing automatic inspection systems is to eliminate defects within the manufacturing process. This may be accomplished not only by flagging these defects for review and rework but using the resulting inspection data to virtually eliminate the opportunity for the defect to ever occur in the first place.
Joel Scutchfield: Most think the primary reason for inspection is “defect catching” at the various typical inspection points where we inspect on a standard SMT line, including post-print, post-placement/pre-reflow, post-reflow, X-ray, or any of the various special inspection points (pin/terminal, dispensed process, THT etc.). Although this approach does provide peace of mind in terms of quality assurance and helps to ensure that escapes do not happen (do not get to the customer), the bigger benefit and value is in the use of the data provided from each of these inspection points to correct and control the assembly process, thereby preventing the defects from happening for all future builds. Taking that to the next level, we use the inspection results data to feed AI engines, which can automatically provide that control of the various processes involved, thus moving us closer to the self-healing process that is “real” Smart factory realization.
Arif Virani: Automatic inspection systems aim to improve inspection quality and consistency while reducing costs.
Can you explain the key components and technologies involved in an automatic inspection system for electronics manufacturing?
D'Amico: There are a variety of different components and technologies involved in automatic inspection systems. Most systems are configured with high-resolution optics and lighting systems combined with various forms of 3D inspection technology such as moiré and laser.
Scutchfield: I’ll speak to SPI and AOI, specifically. There are multiple methods (technologies) being utilized for SPI and AOI depending on whether 2D or 3D is being used. When it comes to 3D, there are two basic approaches: moiré interferometry and laser. Laser, unfortunately, has several shortcomings as it applies to the PCB inspection world for SPI and AOI, which is
the reason most providers use the moiré approach to varying degrees. That’s important to note, because not all 3D is created equal. Technically, a 3D image can be generated from a single moiré projector, but that image will be susceptible to back side shadows, opposite the side of the component where the moiré pattern is being projected. Thus, a minimum of two projectors are needed to eliminate the “back side shadow phenomenon.” An inspection system needs to gather the right kind of data (measurement based, parametric results) using very precise subsystems for pattern generation and data gathering to gather the right amount of data from a multitude of sources for superior statistical relevancy.
Virani: AI-based inspection systems have five key components:
- Optics/lighting: Taking images of the PCBA, components, and defects.
- Material handling: Conveyor and logic to move PCBAs through the system.
- Artificial intelligence models: Analyze PCBA images for defects and additional information.
- Line interface: Interface for operator to monitor and control inspection.
- Engineer/quality user interface: Interface to enable AI learning and continuous improvement of inspection performance.
What are the different types of automatic inspection systems commonly used in electronics manufacturing, and when is each type most appropriate?
D'Amico: There are many types of automated inspection systems used in electronics manufacturing, including solder paste inspection (SPI), automated optical inspection (AOI), flying probe, and X-ray. Each of these systems is used at a variety of different locations within the manufacturing process. SPI is primarily used post-solder deposition but may also
be used for inspection of deposition of adhesives. AOI may be used either post-placement or post-reflow to verify the proper placement and electrical connectivity of each component on the PCB. Flying probe is used to check electrical characteristics of the finished PCB after optical inspection for manufacturing defects. X-ray may be used at virtually any phase of the manufacturing process but is primarily used to inspect solder connectivity for bottom terminated devices.
Scutchfield: SPI systems inspect the solder paste after print to confirm the position and volume of the print vs. the expected values for each. AOI can be used in various locations with different flavors, including a less complex offering (fewer projectors) for pre-reflow inspection, where we’re looking to confirm that all the parts are correct, and they have been accurately placed in the right location and the correct polarity. The use of pre-reflow AOI continues to grow quickly for many valid reasons, some of which are related to the components and labor shortages that many EMS providers are still dealing with. Systems used in the pre-reflow location are typically less complex with regard to the number of projectors and camera complexity, because the inspections being performed in this location can be done effectively with such systems, which are typically also less costly. For post-reflow AOI inspection (most common location for AOI), the more complex systems are typically used due to the need to inspect solder joints and the properties that come with solder joint inspection, including hidden joints, and very reflective solder. AOI is also used for pin and terminal inspection where a high content of both is present. These systems typically require some difference in the configuration, due to the reflective nature of plated pins and terminals. Through-hole inspection can fall into this same category. Dispensed process inspection is also used where the need for conformal coating, underfill, or potting inspection is needed to confirm thickness and/or volume of each.
Virani: The types of automatic inspection systems commonly used in electronics manufacturing can be categorized as follows:
A. Visual inspection is the most flexible and versatile amongst the types of automatic inspection systems, and is appropriate at different stages of the electronics manufacturing process including:
- Parts inspection, such as the initial parts arrival stage, to check whether received parts are damaged
- Placement, to check whether components are placed properly/not missing/damaged, and whether the components are the right ones
- Solder reflow stage to ensure parts are properly soldered
- Hand load through-hole stage to ensure proper placement
- Final assembly stage to ensure that components have not moved/become missing/wrong polarity/damaged, and solder is not missing/creating bridges
Wash stages to ensure components and solder have not been washed away/damaged
B. Non-destructive testing, such as X-ray inspection systems, is most appropriate for situations where you need to look below or within a component for damage (e.g., BGA solder paste inspection) and most appropriate at the parts arrival stage and final inspection stage.
C. Functional testing and in-circuit testing (ICT) are most appropriate at the final assembly stage to determine whether the board is producing the desired results and to electrically probe the assembled electronics to check for shorts, opens, and capacitance.
How do automatic inspection systems contribute to improving quality control and reducing defects in electronics manufacturing?
D'Amico: The whole purpose of test and inspection is to collect actionable data that may be used to reduce defects and maximize efficiency within the manufacturing line. The goal is to minimize scrap and get a really good handle on those process parameters that need to be put in place to manufacture products the right way the first time.
Scutchfield: It all starts with having the right kind of measurement-based data, and then applying it the right way, both manually and in an automated fashion where possible, to reduce the need for human intervention. The data that inspection systems provide is now thought to be the most critical and important information that can be gathered to run the SMT line properly. So, those results must be correct and very reliable. The performance and success of the line depends on it.
Virani: Automatic inspection systems offer a consistent and accurate way to identify defects. These systems are especially useful for complex printed circuit board assemblies (PCBAs) that contain thousands of components, as they can complete inspections much faster than human inspectors, thus improving cycle time.
Moreover, newer AI-based inspection systems are cost-effective and can be deployed across multiple locations within the production process. This helps to catch defects in real-time, as they occur, allowing for prompt corrective action. Additionally, the end-to-end data collected by these systems provides valuable insights into the production process, highlighting opportunities for improvement.
Page 1 of 2
More Columns from The Knowledge Base
The Knowledge Base: Cultivating Your Brand in the Age of ConnectionThe Knowledge Base: A Conference for Cleaning and Coating of Mission-critical Electronics
The Knowledge Base: Building the Workforce of Tomorrow With EMAC
The Knowledge Base: Beyond the Badge—Why Membership Matters More Than Ever
The Knowledge Base: Unlocking the Invisible—The Critical Role of X-ray Technology
The Knowledge Base: At the Forefront of Electronics Manufacturing
The Knowledge Base: Challenges and Considerations of Harsh Environments
The Knowledge Base: My 2025 Industry Wish List