-
-
News
News Highlights
- Books
Featured Books
- design007 Magazine
Latest Issues
Current IssueAll About That Route
Most designers favor manual routing, but today's interactive autorouters may be changing designers' minds by allowing users more direct control. In this issue, our expert contributors discuss a variety of manual and autorouting strategies.
Creating the Ideal Data Package
Why is it so difficult to create the ideal data package? Many of these simple errors can be alleviated by paying attention to detail—and knowing what issues to look out for. So, this month, our experts weigh in on the best practices for creating the ideal design data package for your design.
Designing Through the Noise
Our experts discuss the constantly evolving world of RF design, including the many tradeoffs, material considerations, and design tips and techniques that designers and design engineers need to know to succeed in this high-frequency realm.
- Articles
- Columns
- Links
- Media kit
||| MENU - design007 Magazine
Manufacturing Driven Design: Moving Beyond DFM
October 19, 2023 | Andy Shaughnessy, Design007 MagazineEstimated reading time: 8 minutes
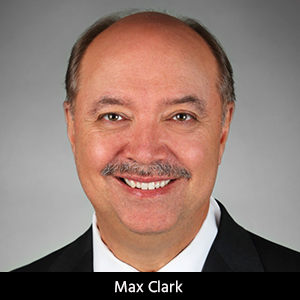
I-Connect007 recently published The Printed Circuit Designer's Guide to... Manufacturing Driven Design, written by Max Clark, business unit director for the Valor NPI line at Siemens.
I sat down for an interview with Max during PCB West and asked him to explain exactly what manufacturing driven design entails. As he says, MDD isn’t just another term for DFM; it’s a whole new way of thinking. If the industry embraces this concept, it could save companies millions of dollars each year, but it’s going to require companies to work together with their manufacturing partners.
Andy Shaughnessy: How's it going, Max? You just wrote a book that’s now available in the I-Connect007 library, The Printed Circuit Designer's Guide to... Manufacturing Driven Design. How did you come up with that term? And where are you going with that?
Max Clark: I've been in the industry since 1989 and that is when I first started working with CAM systems. The CAM system I first started working with actually utilized hardware for doing DRC. The system would digitize the artwork for the PCB, then transfer that image into a hardware cage that we used to do AOI inspection. We basically blinded the AOI solution, feed the bits into that hardware cage, and the hardware gave us back marks. We would then represent the marks in the CAM solution, and someone had to interpret those marks. It was very unintelligent and hardware-intensive because the computers at the time just didn't have the capacity to do the type of analysis that we needed.
But as time progressed, we started developing software for DRC. At that time, we checked spacing and annular rings—just very basic things that the hardware did as well. When we started Valor, we wanted to deliver DRC, but we wanted to differentiate our solution from others. That is when we started using DFM (design for manufacturing) as the acronym rather than DRC. Based on our experience, we developed a large number of analyze of different types; signal, power and ground, solder mask…the list goes on. We introduced those solutions using DFM as a reference, but we sold it to the fabricators initially, not to the design organizations.
Then, out of the blue one day, we got a call from a sizable company who said, “We want to buy your CAM solution because we're sending our designs out to manufacturers and they're finding problems in our designs using the Valor software. We'd like to bring that capability in-house.” We thought, “That's a heck of an idea. Didn't see that coming.” We understood what they were looking to do, and we thought it was a good idea, too. We did two initial translators: a BoardStation translator for Mentor Graphics, and we also did a Cadence Allegro translator. And from there, we started selling that solution to the design organizations.
More recently I have been thinking that if what we originally created was used in the manufacturing space, is it really DFM? I suggest that since the analysis was being performed in manufacturing that really it is not design for manufacturing and instead is manufacturing in spite of design. Even today, when OEMs have implemented DFM, they have put it at the end of the design process as kind of a final check before releasing a design to manufacturing. We realize that for our customers to get the maximum benefit of our manufacturing knowledge, we need to make our DFM analysis operate concurrent with the design process. And that was the motivation behind the term MDD, and the book.
Shaughnessy: How is MDD different from DFM?
Clark: It starts with the manufacturer. Every manufacturer communicates their process capabilities in some form to their customers. One of the foundations of MDD is for the manufacturers to provide a rule deck of their process capabilities, such that while the designer is laying out the board the manufacturer’s rule deck identifies instances where the design can be improved for manufacturability.
Designers today typically don't know the manufacturing requirements of a PCB, especially when you consider the numerous constructions, features and components in use. Yet we're requiring them to go to the printed circuit board manufacturer’s websites or PDFs to transcribe those constraints into their tool. It's not palatable; it's not manageable. And most EDA DRC tools do not address the majority ofmanufacturing process constraints. Sometimes, designers don't even know the terminology of the processes being used. The manufacturers have good intentions, but in reality, it’s a real mess.
We're using our PCBflow platform to harness the digital representations of the manufacturer’s process capabilities. We refer to this as a DFM Profile. When a designer goes to perform MDD, the analysis will then be automatically based upon where they intend to manufacture their printed circuit board, even if they have multiple suppliers. This is unique; it will be a game-changer.
As the industry consolidates into smaller and smaller teams, the systems need to tell the designer why this is a problem, not simply that this is a problem. Because the next thing they always ask is, “Why?” And then they're on their phone with their manufacturer. MDD will flag the problem and provide the explanations why. So the designer can reply, “OK, I don't want that problem. Let’s fix it.” They don't have to call anybody. Our goal is to eliminate all possibilities for any technical queries to come up. Because technical queries add anywhere from a week or two weeks of delay to a design. The more information that we provide up front, the less the likelihood of those technical queries.
Shaughnessy: PCBflow is pretty interesting. It can contain digital twins for all the different manufacturers, so designers can get information without having to make that phone call. It sounds like a kind of fabricator database.
Clark: Right, except PCBflow also contains assembly constraints and therefore it is a PCB manufacturer database. PCBflow has a DFM portion as well, powered by proportionally-scaled release of Valor NPI analysis. Our Valor NPI product serves the enterprise market with its connection to the PCBFlow platform that also contains a DFM service offering for the small and mid-sized markets. PCBFlow will offer DFM services, right to that market niche. Valor NPI customers will first make a connection to the supplier. You're creating a social network of providers; you have to be “friends” so to speak. Some manufacturers will want everybody to have their DFM Profiles. But then other manufacturers will prefer to manage the relationships.
Soon we'll put other functionalities on the PCBFlow platform that both the midsize market and the enterprise market will use–collaboration plans, and all kinds of potential services. I'm very excited. I think this is a real change and it must be challenged to ensure success. In this regard I believe the PCB industry is stuck in its ways. The IC foundries share their capabilities. If they can't build a design, they won’t commit it to a wafer. They don't want to put it on a wafer and then have it scrapped. The wafer and the fabrication schedule are too valuable to waste. That is why they require their customers to run analysis on the design using the foundry’s rule deck before it is accepted for manufacturing.
Shaughnessy: Maybe we need to act more like the semiconductor industry. They won’t take the job it if it’s not right. PCB manufacturers take whatever they get because they want the job.
Clark: That’s right, Andy. The PCB industry would be wise to learn from the semiconductor industry. When quality, costs, and speed matter, they’ve got it down.
Shaughnessy: So, what's next for your MDD quest? Where do you hope this will be in the next couple of years?
Clark: Even today, design tools don't learn from previous experiences. As a company that prides itself on analysis, it's kind of a shame that we haven't put together a solution that can look at the history of thousands of designs from your company, pipe this summary data into a solution to perform the analysis based on previous attempts, then build a report on projected yield and anticipated problems on this design. It would be a way to look beyond design issues and provide a more holistic project view of the design.
I also think we can develop analysis that is more self-tuning. One of the challenges in this type of solution is false errors being flagged. You try to tune the check, but it just keeps generating wrong results. So, the user starts ignoring those errors. And then one day, that one needle-in-the-haystack error pops up. And the manager says, “Didn't you run DFM?” And the engineer says, “Yeah, I did. But I didn't go into all the results because they are usually false. I just approved it.” It would be nice if the next-generation system is better at yield prediction. The tool could then tell us, “Look, you've run 100 designs, you have all these annular ring problems, and you've never done anything about it. I highly suspect the values you're checking about are just not right.”
I always tell people, “It’s one of two areas where we get a lot of results. Either your values are wrong, or your designs do not match the manufacturing requirements.” If you're building your designs and you're not going to change them, then your defined manufacturing requirements need to change. And we start capturing that information to make suggestions. Once the irrelevant rules are cleaned up, you go from 3,000 errors to three, I'll look closely at three errors. But if you give me 3,000 errors, I'm going to rely on my judgement. That’s the kind of thinking that I’d like to see the next-generation system do.
Shaughnessy: Thanks for your time, Max.
Clark: My pleasure, Andy.
Download your own copy of The Printed Circuit Designer's Guide to... Manufacturing Driven Design and other educational titles at I-007eBooks.
Suggested Items
DownStream Acquisition Fits Siemens’ ‘Left-Shift’ Model
06/26/2025 | Andy Shaughnessy, I-Connect007I recently spoke to DownStream Technologies founder Joe Clark about the company’s acquisition by Siemens. We were later joined by A.J. Incorvaia, Siemens’ senior VP of electronic board systems. Joe discussed how he, Rick Almeida, and Ken Tepper launched the company in the months after 9/11 and how the acquisition came about. A.J. provides some background on the acquisition and explains why the companies’ tools are complementary.
Elementary Mr. Watson: Retro Routers vs. Modern Boards—The Silent Struggle on Your Screen
06/26/2025 | John Watson -- Column: Elementary, Mr. WatsonThere's a story about a young woman preparing a holiday ham. Before putting it in the pan, she cuts off the ends. When asked why, she shrugs and says, "That's how my mom always did it." She asks her mother, who gives the same answer. Eventually, the question reaches Grandma, who laughs and says, "Oh, I only cut the ends off because my pan was too small." This story is a powerful analogy for how many PCB designers approach routing today.
Siemens Turbocharges Semiconductor and PCB Design Portfolio with Generative and Agentic AI
06/24/2025 | SiemensAt the 2025 Design Automation Conference, Siemens Digital Industries Software today unveiled its AI-enhanced toolset for the EDA design flow.
Cadence AI Autorouter May Transform the Landscape
06/19/2025 | Andy Shaughnessy, Design007 MagazinePatrick Davis, product management director with Cadence Design Systems, discusses advancements in autorouting technology, including AI. He emphasizes a holistic approach that enhances placement and power distribution before routing. He points out that younger engineers seem more likely to embrace autorouting, while the veteran designers are still wary of giving up too much control. Will AI help autorouters finally gain industry-wide acceptance?
Beyond Design: The Metamorphosis of the PCB Router
06/18/2025 | Barry Olney -- Column: Beyond DesignThe traditional PCB design process is often time-consuming and labor-intensive. Routing a complex PCB layout can consume up to 30% of a designer’s time, and addressing this issue is not straightforward. We have all encountered this scenario: You spend hours setting the constraints and finally hit the Go button, only to be surprised by the lack of visual appeal and the obvious flaws in the result.