-
- News
- Books
Featured Books
- smt007 Magazine
Latest Issues
Current IssueSupply Chain Strategies
A successful brand is built on strong customer relationships—anchored by a well-orchestrated supply chain at its core. This month, we look at how managing your supply chain directly influences customer perception.
What's Your Sweet Spot?
Are you in a niche that’s growing or shrinking? Is it time to reassess and refocus? We spotlight companies thriving by redefining or reinforcing their niche. What are their insights?
Moving Forward With Confidence
In this issue, we focus on sales and quoting, workforce training, new IPC leadership in the U.S. and Canada, the effects of tariffs, CFX standards, and much more—all designed to provide perspective as you move through the cloud bank of today's shifting economic market.
- Articles
- Columns
- Links
- Media kit
||| MENU - smt007 Magazine
SEHO with Systems for Zero-Defect Production at Productronica 2023
October 19, 2023 | SEHO Systems GmbHEstimated reading time: 2 minutes
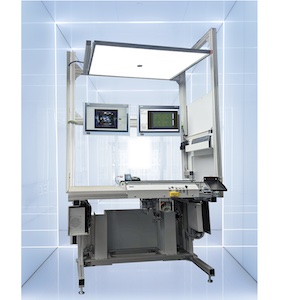
SEHO Systems GmbH, a worldwide leading manufacturer of complete solutions for soldering processes and automated production lines, ensures higher productivity in electronics production with flexible and innovative concepts. At productronica 2023, SEHO is taking another step towards zero-defect manufacturing in hall A4, stand 578.
Avoid defects before they disrupt the process flow and cause costs. With this in mind, SEHO has expanded the AOI product division. At productronica in Munich, SEHO will present the new AssemblyCheck for the first time, a component placement control system that is specifically optimized for THT assemblies.
THT components are often assembled manually or semi-automatically, so the risk of errors is correspondingly high. SEHO AssemblyCheck is integrated directly into the assembly workstation and provides immediate feedback whether the components are assembled correctly. Only then can the circuit board be released for further processing in a wave or selective soldering system. This eliminates possible errors, which leads to a significant increase in quality and yield.
SEHO AssemblyCheck generally checks for the presence of the correct components, the correct orientation or polarity, component colours are recognized and compared. Further inspection tasks include text verification (OCV), orientation and code reading. Circuit boards with a bad mark marking are automatically recognized and not checked.
Short cycle times and an assembly size of up to 610 x 510 mm [24” x 20”] guarantee high system efficiency.
To reduce investment costs when there are several workstations, the SEHO AssemblyCheck can also be used inline. The combination with the THT-AOI system SEHO PowerVision offers maximum ROI: both systems are integrated in just one module that is installed in front of the soldering system.
At the assembly transport level, AssemblyCheck checks for correct component placement. Incorrectly assembled circuit boards can be automatically removed from the line, while defect-free assemblies are released for the further process. After the soldering process, SEHO PowerVision carries out the solder joint inspection at the return conveyor level of the module.
The SEHO Selectline-C also ensures productivity increases. The modular and expandable inline selective soldering system from SEHO has been supplemented with additional modules that significantly increase the flexibility of the system. A highlight of this machine is the SmartSplit software, which turns an already efficient system into a highly flexible and highly productive selective soldering system for high-mix-high-volume production. SmartSplit controls and coordinates the process flow for different assemblies in mixed operation. The soldering process for an assembly is automatically divided among the process stations available in the respective system. Up to 6 soldering units can be integrated in one system. As a result, SmartSplit enables cycle times to be halved in mixed operation, without major investments and without restricting the maximum available working area of the system.
In the high-end wave soldering area, innovative features increase process reliability. This includes the automatic nozzle height adjustment. In up to 16 different areas of an assembly, the height of the soldering nozzles can be programmed and adjusted individually in order to always have the optimal distance between the circuit board and the soldering nozzle, depending on the product. In addition to a greater process reliability, this innovative function offers independence from the workpiece carrier or assembly design, a significantly larger process window and maximum flexibility.
Of course, the stability of the wave height also plays a crucial role. Automated and directly integrated into the soldering area, the automatic wave height control ensures a reliable process and perfect soldering results without interrupting production.
Testimonial
"The I-Connect007 team is outstanding—kind, responsive, and a true marketing partner. Their design team created fresh, eye-catching ads, and their editorial support polished our content to let our brand shine. Thank you all! "
Sweeney Ng - CEE PCBSuggested Items
KOKI to Showcase Analytical Services and New HF1200 Solder Paste at SMTA Guadalajara 2025
07/31/2025 | KOKIKOKI, a global leader in advanced soldering materials and process optimization services, will exhibit at the SMTA Guadalajara Expo & Tech Forum, taking place September 17 & 18, 2025 at Expo Guadalajara, Salón Jalisco Halls D & E in Guadalajara, Mexico.
Weller Tools Supports Future Talent with Exclusive Donation to SMTA Michigan Student Soldering Competition
07/23/2025 | Weller ToolsWeller Tools, the industry leader in hand soldering solutions, is proud to announce its support of the upcoming SMTA Michigan Expo & Tech Forum by donating a limited-edition 80th Anniversary Black Soldering Set to the event’s student soldering competition.
Silicon Mountain Contract Services Enhances SMT Capabilities with New HELLER Reflow Oven
07/17/2025 | Silicon Mountain Contract ServicesSilicon Mountain Contract Services, a leading provider of custom electronics manufacturing solutions, is proud to announce a significant upgrade to its SMT production capability with the addition of a HELLER 2043 MK5 10‑zone reflow oven to its Nampa facility.
SHENMAO Strengthens Semiconductor Capabilities with Acquisition of PMTC
07/10/2025 | SHENMAOSHENMAO America, Inc. has announced the acquisition of Profound Material Technology Co., Ltd. (PMTC), a premier Taiwan-based manufacturer of high-performance solder balls for semiconductor packaging.
Hands-On Demos Now Available for Apollo Seiko’s EF and AF Selective Soldering Lines
06/30/2025 | Apollo SeikoApollo Seiko, a leading innovator in soldering technology, is excited to spotlight its expanded lineup of EF and AF Series Selective Soldering Systems, now available for live demonstrations in its newly dedicated demo room.