-
- News
- Books
Featured Books
- pcb007 Magazine
Latest Issues
Current IssueSales: From Pitch to PO
From the first cold call to finally receiving that first purchase order, the July PCB007 Magazine breaks down some critical parts of the sales stack. To up your sales game, read on!
The Hole Truth: Via Integrity in an HDI World
From the drilled hole to registration across multiple sequential lamination cycles, to the quality of your copper plating, via reliability in an HDI world is becoming an ever-greater challenge. This month we look at “The Hole Truth,” from creating the “perfect” via to how you can assure via quality and reliability, the first time, every time.
In Pursuit of Perfection: Defect Reduction
For bare PCB board fabrication, defect reduction is a critical aspect of a company's bottom line profitability. In this issue, we examine how imaging, etching, and plating processes can provide information and insight into reducing defects and increasing yields.
- Articles
- Columns
- Links
- Media kit
||| MENU - pcb007 Magazine
Estimated reading time: 5 minutes
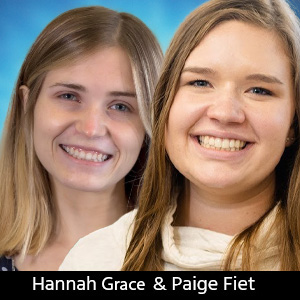
The New Chapter: Reimagining PCB Design in Education
I’ve been reminiscing about my college classes, especially the ones proving to be the most valuable in my early career. One class that has given me the upper edge in my new job was an independent study on advanced PCB layout, where I learned about the PCB design and manufacturing processes. In that class, I designed several boards, ranging from antennas to fun kits for students, and I learned more about fundamental hardware electrical principles and the mechanics behind a PCB.
Before taking this class, it felt like there were key concepts missing in my educational experience because I could not see the theory working in real life. Once I created my first PCB, I finally understood how concepts like trace width can cause an impedance change and how the placement of a component might affect the signal integrity of the circuit. Sparks went off in my brain as I began linking theory to a reality that felt previously out of reach. Learning PCB design in the classroom may give the next generation of students an opportunity to link theoretical understanding to reality and see how the foundation of electronics can come to life.
PCB design plays an important role in high-reliability fabrication, and there is an expectation for designs to adhere to safety protocols and standards. The PCB industry comprises about 30% of business/retail/computer industries and about 28% of the communications/telecom industries1. Designs range from small toys to giant aircraft, so it’s important that the designer works closely with the fabricator, even during the beginning stages, to ensure that standards and safety protocols are upheld during fabrication. Designers must design for reliability, while ensuring that the design meets the customer’s specifications throughout the product’s lifecycle. In fact, “for any new product, around 70-80% of production costs come from decisions made during the design phase.”2
Designers need the skills to work with fabricators, adhere to standards and safety protocols, and keep production costs low. What better way to gain those skills than learning them in the early stages of college and your career.
If I had not taken my PCB layout course, I would have needed to learn these things on my own. During the senior design process, projects often need PCB design or soldering—skills typically not offered in an electrical engineer’s curriculum. This leaves many students to learn soldering and PCB design either before or during the senior design process. Why is it that something so undeniably necessary for senior engineering students to know is left to learn on their own? In these situations, students miss out on the opportunity to learn important practices and industry standards. Sadly, they miss out on tips and tricks used in the industry for complex projects. Think how much further ahead they would be, and how much more they could contribute to sophisticated projects, if they came into a job already having some of these design and soldering skills.
Many graduating students entering a hardware-based workforce really need to possess a basic PCB skill set, but with PCB design and manufacturing so frequently left out of the curriculum, how will they build that strong foundation?
Many universities are already making headway toward integrating PCB design and assembly within their programs, including Carnegie Mellon, Rochester Institute of Technology, and Massachusetts Institute of Technology. Even at Valparaiso University—my alma mater—they integrated a one-credit introductory course this year. Students can choose and design PCBs, select and solder available parts for their boards, and work with manufacturers to ensure the design is up to industry standards.
George Mason University, for example, introduced students to a PCB design course that enabled them “to design at least a two-layer PCB from start to finish.”3 Students went through the entire PCB design process, from “getting acquainted with the general features” to “generating a bill of materials” and “ordering parts for the project.” Training on soldering and a tour of a PCB manufacturing lab helped students learn and understand the different steps within the PCB fabrication process, such as using a hot reflow oven and the proper utilization of solder paste. Interestingly, students also learned the importance of time management when designing a board, to “spend sufficient time building the circuit” that would ensure the board could be manufactured during the specified project time because simulation needs adequate time to ensure the circuit works properly. The course taught them the importance of starting the design process early enough to allow for design optimization.
Overall, students completed the class “more motivated and better prepared to tackle more sophisticated design projects.” To me, this shows that when someone can obtain a basic understanding and skill set, they’re ready to take on more rigorous design challenges. Students learn to manage their time while optimizing designs.
Even if colleges cannot fit in a semester-long course, I would love to see these topics taught in a few general engineering lab sessions to at least familiarize students in a hands-on setting. If neither option is available, I implore the greater electronics manufacturing industry to support their local IPC chapter. Together, we can pull industry forward.
When looking back on my college experience, our IPC chapter provided opportunities for us to learn skills like soldering and PCB design. The IPC Education Foundation even offered free courses to learn more about the PCB manufacturing process. The things I learned there I am now using whenever I am tasked with designing a PCB. With PCB design experience under my belt, I am better equipped to handle the unpredictable challenges that may come my way.
References
- The Global Printed Circuit Board Market: Key Insights, Forecasts, and Growth Outlook,” MKTPCB.com.
- “6 PCB Design Stats to Make You Look Smart Around the Water Cooler,” by David Marrakchi, Altium, Feb. 21, 2017.
- “Development of a Printed Circuit Board Design Laboratory Course,” by P. Kurtay, 2020 ASEE Virtual Annual Conference Content Access.
This column originally appeared in the October 2023 issue of PCB007 Magazine.
More Columns from The New Chapter
The New Chapter: The Benefits of Continuing EducationThe New Chapter: Navigating Maternity Leave in the Electronics Industry
The New Chapter: The Impact of Parasitics on PCB Design
The New Chapter: I’ve Found My ‘Why’
The New Chapter: Artificial Intelligence in PCB Design
The New Chapter: Lessons From the Best Engineer I’ve Ever Known
The New Chapter: Attracting ‘Generation Green’
The New Chapter: Dip Your Hand in the IPC APEX EXPO Candy Jar