-
- News
- Books
Featured Books
- pcb007 Magazine
Latest Issues
Current IssueThe Hole Truth: Via Integrity in an HDI World
From the drilled hole to registration across multiple sequential lamination cycles, to the quality of your copper plating, via reliability in an HDI world is becoming an ever-greater challenge. This month we look at “The Hole Truth,” from creating the “perfect” via to how you can assure via quality and reliability, the first time, every time.
In Pursuit of Perfection: Defect Reduction
For bare PCB board fabrication, defect reduction is a critical aspect of a company's bottom line profitability. In this issue, we examine how imaging, etching, and plating processes can provide information and insight into reducing defects and increasing yields.
Voices of the Industry
We take the pulse of the PCB industry by sharing insights from leading fabricators and suppliers in this month's issue. We've gathered their thoughts on the new U.S. administration, spending, the war in Ukraine, and their most pressing needs. It’s an eye-opening and enlightening look behind the curtain.
- Articles
- Columns
- Links
- Media kit
||| MENU - pcb007 Magazine
New Materials Simplify Fab and Design Processes
November 2, 2023 | I-Connect007 Editorial TeamEstimated reading time: 9 minutes
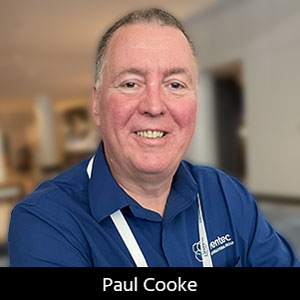
During PCB West, Andy Shaughnessy and Kelly Dack met with Paul Cooke, senior director of business development, Ventec International Group. In this interview, Paul discusses some of the global trends he’s seeing in new materials that address the issue of stacked microvia failure, and his drive to educate North American designers about the use of pure resin and no-flow materials.
Andy Shaughnessy: Paul, what’s happening with materials now, in Ventec, and across the industry?
Paul Cooke: We’ve developed some pure resin systems, and I’m now teaching designers how to use them. It’s part of my job to educate customers in North America and show them how these materials are being used with some of their new applications. I’m also showing them how to use our no-flow materials for high-speed applications. We've developed our Tec-Speed series of no flows for rigid-flex, because people designing rigid-flex for high speed really didn't have any other options. We've also developed pure resin systems for substrate technology, down to a half-mil thickness. These are low CTE, so they’re perfect for mounting ceramic packages on top of these materials.
Another trend we're seeing is a huge movement toward our polyimide materials, because it's one of the best polyimides on the market. North America is now starting to adopt this material. We own about 60% of European polyimide sales, and we're starting to see movement here in North America. We manufacture everything from PTFE to high-speed digital to IMS. We recently developed a new IMS material that is 10 watts/meter K which is the upper benchmark in the industry.
Kelly Dack: Paul, I work for an EMS provider, and customers come to us with designs that are already in prototype, and they want to gain volume by going to offshore sources. In your view, should our customers specify a certain material by brand name or just use a generic term?
Cooke: I spent the past 35 years as a field applications engineer, and I would teach them to use IPC slash sheets. However, the problem with these extremely high-speed digital type products, about 200 gigabytes and above, is that not all materials are drop-in equivalents. For others, they have to be designed, prototyped, and tested prior to mass fabrication. I also had customers who would choose to use materials for prototypes that they would be able to access in Asia. Therefore, they may use an Asian material here, knowing that their fab shops in China and Taiwan would have access to the same type of material and therefore have no issues with the design transferring from one fabrication location to another. I'd love to put the Ventec name on every print, but that’s not how it is.
Dack: What’s your view on supply chain issues with materials and availability? For instance, is the exotics and specialty materials market opening up, or is it still problematic?
Cooke: With PTFE, for instance, Ventec is currently at a two- to three-week lead time. If you specify an oddball size or thickness, we can basically manufacture that and have it to you in three weeks. This differentiates us from other material suppliers in my view. Ventec is a big enough company, about $200 million, to support the large Tier 1 companies. But we're small enough to be adaptable and flexible to customer requirements. We attempt to get forecasts for materials, but if a designer needs a material quickly, we can adapt and quickly manufacture it. Ventec’s main lot sizes are much smaller than the larger material manufacturers as well. We're not going to tell a designer, “By the way, you need to buy 200 sheets, even though you only want five.”
My colleagues out in the field and I have been told of supply chain issues with other materials suppliers. OEMs and designers want quick-term solutions, which Ventec can supply anywhere in the world, and its Ventec’s flexibility that is a key component to be able to accommodate them.
Dack: Has anything been developed in additives for the Z-axis? When we say coefficient of thermal expansion, we’re mainly concerned about the Z-axis, the vertical axis alongside a microvia. Most materials have some type of support—fibers, glass—laterally. With additives, when we laminate there's nothing going vertically in the Z-axis to hold this together. Have you seen any work on additives that will help in the Z-axis?
Cooke: Let me just say that glass is not your friend. Glass causes a great deal of CTE expansion. Ventec has developed non-reinforced materials, specifically pure resin systems, with a CTE of only 15 to 18 ppm, which aligns nicely with copper that is around 19 ppm. In a board over 100 mils thick, because of that Z-axis expansion, the external layers put a lot of stress on the microvias. Designers are taught that you have to use staggered microvias since the consensus is that it's not as reliable to utilize stacked vias. However, I did a study that indicates that stacked microvias with a low-CTE material are just as reliable. These builds survived 24 to 48 reflow cycles at 260°C, due to the low Z-axis thermal expansion of the materials. If a designer selects a material with high expansion, the CTE causes high expansion and contraction rates. Therefore, there is so much stress on a stacked microvia that they'll start to pull apart. We're just finishing another study for a white paper that will verify that by using a low-CTE non reinforced material you can reliably manufacture stacked microvias.
Dack: So, to get it straight, high resin content is great for stacked microvias.
Cooke: If it’s the right resin (laughs). If you use a high-CTE resin, no, that’s your enemy, and that's the problem. The problem occurs when you go to thinner dielectrics, like a 1067 dielectric, that has a very high resin content of 65–70%. If that resin has a ppm of 200 ppm above Tg, it will basically have a very high expansion rate every time you go through a sequential lamination. So, really no, you need to be using materials with 15–20 ppm CTE to avoid causing microvia failures.
Dack: Now, should a designer who wants to solve the stackup problem recommend moving to a certain material? How do they do that?
Cooke: They don't. They rely on the fabricator having the knowledge, and unfortunately, most of them don't. They're trying to use their standard materials to fix the problem, or they think it's a process issue. I know we can stack vias, and it's just because we didn't have some of these materials available in the past. Really, a designer or fabricator might not want to utilize two stacked microvias, but I can show you that you can go to five stacked microvias reliably. With the right material, process, and fabricator, you can build reliable product with multiple stacked microvias.
As I said, the problem is that the fabricators, and even some of the OEMs, always believed that this was a process issue. However, using these lower-CTE materials opens a process window. Even if the fabricator is not having his best day, it opens the window to give him a better chance of building a reliable product. I heard a fabricator recently presenting incorrectly that the solution is to use materials with higher Tg which will help but not prevent failures. This is because once the material reaches Tg, the high CTE rates will still cause microvia separation.
Yet, a lot of fabricators haven't experimented with these low-CTE materials. So, it's really a matter of educating them, which is why we’re doing white papers and showing them data to prove that you can actually do this. Another challenge you have is that even if fabricators are really confident and building stacked microvias, they will give you rules like, “We don't go below 5-or 6-mils via size as they say the solution is capture pad area larger is better, and we want a 0.7:1 aspect ratio.” If you’re doing a 0.65 pitch design or smaller, you can’t use 5-mil vias or larger and you want to go to 4 or 3. Instead of using thinner glass reinforced dielectrics with high resin content, you could be using a 1-mil or 2-mil pure resin system. It’s just a matter of educating the fabricators about what's available, and what you need to do to build a high-reliability product. North America is just so far behind Asia, which is way ahead of us in these types of technologies.
Dack: We’re still finding capability issues and getting no-bids for advanced capabilities. For instance, want to do 3-mil lines and spacing, but we get no-bids, because they say they can't do that. We also have customers who don't understand what's required for that technology.
Cooke: Right, because when you're going down to these finer lines and spaces, you're also designing in other leading-edge requirements. So, it's not just lines and spaces and smaller microvias; you’re also using, say, thinner dielectrics, etc. Designers used to come to me when I was a field applications engineer and say, “Tell me about your capabilities,” and I’d say, “No, because you’ll just design everything to the leading edge and we'll probably end up no-bidding, or our yields would be in the toilet.”
The other challenge is that the fabricators with these capabilities are the larger companies. This means that a smaller- or even medium-sized OEM struggles to get their prototypes/products manufactured due to their high mix low volume requirements and also due to their much smaller dollar spend. Hopefully as we help increase the capabilities of the smaller board shops here in North America, we will give these OEM’s more choice for fabrication and prevent single sourcing.
Dack: This has been great, Paul. Thanks so much.
Cooke: Thank you. I enjoyed it.
Additional content from Ventec International Group:
The Printed Circuit Designer’s Guide to… Thermal Management with Insulated Metal Substrates, Vol. 2 by Didier Mauve and Robert Art
The Solutions Guide to… Thermal Management by Didier Mauve and Ian Mayoh
The Printed Circuit Designer’s Guide to… Thermal Management with Insulated Metal Substrates, Vol. 1 by Didier Mauve and Ian Mayoh
Roundtable Discussion: Use of IMS Thermal Materials in Multilayer Stackups for Power Applications, with Chris Hanson and Denis McCarthy of Ventec, Rax Ribadia of Excello Circuits, and Pete Starkey, I-Connect007 technical editor.
You can view other titles in the I-007eBooks library here.
Suggested Items
Symposium Review: Qnity, DuPont, and Insulectro Forge Ahead with Advanced Materials
07/02/2025 | Barb Hockaday, I-Connect007In a dynamic and informative Innovation Symposium hosted live and on Zoom on June 25, 2025, representatives from Qnity (formerly DuPont Electronics), DuPont, and Insulectro discussed the evolving landscape of flexible circuit materials. From strategic corporate changes to cutting-edge polymer films, the session offered deep insight into design challenges, reliability, and next-gen solutions shaping the electronics industry.
Indium Corporation Expert to Present on Automotive and Industrial Solder Bonding Solutions at Global Electronics Association Workshop
06/26/2025 | IndiumIndium Corporation Principal Engineer, Advanced Materials, Andy Mackie, Ph.D., MSc, will deliver a technical presentation on innovative solder bonding solutions for automotive and industrial applications at the Global Electronics A
Gorilla Circuits Elevates PCB Precision with Schmoll’s Optiflex II Alignment System
06/23/2025 | Schmoll MaschinenGorilla Circuits, a leading PCB manufacturer based in Silicon Valley, has enhanced its production capabilities with the addition of Schmoll Maschinen’s Optiflex II Post-Etch Punch system—bringing a new level of precision to multilayer board fabrication.
Day 1: Cutting Edge Insights at the EIPC Summer Conference
06/17/2025 | Pete Starkey, I-Connect007The European Institute for the PCB Community (EIPC) Summer Conference took place this year in Edinburgh, Scotland, June 3-4. This is the second of three articles on the conference. The other two cover the keynote speeches and Day 2 of the technical conference. Below is a recap of the first day’s sessions.
American Made Advocacy: Supporting the Entire PCB Ecosystem—Materials to OEMs
06/17/2025 | Shane Whiteside -- Column: American Made AdvocacyWith the addition of RTX to PCBAA’s membership roster, we now represent the interests of companies in the entire PCB ecosystem. From material providers to OEMs, the insights of our collective members help us educate, advocate, and support legislation and policy favorable to America’s microelectronics manufacturers. The industry veterans who lead these companies provide valuable perspective, and their accumulated wisdom makes us an even stronger association.