-
- News
- Books
Featured Books
- design007 Magazine
Latest Issues
Current IssueShowing Some Constraint
A strong design constraint strategy carefully balances a wide range of electrical and manufacturing trade-offs. This month, we explore the key requirements, common challenges, and best practices behind building an effective constraint strategy.
All About That Route
Most designers favor manual routing, but today's interactive autorouters may be changing designers' minds by allowing users more direct control. In this issue, our expert contributors discuss a variety of manual and autorouting strategies.
Creating the Ideal Data Package
Why is it so difficult to create the ideal data package? Many of these simple errors can be alleviated by paying attention to detail—and knowing what issues to look out for. So, this month, our experts weigh in on the best practices for creating the ideal design data package for your design.
- Articles
- Columns
- Links
- Media kit
||| MENU - design007 Magazine
Insulectro: Education Begins with the Designer
November 2, 2023 | Andy Shaughnessy, PCBDesign007Estimated reading time: 7 minutes
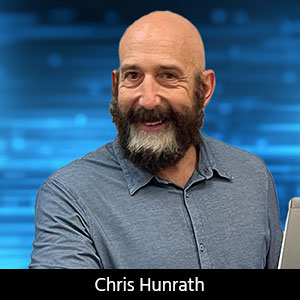
During PCB West, Insulectro held an educational showcase at its office in San Jose that focused on flexible, printed electronics, and advanced materials. After the courses concluded, I spoke with Chris Hunrath, VP of technology, about the company’s efforts to educate PCB designers, and the variety of material options available for customers who want to push the envelope of innovation.
Andy Shaughnessy: Chris, Insulectro has been holding these seminars for years, and you had a pretty solid event here today. How long have you been doing these?
Hunrath: We held our first one back when lead-free assembly was coming online, around 2006. A lot of our customers and their customers were not familiar with the requirements for the thermal survivability of the materials. The lead-free-compatible FR-4s were coming out, but baking requirements, alternative oxide, and other processes needed to be adjusted. We created this series of seminars that we typically hosted in our branches, and customers and OEMs from the area would come to our local branch. That began to evolve in 2005-2007.
Then in 2010, we did a seminar on flex technology. We went around the country and presented flexible materials in in conjunction with DuPont and some of our other suppliers. We did another group of courses in 2012. So, every couple of years, we would host these seminars. Later, we did seminars on high-speed circuitry and high-speed, low loss. So, you can see how that fits with the evolution of the industry.
Today’s seminar focused on flexible circuits and printed electronics; they go hand in hand because even though one's an additive technology and one's a subtractive additive technology, some of the applications and form factors are similar. The materials can be quite different sometimes, with Kapton being the foundation of flexible circuits. But these materials can also be the substrate material for printed electronics in high-temperature applications.
Shaughnessy: The presentation on PTC materials was really interesting; the resistance increases with the temperature so that you won’t get burned if you touch the application.
Hunrath: Sure, the positive temperature coefficient materials can be somewhat self-regulating in temperature. As the temperature goes up, the conductor resistance increases, and then you have less current flow. They don't run away like a conventional heater might, and it's not too hot to the touch. Think about a seat heater or a heated article of clothing.
We now have a brand of liquid polyimide that cures or coalesces, for lack of a better word, at a much lower temperature than prior traditional liquid polyimides, which usually cure in the 650°F range. These new liquids dry at 300°F, so they're very different, much more usable and easier to manage. But some of the polymer building blocks used in these systems came with what I'm going to call “chemical artifacts” that they really didn't need. Celanese had a technology to get the fluoro systems out of that final product, and they've been able to do that successfully.
Shaughnessy: It was pretty interesting seeing all of you interact with each other during the classes, like when you showed the DuPont people some things that you’d learned while working with their materials.
Hunrath: We’ve been partners with DuPont now for about 20 years. We just had a distributor recognition event at the DuPont Silicon Valley Tech Center. But DuPont has been a great partner. We work together. The information flows both ways, and I think we're closer to the customer, so we're able to report back to DuPont what we see happening in the field. DuPont has the material science background, and it’s been a great partnership for us over the years.
Shaughnessy: I think there’s definitely a need for classes like this, especially with so many PCB designers retiring or planning to retire, and taking their knowledge with them.
Hunrath: Sure. We want to keep this knowledge base alive. We are trying to recruit younger people within our company, and we're also trying to bring this information to our customers, who also have new employees. It is a challenge as people move on to other things or retire. We touch so many parts of the industry: manufacturing of the materials, fabrication, and sometimes even the OEMs and users. We think we're in a good position because we participate in three markets in a pretty big way—printed electronics, flexible electronics, and rigid PCBs.
Actually, printed electronics goes back to the early 1900s where people were printing conductive inks. Rear window foggers are printed electronics and they've been around for years. Believe it or not, some of that fired-on technology goes into the O2 sensors on your car, and in the airbag delivery systems. If you have a microwave oven or a dishwasher, very often they have membrane touch switches and printed electronics.
A printed electronics manufacturer’s In-Mold product line was projected to take over a lot of the membrane touch market. But, as you heard today, there are some downsides to that. There’s no tactile feedback with In-Mold; it's just capacitive, like the touchscreen on your phone. It's just not what people are used to. The upside is that it can be cheaper to manufacture, and everything is sealed so it should have a very long life. There are some definite reasons to pursue that technology, but people still want to connect—they want to feel that “click” when you push a button.
Shaughnessy: When you have a new customer come in, what kind of problems are they typically bringing to you? Do they know what they want, or do you have to walk them through it?
Hunrath: We get a variety of questions from new customers. Maybe the customer needs flexibility, so they might need some of those things on the PCB and flexible electronics side. Another example would be questions about a difficult construction. Let’s say the customer needs multiple two-ounce copper layers. They want to make sure that they avoid lamination voids, which are very bad for the reliability of the structure, but they don't want the overall thickness to be too high, so, what's the best solution?
Well, using a certain kind of prepreg for fill is better for donating resin to the resin-hungry spaces on that two months later, but not add to the overall thickness. Those are sometimes challenges that are hard to overcome. High speed is another area; they might want to minimize the amount of topography they put on the copper, and they want low-loss materials, or they want high-density interconnect. These are a few things that we get asked about on a routine basis.
Shaughnessy: You have a pretty interesting job, Chris. It must be nice having your own lab right next to your office.
Hunrath: Yes, I spend a lot of time in the lab, right next to my office. I’m never bored. That's what I tell young people coming into the businesses. You'll never be bored doing this. There’s a lot of opportunity because there are so many of us nearing retirement. I'm in my 60s now.
Shaughnessy: Me too. Where did the time go? So, is there anything else you want to mention?
Hunrath: Yes, we’ve now has partnered with EMC and Arlon and that's really exciting for me. They have a wide range of products. Arlon comes to us with some unique low-flow, building blocks for our rigid-flex business. Plus, they have the aramid fabric materials that are really neat. EMC has a range of low Z-expansion and low-loss materials that are fully commercialized that will give our customers a ton of capability. Arlon has a lot of products, so we’re trying to focus on a range. Our customers can do everything from FR-4 to high-reliability FR-4 to mid-loss, mid-Dk, all the way up to the extremely low-loss and ultra-low-loss products, but we won’t have 100 products. Maybe we have five in that space and then maybe another five in the aero and defense space. We like to have enough building blocks on the shelf that our customers don't have to go to the factory, and we can service them from our branch. We’re trying to do a good job of offering a nice blend of options, but also good access to the materials.
Shaughnessy: It’s been great talking with you, Chris.
Hunrath: Thank you for covering the showcase, Andy.
Testimonial
"In a year when every marketing dollar mattered, I chose to keep I-Connect007 in our 2025 plan. Their commitment to high-quality, insightful content aligns with Koh Young’s values and helps readers navigate a changing industry. "
Brent Fischthal - Koh YoungSuggested Items
Creating a Design Constraint Strategy
07/24/2025 | I-Connect007 Editorial TeamMost designers learn how to set their design constraints through trial and error. EDA vendors’ guidelines explain how to use their particular tools’ constraints, and IPC standards offer a roadmap, but PCB designers usually develop their own unique styles for setting constraints. Is there a set of best practices for setting constraints? That’s what I asked Global Electronics Association design instructor Kris Moyer, who covers design constraints in his classes.
Meet the Author: Beth Turner Explores Encapsulating Sustainability for Electronics
07/23/2025 | I-Connect007In a special Meet the Author edition of On the Line with…, host Nolan Johnson welcomes Beth Turner, senior technical manager at MacDermid Alpha Electronics Solutions. Beth is the author of The Printed Circuit Assembler’s Guide to… Encapsulating Sustainability for Electronics.
The Pulse: Design Constraints for the Next Generation
07/17/2025 | Martyn Gaudion -- Column: The PulseIn Europe, where engineering careers were once seen as unpopular and lacking street credibility, we have been witnessing a turnaround in the past few years. The industry is now welcoming a new cohort of designers and engineers as people are showing a newfound interest in the profession.
Copper Price Surge Raises Alarms for Electronics
07/15/2025 | Global Electronics Association Advocacy and Government Relations TeamThe copper market is experiencing major turbulence in the wake of U.S. President Donald Trump’s announcement of a 50% tariff on imported copper effective Aug. 1. Recent news reports, including from the New York Times, sent U.S. copper futures soaring to record highs, climbing nearly 13% in a single day as manufacturers braced for supply shocks and surging costs.
Symposium Review: Qnity, DuPont, and Insulectro Forge Ahead with Advanced Materials
07/02/2025 | Barb Hockaday, I-Connect007In a dynamic and informative Innovation Symposium hosted live and on Zoom on June 25, 2025, representatives from Qnity (DuPont's electronics business), DuPont, and Insulectro discussed the evolving landscape of flexible circuit materials. From strategic corporate changes to cutting-edge polymer films, the session offered deep insight into design challenges, reliability, and next-gen solutions shaping the electronics industry.