-
- News
- Books
Featured Books
- pcb007 Magazine
Latest Issues
Current IssueSales: From Pitch to PO
From the first cold call to finally receiving that first purchase order, the July PCB007 Magazine breaks down some critical parts of the sales stack. To up your sales game, read on!
The Hole Truth: Via Integrity in an HDI World
From the drilled hole to registration across multiple sequential lamination cycles, to the quality of your copper plating, via reliability in an HDI world is becoming an ever-greater challenge. This month we look at “The Hole Truth,” from creating the “perfect” via to how you can assure via quality and reliability, the first time, every time.
In Pursuit of Perfection: Defect Reduction
For bare PCB board fabrication, defect reduction is a critical aspect of a company's bottom line profitability. In this issue, we examine how imaging, etching, and plating processes can provide information and insight into reducing defects and increasing yields.
- Articles
- Columns
- Links
- Media kit
||| MENU - pcb007 Magazine
RoBAT Brings TDR Test to Bare and Assembled PCBs
February 19, 2024 | Andy Shaughnessy, Design007 MagazineEstimated reading time: 4 minutes
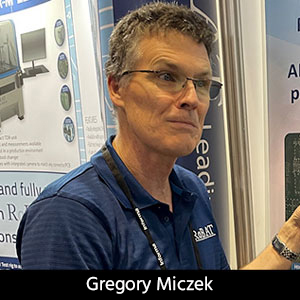
When most people in this industry think of time domain reflectometry (TDR), they envision an electrical engineer running signal integrity simulation on a high-speed PCB during the design cycle. But RoBAT has flipped the script, migrating this SI functionality downstream with a range of automatic TDR testers for bare and assembled boards.
In an interview at DesignCon, Gregory Miczek, global applications manager with RoBAT, discussed the company’s background and its expansion path from backplane defect analyzers to TDR testers for high-tech bare and assembled boards.
Andy Shaughnessy: Gregory, tell us about RoBAT and how you all wound up moving TDR downstream from its usual spot in the development cycle.
Gregory Miczek: Sure. RoBAT started back in 2001 as a core test electronics company dedicated to the design and manufacture of automatic test equipment specifically for backplanes. We were doing shorts and continuity tests primarily on a proprietary machine, developed to test multiple signals by taking a robotic head and plugging into connectors on a board to tell whether they're connected in the right place, and that sort of thing.
We tested shorts and continuity for years, and we made our robotic manufacturing defect analyzers an industry standard and sold many machines around the world. But as technology in the backplane industry evolved, we saw speeds and data rates constantly increasing to the point that now shorts and continuities were no longer enough of a test.
So, we adapted our robotic test machine to add signal integrity test capability. We started by repackaging somebody else's TDR system into our system. We then went through a series of iterations to progressively reduce the cable length. With each iteration, there was a continuous improvement to the TDR resolution. We reached a point where the limiting factor was the existing TDR measurement systems on the market. So, we developed and tuned our own TDR unit packaged specifically for carrying the measurement unit around on our robotic head. The latest generation has the TDR measurement ports at the interface to our tooling to connect to the board under test. Now, our rise time and signal loss through our interface is as small as you can possibly get. We don't think we can actually get it any better. At that time, our machines had been designed to find faults created during the assembly process using TDR.
However, we soon realized the machine was not only finding assembly-related faults but also ones created in the fabrication of the bare board. In fact, it found more bare fab manufacturing faults than assembly-related faults. It was clear to us at this point that we should develop a version of the machine to test bare fabs. The goal was a machine that retained the ability to make multiple connections (up to x24) to the PCB in one insertion and, therefore, make it possible to test 100% of the high-speed nets in a production test environment. We have designed high-speed impedance-controlled compliant tips to contact the bare fab, which can be configured to match any pad/hole layout. At this point, because we've packaged it this way, we can also adapt this to any configuration of bare printed circuit board in the high-speed test realm. What we are primarily looking for are backdrill depth discrepancies, slivers, impedance variations and skew
Shaughnessy: This type of tester could work in the IC realm as well, right?
Miczek: Yes, correct, we have versions of the latest RoBAT Scara machines that will test assembled backplanes and line cards as well as bare fabs. We actually test all the way out to ASICs and FPGAs, and we're starting to find faults with ASICs on the customers’ line cards that they had no way to ever find before because they didn't even know these faults existed. I work with our customers closely, and now they're telling us what they're finding. It's really fascinating.
Shaughnessy: That’s great. Your customers are doing R&D for you because the tool has so many potential uses.
Miczek: That’s right. We've been blessed with a great core group of primary customers. We have historically sold primarily to contract manufacturers. However, we have some OEM customers who have heard about our equipment. One customer in Toronto bought our equipment just to test their own products, and they are having great success testing bare line cards measuring each signal from both ends. In a fully populated line card, we can't access the SMT end of the net, but testing prior to SMT installation, we can access the end of the net from the bare SMT pads, for example, on a BGA array. In the fully populated configuration, we make tooling to fit the size of the daughter card connector, for example, a 16-way version, each with a dedicated TDR measurement channel. This allows us to test every single signal from the connector side and tell you that the ASIC is now faulty from a TDR perspective.
Shaughnessy: This qualifies as a game-changer, I’d say.
Miczek: We think so.
Shaughnessy: Thanks for speaking with me, Gregory.
Miczek: Thank you, Andy.
Testimonial
"We’re proud to call I-Connect007 a trusted partner. Their innovative approach and industry insight made our podcast collaboration a success by connecting us with the right audience and delivering real results."
Julia McCaffrey - NCAB GroupSuggested Items
TRI to Exhibit at SMTA Queretaro Expo 2025
07/16/2025 | TRITest Research, Inc. (TRI), the leading provider of test and inspection systems for the electronics manufacturing industry, is pleased to announce plans to exhibit at the SMTA Querétaro Expo 2025, scheduled to take place on July 24, 2025, at the Querétaro Centro de Congresos y Teatro Metropolitano.
Knocking Down the Bone Pile: Addressing End-of-life Component Solderability Issues, Part 4
07/16/2025 | Nash Bell -- Column: Knocking Down the Bone PileIn 1983, the Department of Defense identified that over 40% of military electronic system failures in the field were electrical, with approximately 50% attributed to poor solder connections. Investigations revealed that plated finishes, typically nickel or tin, were porous and non-intermetallic.
Meet the Author Podcast: Martyn Gaudion Unpacks the Secrets of High-Speed PCB Design
07/16/2025 | I-Connect007In this special Meet the Author episode of the On the Line with… podcast, Nolan Johnson sits down with Martyn Gaudion, signal integrity expert, managing director of Polar Instruments, and three-time author in I-Connect007’s popular The Printed Circuit Designer’s Guide to... series.
TTCI Joins Printed Circuit Engineering Association to Strengthen Design-to-Test Collaboration and Workforce Development
07/09/2025 | The Test Connection Inc.The Test Connection Inc. (TTCI), a leading provider of electronic test and manufacturing solutions, is proud to announce its membership in the Printed Circuit Engineering Association (PCEA), further expanding the company’s efforts to support cross-functional collaboration, industry standards, and technical education in the printed circuit design and manufacturing community.
Study on Resonance Mitigation in Metallic Shielding for Integrated Circuits
07/08/2025 | Maria Cuesta-Martin, Victor Martinez, Vidal Gonzalez Aguado, Würth ElektronikInherent cavity resonant modes often lead to significant degradation of shielding effectiveness, responsible for unwanted electromagnetic coupling. Cavity resonant modes of the metal shielding enclosure can produce two adverse problems: the mutual coupling among different RF modules and shielding effectiveness reduction of the metal enclosure. The cabinets serve to shield certain components from electromagnetic interference (EMI). However, these cavities present some resonance peaks at 5 GHz, making it impossible to use them at higher frequencies.