Estimated reading time: 5 minutes
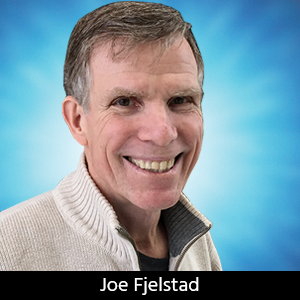
Flexible Thinking: Embedded Design—A Term With Multiple Meanings
With the seemingly endless ways that electronic products are worming their way into our lives, what was once “nice to own” is increasingly considered indispensable. The capabilities of these products have been driven by relentless improvements at every level of the manufacturing chain, from individual transistors (which are approaching Angstrom levels) to systems the size of buildings supporting Bitcoin mining and increasingly distributed AI products.
Along that chain of electronically interconnected products, the term “embedded design” is used at several points. Among high-level product developers, embedded design commonly refers to a process of designing and integrating end-product-specific computer systems into next-level systems to perform a chosen set of functions within the larger system, often with hardware and software also integrated, where the end products cover a wide spectrum of applications, everything from consumer electronics to automobiles, medical devices, military/aerospace products, and beyond.
A Little Background
Of greater interest here is the concept of the integral integration or embedment of electronic components (or electrical/electronic function) into the actual electronic interconnection substrate (typically a printed circuit). The concept of embedded/integrated devices and/or their function has deep roots in the printed circuit industry. Seventy-five years ago, the U.S. government published “Printed Circuit Techniques” to promulgate knowledge gained in electronics research during World War II. It was also meant to jumpstart the post-war electronics industry in the U.S., as it described methods for making resistors in situ and trimming them to value in place. Such methods have been employed ever since, though more often on the inner layers of multilayer boards.
The concept of distributed capacitance evolved with the introduction of multilayer PCBs in the 1960s and ’70s when it was realized that the stacking of multiple layers of circuits, including ground and power, provided an opportunity to incorporate distributed capacitance intrinsically embedded and made possible by the built-in parallelism of adjacent layers which naturally contributed to the capacitance between them. Material suppliers recognized the opportunity and began to explore the use of alternative materials for use in multilayer boards, including the use of high-permittivity dielectric materials to improve and better control distributed capacitance. Designers soon began considering capacitance a key factor in signal integrity and power distribution. The terms “buried capacitance” and “embedded capacitance” are much a part of the current printed circuit industry lexicon.
Embedded discrete components also have a long history, depending on how rigid one wants to define embedment. One of the first volume applications was “chip on board” (COB) products that ushered in the video game console industry in the mid-1970s. These structures could arguably embrace both ends of the spectrum described thus far. They were programmed chips attached to PCBs, wire-bonded to make interconnections, and encapsulated with epoxy. The method obviated the need for the packaging and subsequent solder assembly of the chip. The assembly was then given a housing identifying the game, and edge card connections were used to plug the module into the game player system.
Common Approaches
Turning attention to the embedment of other passive functions to provide discrete components, including discrete capacitors (as distributed capacitance as discussed earlier), resistors, and inductors, the most common approach has been the attachment of the component to etched lands on inner layers of the multilayer PCB using solder. This approach requires cavities be made in the prepreg and/or the inner layer materials used in constructing the board. Yet unstated but presumed to be understood, the purpose of embedding discrete devices has typically been to free up space on the outer surfaces of the printed circuit.
Beyond embedment of components, several techniques have been developed for forming the components in situ on inner layers. This was seen as an opportunity in the 1970s, as special laminates having bimetallic foils of copper and more resistive metals or coatings were developed to produce chosen resistor values by selectively etching the different foils to create the number of squares required in the resistive layer. However, the printing of a resistive material between ends of copper traces is a long-time practice. The resistor value can be “roughed in” by choosing the right value for the ink and the value “fine-tuned” by laser trimming the material to the desired value.
I had the notion 20 years ago that it would also be possible to create vertical resistors by drilling from one layer to another and filling the hole with a resistive material. The depth and diameter of the via would account for the number of squares and the resistive ink would be selected by the designer and the needs of the design. Once filled, copper would be plated over the top of the resistor material and a relatively small footprint resistor could be had. They could potentially be quite useful for termination resistors. (U.S. Patent No. 7049929B1)
Inductors are the other final passive function adapted for embedment into printed circuits. Inductors are well understood and follow a few established rules. The features that define inductance can be readily produced by standard printed circuit processing. In general, inductance is determined by the length of the spiral and number of turns. The spacing between turns will control the resonant frequency of the inductor. In general, a wider spacing will typically reduce capacitance and raise the inductance frequency. In a multilayer board, a multiple-layer inductor can be produced, increasing the number of turns without increasing the footprint.
In conclusion, the concept of embedded design is claimed by more than one segment of the electronics industry, though I believe that embedded component design in PCB construction predates the more recent interpretation of meaning. No matter, in the context of the application, the meaning should be clear to all.
Resources
For those wishing to take a deeper dive into the subject matter, Vern Solberg, an industry veteran and IPC Hall of Fame Award recipient, provides better understanding with additional detail and graphics.
Joe Fjelstad is founder and CEO of Verdant Electronics and an international authority and innovator in the field of electronic interconnection and packaging technologies with more than 185 patents issued or pending. To read past columns or contact Fjelstad, click here. Download your free copy of Fjelstad’s book Flexible Circuit Technology, 4th Edition, and watch his in-depth workshop series “Flexible Circuit Technology.”
This column originally appeared in the February 2024 issue of Design007 Magazine.
More Columns from Flexible Thinking
Flexible Thinking: The Key to a Successful Flex Circuit Design TransferFlexible Thinking: Flexible Circuit Technology—Looking Back and Forward
Flexible Thinking: Mind-tapping into January
Flexible Thinking: Another PCB Design Paradigm Shift in the Works
Flexible Thinking: Rules of Thumb—A Word to the Wise
Flexible Thinking: Musings on High Density Interconnections
Flexible Thinking: Integrated Passive Devices—Design Solutions With Many Benefits
Flexible Thinking: Mechatronics in a Flex World