Estimated reading time: 3 minutes
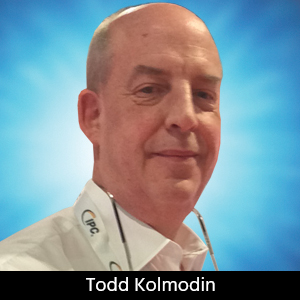
Testing Todd: Why 4-wire Kelvin?
As William Thomson (Lord Kelvin) once said, “If you cannot measure it, you cannot improve it.” This is truer today than ever before. With the advances in microelectronics and nanoelectronics, HDI, and buried active/passive components, the signature of the printed circuit is critical. High-speed substrates rely on signal transmission to be as pristine as possible. Minor changes can cause impedance changes in standing wave ratio (SWR) elevation, which leads to degraded performance.
As we know, there is a difference between low resistance threshold continuity testing and 4-wire Kelvin. Wait, maybe we don’t. Let’s take a look.
Continuity resistance in the standard electrical test (ET) theater relates to the end-to-end resistance of a single circuit. This is outlined in IPC-9252 for testing printed wiring boards. In this specification, referenced in many others as the standard for ET, Table 4-1 outlines continuity and isolation parameters for Class 1, 2, and 3 builds. These are referenced to Test Levels A, B, and C, accordingly. Here, continuity resistance for Class 3/Test Level C is 10 ohms, meaning point-to-point resistance in the circuit cannot exceed 10 ohms to be compliant. However, this just means that if the resistance is ≤ 10 ohms, all is well with the world.
However, with via plating, microwave circuits, and critical timing circuits, this can be a problem. This is where the high-resolution measuring of the 4-wire Kelvin bridge is recommended. Historically, 4-wire Kelvin has been used to identify plating anomalies where sight resistance changes may indicate taper plate or insufficient bonding in the microvias. Today, resistance values play into the overall performance of the circuit and, further, the performance of the final product.
We must remember that 4-wire Kelvin is different from standard continuity testing and enhanced equipment is required. We must also remember that fixture testers are not a good solution either. The main reason is the continuity threshold capability. Honestly, most 1980s and ’90s fixture testers will struggle to perform under a 5-ohm continuity threshold requirement unless they are in a strict maintenance program that refurbishes the cassettes and machine interfaces. Otherwise, contamination and oxidation will hamper the ability to test to the lower continuity requirement. Second, most fixture testers cannot perform a 4-wire Kelvin test due to the lack of system metering technology. The solutions are bench tests or flying probes.
Technology exists now where passive components can be tested to a known value. This is common with resistors, capacitors, and inductors. These values can be learned on machines and compared, or a predetermined value can be programmed. However, this is used in lower resolution requirements of usually 3 ohms and above. This is still a 2-wire measurement with better accuracy obtained by less wiring and wire resistance nulling on the machine. This is usually unavailable on fixture testers.
To realize the full potential of the high-resolution measurement requires the 4-wire Kelvin bridge. The theory is that as the stimulus is applied to the unit under test (UUT), the stray/contact resistance is shunted, leaving only true resistance. This allows for very fine measurements in the milli- and micro-ohm ranges. Using this methodology, the very fine changes in resistance can be measured. Here is where it has been very beneficial identifying plating anomalies. Thin copper in the via barrels will have a change in resistance that can be detected using 4-wire Kelvin and thus removed from the supply chain and stopping the latent field failure.
Build technology is advancing rapidly and 4-wire Kelvin has found a new niche in the high-speed substrate, HDI, and microwave markets. High-speed transmission and wave propagation are affected by resistance changes. These changes can cause changes in the reactance of circuits. In this arena, it is bad news; 5 ohms continuity in a circuit may be way too much. Designers are now adding predictability to their designs, which includes circuit resistance. We also see this in ceramic substrates where circuit resistance must be predictable in the 300 mohm to 1.2 ohm range. This requires measuring with 4-wire Kelvin hardware. This can be pre-programmed so that the test is invisible to the operator. Reports can be generated so that predictability can be reviewed.
This is why 4-wire Kelvin has emerged as an even more important tool in the ET arena. Standard testing, buried passive interrogation, and 4-wire Kelvin should be in the manufacturer's toolkit. If not, seek a reputable test supplier to help you along the way.
This column orginally appeared in the February 2024 issue of PCB007 Magazine.
More Columns from Testing Todd
Testing Todd: Why TDR?Testing Todd: Positivity Boosts Employee Morale
Testing Todd: Preparing Employees for the Long Haul
Testing Todd: Where Can We Improve?
Testing Todd: Turning Into the Wind
Testing Todd: Coming Back to Life—Design Recovery
Testing Todd: Decision Time—Invest or Delegate?
Testing Todd: Induction Junction, What’s Your Function?