Estimated reading time: 4 minutes
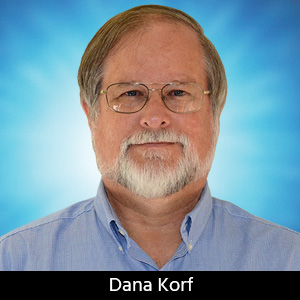
Dana on Data: eCAD PCB Design Deficiencies
Printed circuit board manufacturers are paid to create PCBs that reflect the supplied data package technical data. Decades ago, the industry started to send data packages that could not be built properly per the supplied documentation. Nobody seems to know when this started or the first manufacturer who said, “I’ll fix your error for free.”
In my column, I have highlighted key DFM issues and provided suggested remedies. But the data packages continue to show no improvement. Figure 1 presents a high-level breakdown of PCB data quality key issues. I always present this chart on the first day of my IPC course, “PCB Design for Manufacturing.” I have performed studies over the years of the quality of incoming data packages. The bottom-line consistent result is that less than 5% of these packages can be fabricated as-is.
It is interesting that all eCAD systems, from expensive to free, release common recurring design errors. For some reason, they are set up to assume that the fabricator will fix these problems for them. CAM software has excellent automated DFMs that fix these. I keep wondering why, if the CAM software can automatically identify and fix these, the eCAD software can’t fix them.
Here I’ll highlight the most common design errors that are not typically fixed by the eCAD software and remain for the PCB CAM engineer to identify and fix.
Solder Mask on Pad
It is assumed that the solder paste layer and/or the solder mask layer openings are there because a component will be soldered to those pads, or holes. There are often round pads without holes in them, in a trace that looks like they are intended to be test points. Automated CAM DFMs can designate pads that are covered with solder mask. More advanced systems can identify test points and ask whether these are intended to be covered with solder mask. The fabricator CAM person places the job on hold, and sends a request to the designer asking permission to open the solder mask for these locations. I propose that the eCAD system automatically open the solder mask for these pads.
Legend/Silkscreen on Pad
There are two primary reasons why the silkscreen can extend into the solder mask opening. The first is from the eCAD system where it is intentionally placed. The second reason is due to manufacturing capability, e.g., line width, registration. The CAM software and operator assumes that the designer did not intend to place legend under the solder joint, so the interferences are modified to clear the openings. It is rare that the designer wanted the legend to be under the solder paste deposition. I propose that the eCAD system automatically open the solder mask for these pads.
Thieving/Dummy Pads
Over 20 years ago, I worked for a multi-site company. Customers were complaining that different sites would ask for different TQ (technical query) modifications for the same design. So, we performed a study. Each site had their best product engineer review the exact same design and create the TQs. We compiled all the questions and were surprised that there were over 120 different proposed modifications raised, but there was only one request common to all sites. It was, “Can we thieve the layers?” I would suspect that this is still the most globally common question. I propose that the eCAD system automatically thieve or add dummy pads, as they are called in Asia, to the layers.
Multiple Drill Hits and Non-centered Drilled Holes
At design input, one of the first data clean-ups is to review the drill data. It is common to have multiple drill occurrences at the exact same location for the exact same hole size. This only takes seconds for the CAM automation to fix. It should only take seconds to fix in the eCAD/DFM system.
The same applies to moving the pads or holes in the vertical axis to align the hole in the center of the pad. This is performed to allow the maximum hole-to-copper distance to create more allowance for mis-registration. I propose that the eCAD system automatically remove multiple drill hits and align the hole to the pads.
The eCAD Plea
eCAD and its associated DFM software should automatically fix these errors prior to the final layout being saved, or before the production files are sent to the manufacturer. This does not require knowing anything about the fabricator’s capabilities. If the fabricator, front-end engineer, and CAM software can identify these issues, one can assume that the CAD library, netlist, and other eCAD tools should be able to identify these issues and fix them.
I have suggested (as have many others) over time that we should just produce the designs per the supplied documentation package without fixing any design issues. It would move the financial pain back to the designer which, hopefully, would in turn motivate them to fix the database faster.
If designers would set up their design flows, design rules, and DFM rules to fix these issues that are identified, manufacturing cycle time can be reduced, and editing variations between multiple suppliers would be reduced substantially.
Dana Korf is the principal consultant at Korf Consultancy LLC.
More Columns from Dana on Data
Dana on Data: The Missing AI-NPI LinkDana on Data: Merging 2D Electrical, 3D Mechanical Worlds
Dana on Data: Resurrecting IPC Class 1
Dana on Data: The Evolution of Fabrication Drawing
Dana on Data: The Insane PCB DFM Process
Dana on Data: Nuke the Netlist
Dana on Data: Simplify PCB Documentation
Dana on Data: IPC AME Standards Development Launched