-
-
News
News Highlights
- Books
Featured Books
- design007 Magazine
Latest Issues
Current IssueAll About That Route
Most designers favor manual routing, but today's interactive autorouters may be changing designers' minds by allowing users more direct control. In this issue, our expert contributors discuss a variety of manual and autorouting strategies.
Creating the Ideal Data Package
Why is it so difficult to create the ideal data package? Many of these simple errors can be alleviated by paying attention to detail—and knowing what issues to look out for. So, this month, our experts weigh in on the best practices for creating the ideal design data package for your design.
Designing Through the Noise
Our experts discuss the constantly evolving world of RF design, including the many tradeoffs, material considerations, and design tips and techniques that designers and design engineers need to know to succeed in this high-frequency realm.
- Articles
- Columns
- Links
- Media kit
||| MENU - design007 Magazine
Plastronics and the New IPC Guidelines for In-mold Electronics (IME)
April 11, 2024 | Barry Matties, I-Connect007Estimated reading time: 8 minutes
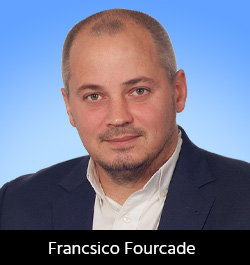
In the ever-evolving world of electronics, the roads for the integration of electronics assemblies into 3D structures continue to grow into a set of technologies used to produce 3D plastronics parts and revolutionize mainly the automotive industry. IPC has been developing standards for this set of technologies, led by Francisco Fourcade, IPC electronics technology standards manager. During this interview, he provides a perspective on these technologies and explains in detail, one of which is being rapidly standardized, who’s using it, and what some of the challenges are when new technologies are introduced.
Barry Matties: Francisco, will you explain this new and innovative set of technologies many people may not know much about?
Francisco Fourcade: 3D Plastronics refers to the set of technologies used to functionalize surfaces in 3D-molded structures. Over the past decades, some have been widely used as antennas and connectors in a variety of products, while in present times the technologies have evolved into many solutions that open the design limitations on surface functionalization of structures such as LSA-MID (laser surface activated molded interconnected device or 3D-MID/LDS), IME (in mold electronics), 3D direct deposition (aerosol or ink-jet printing), or LIFT (laser induced forward transfer). These technologies are suitable for a variety of applications and represent certain advantages and disadvantages with respect to each other.
I will use the example of the in-mold electronics as we are gearing to publish the first IPC standard. This particular manufacturing technology merges printed electronics and injection molding. Due to the nature and simplicity of both processes, it is especially attractive given the mass manufacturing possibilities it offers to provide cost-friendly solutions. The automotive industry has been pushing this technology forward to significantly reduce cost, weight, waste, and energy needed to produce automotive interior parts. Traditionally, you would have a PCB built and placed into a plastic molding with mechanical features that would interact with the PCB sensors, whereas in IME, your mechatronic device incorporates, in most cases, both electronics components and circuitry into the finished 3D molded part.
Matties: Will features be embedded in the substrate or printed onto the surface?
Fourcade: Depending on the design and end-use application, the selection of the technology enables the embedding of components and traces into the injection molded part, interconnecting components with conductive and structural adhesives. Using laser technologies also enables the selective metalization of a molded surface to allocate the soldering of components, which are later encapsulated or coated in the same manner as traditional printed boards. The limitation is really the substrate and its material properties, especially the temperature that these can withstand through processing. Instead of using FR-4, we use plastics and attach directly onto the plastic surface. The limit on temperature exposure depends on the type of plastic being used. You can only solder components on top of plastics when they are specifically engineered plastics like Polyether ether ketone (PEEK).
Matties: Can you laser solder onto the plastic, or are there other nontraditional soldering methods that work?
Fourcade: Today, there are many ways to solder onto plastic and several more in development, but the use of laser is well known and has proven a track record, even with pulse-driven laser beam selective soldering. For many decades, we have been able to do laser sintering on top of plastics in order to scribe and metalize traces to later solder components. This technology is called 3D molded interconnect device (MID) technology, laser surface activated MID or 3D-MID/LDS products. It sinters the design circuitry onto the surface of a 3D molded plastic for specialty applications. The laser process provide high resolution of traces as an advantage. In the case of LDS products, specific polymers (plastics) contain activators inside that allow for laser sintering to take place and the chemical bath metalizes the traces which can later be soldered.
Matties: What was the impetus for even bringing plastics and electronics together?
Fourcade: This trend and these technologies have been maturing for years. The merge has not been very popular during past decades due to patented technology restrictions, but they have been used for specific applications and the MID technology had an IPC standard published in the 1990s. We are gathering volunteers to start Revision A soon: ANSI/IPC-MB-380, Guidelines for Molded Interconnection Devices. Today the search for sustainable options and with new technologies also maturing, many experts and key stakeholders of this rapidly growing industry have come to IPC and asked for standards so industry can set today’s baseline for each technology. In particular the automotive industry is pushing this the most as the technologies provide a clear advantage in terms of sustainability: having an additive manufacturing process, being lighter weight, with less cost.
Matties: How much functionality will they get out of IME? Will it be as functional as a standalone board?
Fourcade: Not necessarily. Think about it as an extension of the much smaller module that controls the IME part, the part becomes your human to machine interface (HMI) or provides solutions in lighting and interactive haptic triggers. You're limited in different ways, such as component package configurations and in what thermal and pressure stresses they can withstand from both thermoforming and injection molding. For instance, here is the IME technology diagram showing the different layers: substrate, graphic inks, conductive inks, dielectric inks for cross-overs and multilayer capability, conductive and structural adhesives for component placement, all of which are thermoformed and injected into one piece.
The steps are simple:You use the initial polymer flexible film and screenprint the traces or features using conductive inks and dielectric inks—just as you do in printed electronics. The main difference is that plastronics takes it a couple steps further in processing by using thermal forming to create a 3D structured shape. During this step, the device is subjected to a temperature cycle and needs to account for the stretching of the different inks among other key requirements. The last step is injection molding, which puts a lot of pressure into the IME components, and this could consist of multiple injection molding shots
Matties: Who's the most likely candidate to make a substantial investment? Will it be the plastics companies, or maybe EMS providers or dedicated PCB fabricators? Is this a new value they can offer their customers?
Fourcade: I see it coming from both sides. OEMs are already pushing their Tier 1 suppliers and reaching out to their Tier 2 and 3 suppliers to get ahead; production is already happening in the automotive industry. Many of these applications are for automotive interiors, and testing is following OEMs strict regime of reliability testing.
Matties: Francisco, what is the state of the new IME standard?
Fourcade: IPC-8401, Guidelines for In-Mold Electronics, was a full proposal brought to the 3D Plastronics committee by Tactotek and it is now finalizing the Final Draft for Industry Review (FDIR) comment resolution to move shortly into the Proposed Standard for Ballot (PSB), the last step before publishing. It has been taken through our standardization process for the four main milestone, developing the content during the Working Draft as it’s finalized content takes shape into a FDIR document where we have a formal, 30-day review period open to industry to review and make comments. The IME standard went out for FDIR review in February. Between March and April, the comments we collected have to be resolved by the committee before we can move the IME document to the ballot stage.
Matties: Is it available for comment by the whole industry?
Fourcade: It's open to anyone in the industry regardless of whether they're part of the standard’s committee. Anyone can make a comment in the Final Draft document through the end of the 30-day review period. Usually, those who have access to the revision or the working draft are part of the committee. In this case, we reached out to the industry to share with them the final draft so industry can see where we are heading. Do they agree? Do they have something to say about it? Seeking input is key to making sure IPC standards are broadly represented and ultimately adopted by the industry.
At this point, the document is in great shape. It incorporates an agreed-upon definition and an introduction to all the different topics regarding the design, manufacturing process, materials and testing, serving as a great introductory guideline to anyone looking closely at using this technology.
Matties: What's the timing of the new standard to be published?
Fourcade: We are finishing up the comment resolution of the FDIR phase by the end of April. We are looking to go to ballot in May and keep our target publication of June/July.
Matties: Thinking about design, how will that work? Will it be a traditional circuit designer? Are design tools ready for this technology?
Fourcade: The design can be done by a design house, outside source, or in-house. Part of the standardization roadmap is putting together a couple of design standard to support the most used technologies. Yes, there are currently in the market design tools that support both MID and IME.
Matties: Will there be new IPC design training courses to help support this?
Fourcade: Not at the beginning stages. I want to push this envelope further, but what we need now is a baseline set of requirements that allow the industry to continue innovating. Training usually comes after standards have been established and industry has consensus on what is needed.
Think about it like this: With this technology, you now have the ability to break through some of the boundaries set by traditional PCBs. Certain X and Y limitations need to be well addressed when preparing the design. The breakthrough that these technologies are bringing to mass manufacturing is continuously evolving the design boundaries for system integration.
Matties: Fran, this is interesting and exciting technologies, and we look forward to seeing where this goes. Thank you.
Fourcade: I agree, Barry. Thank you for giving me an opportunity to explain it further.
Suggested Items
I-Connect007 Editor’s Choice: Five Must-Reads for the Week
06/13/2025 | Marcy LaRont, I-Connect007Today is Friday the 13th, and in much of Western folklore, this is a day when bad luck is lurking. But while Friday the 13th may top Western superstition charts, the global calendar is sprinkled with its own unlucky legends. In Spain and Greece, the bad juju lands on Tuesday the 13th—a day linked to Mars, the god of war, and naturally, chaos. In Italy, it’s Friday the 17th that is feared, thanks to the Roman numeral XVII, which can be rearranged to spell VIXI—Latin for “I have lived” (a poetic way of saying you’re dead).
Roll-to-Roll Technologies for Flexible Devices Set to Grow at 11.5% CAGR
06/11/2025 | GlobeNewswireAccording to the latest study from BCC Research, the “Global Markets for Roll-to-Roll Technologies for Flexible Devices” is expected to reach $69.8 billion by the end of 2029 at a compound annual growth rate (CAGR) of 11.5% from 2024 to 2029.
Qualcomm Acquires Autotalks to Boost V2X Deployments
06/06/2025 | Qualcomm IncorporatedQualcomm Incorporated announced that its subsidiary, Qualcomm Technologies, Inc., has completed the acquisition of Autotalks, an industry leader in direct vehicle-to-everything (V2X) communication solutions.
Mycronic’s Global Technologies Acquires Surfx in the US
06/03/2025 | MycronicMycronic’s Global Technologies division has acquired Surfx Technologies, a company headquartered in the US, providing atmospheric plasma solutions for surface treatment, including cleaning and active oxide removal.
Delta Thailand Reinforces 4IR Leadership and Smart Energy Vision at i-Forum 2025
06/02/2025 | Delta ThailandDelta Thailand reaffirmed its role in advancing industrial automation and sustainable innovation at i-Forum 2025. Held on May 9 by the Faculty of Engineering at Kasetsart University in Bangkok, the forum focused on the theme “Leading the 4IR Revolution: Key Lessons from the WEF Global Lighthouse Network.”