-
- News
- Books
Featured Books
- pcb007 Magazine
Latest Issues
Current IssueInventing the Future with SEL
Two years after launching its state-of-the-art PCB facility, SEL shares lessons in vision, execution, and innovation, plus insights from industry icons and technology leaders shaping the future of PCB fabrication.
Sales: From Pitch to PO
From the first cold call to finally receiving that first purchase order, the July PCB007 Magazine breaks down some critical parts of the sales stack. To up your sales game, read on!
The Hole Truth: Via Integrity in an HDI World
From the drilled hole to registration across multiple sequential lamination cycles, to the quality of your copper plating, via reliability in an HDI world is becoming an ever-greater challenge. This month we look at “The Hole Truth,” from creating the “perfect” via to how you can assure via quality and reliability, the first time, every time.
- Articles
- Columns
- Links
- Media kit
||| MENU - pcb007 Magazine
Estimated reading time: 3 minutes
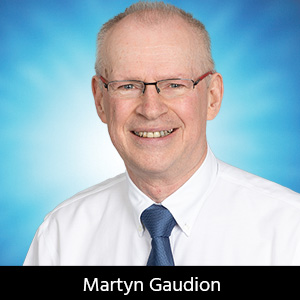
The Pulse: Drilling Down on Documentation
How did a product aimed at signal integrity end up being more about documentation? For a little backstory, the Polar team has an unspoken “no business speak” rule at certain times. So, why is this column titled “Drilling Down?” I find it fascinating when a company sets off in one direction, but customers steer it in another. That’s what has happened here as customers took a product down a fork in the road we couldn’t predict. Your destination isn’t always where you initially set off to go, and that’s how we got to our subject of drills and drill documentation.
Laser-focused, But Rotating Drills Still Play a Major Role
Conventional drilling has come a long way, and from a signal integrity perspective, the advent of precision-controlled depth drilling—especially when combined with contact detection—has transformed the high-speed performance of thicker boards, eliminating troublesome via stubs which behave to the signal as though they are twice as deep electrically as they are physically. Historically, you had to calculate the stub length, which would cap the maximum frequency at which a channel could operate.
Backdrilling the via can release the performance of the channel. The increased availability of PCB drilling machines with precision depth drilling has revolutionized the signal integrity performance of high-layer count PCBs. I have often mentioned that good modeling tools can't fix an inherent design flaw or limitation. In the case of via stubs, the modeling tool can flag where stub length becomes an issue and direct the PCB technologist or designer to deploy back drilling in the appropriate cases.
Via Documentation Fills a Variety of Applications
Aside from backdrilling, where the unused stub of the via is removed, vias can be treated in myriad ways to suit the specific application or functional area of the PCB. In high-power applications, the via may be copper or conductive epoxy-filled. Both methods aid in reducing the resistance of the via; aiding high-power applications have the added benefit of increasing the thermal conductivity and helping heat exit the PCB in a managed way.
Vias may also be filled non-conductively simply to prevent the entrapment of contaminants and for increased reliability.
The variety of options and implications of getting the via fills and styles incorrect mean that clear documentation is vital for supply chain communication.
Conclusion
I started my column talking about Polar’s informal ban on business speak—no reaching out. We email or call each other, no “going forward,” no “dog and pony shows,” “deep dives” (unless compressed gasses and seawater are involved), and certainly no circling back or “Let’s ‘parking lot’ this.” So, why does the title focus on drilling down? It must be on the list of “verboten” words and phrases. In this case, I used the words literally as this article is all about the increasing need for drill documentation in PCB stackups.
I also mentioned that sometimes a product doesn’t end up where you thought it would. In the early 2000s, Polar was nudged in the direction of providing a simple stackup documentation tool—SB200, the forerunner of today’s Speedstack. With the aim for a no-frills stackup tool, we added impedance control to the tool as that was what we were known for then. Over time, we added more impedance capability and extended the tool to cover insertion loss. At the same time, there was a drip, drip, drip of requests for more drill-related documentation. Back then, there was some HDI, but nothing like the widespread adoption of complex drilling we see now. Now, the prime drivers of Speedstack are customer requests on the documentation side, especially drill-related ones, plus the sharing of that documentation information with other tools in use by the industry. It will be interesting to see where our customer base takes us in the next 20 years.
Drilling capabilities have changed radically and the variety of drills and fills available to fabricator and designers mean that a variety of challenges in high power and high speed can be addressed in ways that would have seemed impossible or just an R&D dream a mere 10 or so years ago.
Martyn Gaudion is managing director of Polar Instruments Ltd. To read past columns, click here. Martyn is the author of The Printed Circuit Designer’s Guide to… Secrets of High-Speed PCBs, Parts 1 and 2.
This column originally appeared in the April 2024 issue of Design007 Magazine.
More Columns from The Pulse
The Pulse: Design Constraints for the Next GenerationThe Pulse: Ultra Upgrade Unknowns—What’s Coming for UHDI?
The Pulse: Commonsense Cost Cutting
The Pulse: Overconstraining: Short, Slim, and Smooth
The Pulse: New Designer’s (Partial) Guide to Fabrication
The Pulse: Simplest Stackups Specified
The Pulse: Rough Roughness Reasoning
The Pulse: Industry Organizations Keep Knowledge Alive