-
- News
- Books
Featured Books
- pcb007 Magazine
Latest Issues
Current IssueInventing the Future with SEL
Two years after launching its state-of-the-art PCB facility, SEL shares lessons in vision, execution, and innovation, plus insights from industry icons and technology leaders shaping the future of PCB fabrication.
Sales: From Pitch to PO
From the first cold call to finally receiving that first purchase order, the July PCB007 Magazine breaks down some critical parts of the sales stack. To up your sales game, read on!
The Hole Truth: Via Integrity in an HDI World
From the drilled hole to registration across multiple sequential lamination cycles, to the quality of your copper plating, via reliability in an HDI world is becoming an ever-greater challenge. This month we look at “The Hole Truth,” from creating the “perfect” via to how you can assure via quality and reliability, the first time, every time.
- Articles
- Columns
- Links
- Media kit
||| MENU - pcb007 Magazine
Estimated reading time: 4 minutes
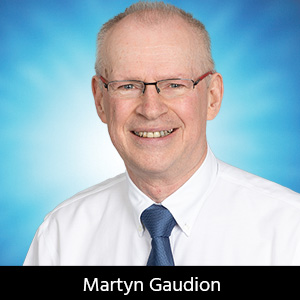
The Pulse: Overconstraining: Short, Slim, and Smooth
Engineering is both an art and a science. The design engineer’s task is (almost) always to bring product to market that meets specifications at the best and most economical price suited to the appropriate end use requirements. From a PCB perspective, designers are faced with a bewildering and almost overwhelming choice of materials at their disposal.
Design Focused to Minimise Costs
Small is beautiful in every respect, especially when it comes to high speed and high reliability. First, put the spotlight on:
Short: By keeping high-speed traces as short as possible, the risk of signal reflections causing problems can be minimized. PCB traces always operate as transmission lines, but if the length is kept short compared with signal rise time, their effects are benign. Likewise, at higher speeds, when copper and dielectric losses become significant, the nature of these losses is proportional to trace length, so if you can arrange a design to halve the length of the high-speed serial busses, then you halve the losses. This may enable you to adopt a more economical base material or a more standard copper surface.
Slim: By this, I mean minimizing the Z-axis height. A low layer count board and a thinner board will yield better thermal reliability and will minimise the length of vias and avoid the need for backdrilling those troublesome via stubs. While on the subject of avoiding stubs, I recall Dr. Eric Bogatin once mentioning that it might be a better route to take a critical signal using a conventional via from top to bottom of the PCB and then back up to use two vias with minimum stub length when transitioning the trace one or two layers where backdrilling is not economical or possible. If anyone has tried this, I would be delighted to hear from you.
Smooth (as necessary): Smooth copper is great for high speed signals, but for reliability not so much, so keeping the traces as short as possible allows you to use rougher copper whilst keeping losses under control. Of course, materials are improving as are bonding methods, and one day, the use of chemical adhesion promoters on copper may obviate the need for rough copper to make a reliable bond. Chemical adhesion promoters are what help to bond epoxy to glass fiber, but for copper, these treatments still have a cost and equipment burden. However, I can see a day when perhaps this paragraph will obsolete itself.
(Mis)communication-driven constraint: In these times, engineering has become so specialised it can be challenging to communicate requirements across disciplines where the terminology is so unique to each skill. This is often where the role of the PCB technologist comes into play, bridging the knowledge gap between designer, procurement, fabricator, and material supplier, ensuring that materials are not overspecified. In a previous life, I had an experience where a lack of supply chain communication caused significant wastage and could have been easily fixed with clear and open communication. Components were sourced with a 2% specification, and on inspection, all components received were precisely centered on +2%. The buyer insisted this was just new technology and because the parts were laser-trimmed they were precisely on specification. In practice, this meant 50% met the specification, and 50% were outside of tolerance. After much pressure, I travelled to meet the supplier, who proudly showed the process of making the parts “on spec.” No one had clarified to the laser trim operator that 2% should be the limit and the spec was ±2%. To be fair to the laser operator, they were nontechnical, but they could drive the trimming process very well indeed, and once they understood they were shooting for 0% rather than +2, all the parts came in exactly centered. Such an easy miscommunication, but the enemy was in the procurement chain, which tried to clamp down on awkward questions and be defensive.
Modeling: Back to the main focus of overconstraining, knowing which levers to pull in terms of constraint is now so much easier, given the wide variety of simulation tools available to designers. By simulating up front, it is much easier to explore design space and see where advanced materials are mandatory, and where there may be flexibility to use a lower specification of materials. PCB designers have access to a range of brokers who, at the top end, are very familiar with available materials, or to an in-house PCB technologist. Alternatively, most base material and chemistry suppliers have applications people who can guide you to the correct material choice, and because there is so much competition in material supply, it is in their interest to steer you in the most economical direction for your project.
Conclusion
PCB designers need to balance the end-use application of the product with time-to-market and material lead times with high speed and reliability considerations. Modeling and simulation of PCB characteristics and clear communication with supply chain partners are vital to delivering a product that is “correctly constrained” for the application. More than ever, it is important to understand that the differing skill sets and terminology across the supply chain mean that open and clear communication is vital.
Martyn Gaudion is the author of The Printed Circuit Designer’s Guide to… Secrets of High-Speed PCBs, Parts 1 and 2.
This column originally appeared in the May 2024 issue of Design007 Magazine.
More Columns from The Pulse
The Pulse: Design Constraints for the Next GenerationThe Pulse: Ultra Upgrade Unknowns—What’s Coming for UHDI?
The Pulse: Commonsense Cost Cutting
The Pulse: Drilling Down on Documentation
The Pulse: New Designer’s (Partial) Guide to Fabrication
The Pulse: Simplest Stackups Specified
The Pulse: Rough Roughness Reasoning
The Pulse: Industry Organizations Keep Knowledge Alive